Recently, Tesla Motors Inc. acquired Riviera Tool, LLC, a leading West Michigan auto supplier, and renamed it Tesla Tool and Die Factory. This strategic acquisition bolsters Tesla’s production capabilities, particularly as it gears up for the release of the Model X SUV, while also highlighting the importance of sheet metal fabrication in driving automotive innovation forward.
Sheet metal fabrication serves a critical role across a broad spectrum of applications in modern-day industrial practices. From vehicles on our roads, planes in the sky, and household appliances, sheet metal fabrication has extensive applications. It is a complex yet flexible process that turns metal sheets into vital parts in many life aspects.
This concise guide covers the fundamentals of fabrication techniques and the variety of materials involved, equipping you with the knowledge to navigate the industry effectively.
What Are Sheet Metal Fabrication and Its Working Process?
Sheet metal fabrication is a transformative manufacturing process that reshapes thin, flat pieces of metal into a variety of components and structures that are vital across different industries. The process involves selecting a suitable metal, like aluminum, steel, or copper, based on the project’s requirements. After that, the required designs are drafted using advanced software to ensure precision. Following this, the metal sheets are skillfully cut into designated shapes using different techniques, all while ensuring sharp accuracy and clean edges. Then, the cut pieces are molded into their final forms through processes such as bending and stamping. Finally, pieces are assembled, often through welding, to construct the complete product, which is then finished with treatments like painting or coating to enhance durability and aesthetics.
Manufacturing Methods of Sheet Metal Fabrication
Here are the different manufacturing methods used in metal fabrication:
Cutting
Cutting is the initial step in the process, where metal sheets are transformed into precise slices to create specific shapes or designs. This process utilizes advanced methods like laser cutting and waterjet cutting.
Stamping
Stamping in sheet metal fabrication involves pressing the metal into a die to imprint shapes, patterns, or designs. This method can produce a range of effects, from simple indentations to complex three-dimensional forms. Using this method, you get both aesthetic and functional enhancements to the metal sheet.
Bending
Bending transforms flat sheet metal into angular or curved shapes by applying force. Methods like press brake bending and roll bending are well-known blending techniques.
Available Materials for Sheet Metal Fabrication
The selection of material is a critical decision in sheet metal fabrication. It influences not only the manufacturing process but also the performance and longevity of the final product.
Some common materials include:
Bronze
Bronze offers a remarkable blend of durability and corrosion resistance. It is famously used in sculptures, bearings, and electrical connectors. Its natural elegance over time adds aesthetic value to your product, making it a favored choice for artistic and decorative projects.
Stainless Steel
Stainless steel provides exceptional resistance to rust and tarnishing. Combined with its ability to withstand high temperatures, this attribute of stainless steel is ideal for use in the medical, food service, and automotive industries. Its strength and durability also make it a reliable choice for structural applications.
Aluminum
Aluminum stands out for its lightweight yet strong profile, making it a preferred material in the aerospace and automotive industries. Its excellent corrosion resistance and conductivity also find applications in electrical components and consumer electronics.
Copper
Copper is highly valuable for its unparalleled electrical conductivity, which makes it an important part of the electrical industry for wiring and components. Beyond its functional applications, copper’s thermal conductivity is crucial in heat exchangers and radiators as well.
Is Welding the Same as Sheet Metal Fabrication?
No, welding is one technique within the whole sheet metal fabrication process. It primarily fuses metal parts together to form a strong joint. While welding is an integral component of the fabrication process, many other steps are involved in transforming raw sheet metal into finished products.
MY Prototyping
Choosing MY Prototyping’s sheet metal fabrication service for your next project opens your door to various possibilities. This sheet metal fabrication shop stands out for its commitment to precision, efficiency, and unparalleled quality. Not to mention that they also provide highly custom sheet metal fabrication solutions for your personalized projects.
With their sheet metal services, you gain access to a shop that is famous for rapid turnaround times, as you receive quotes within 24 hours and manufacturing times that can be as quick as a single day. This agility is backed by the reassurance of ISO 9001:2015 certification, which means that every workpiece produced meets the quality standard.
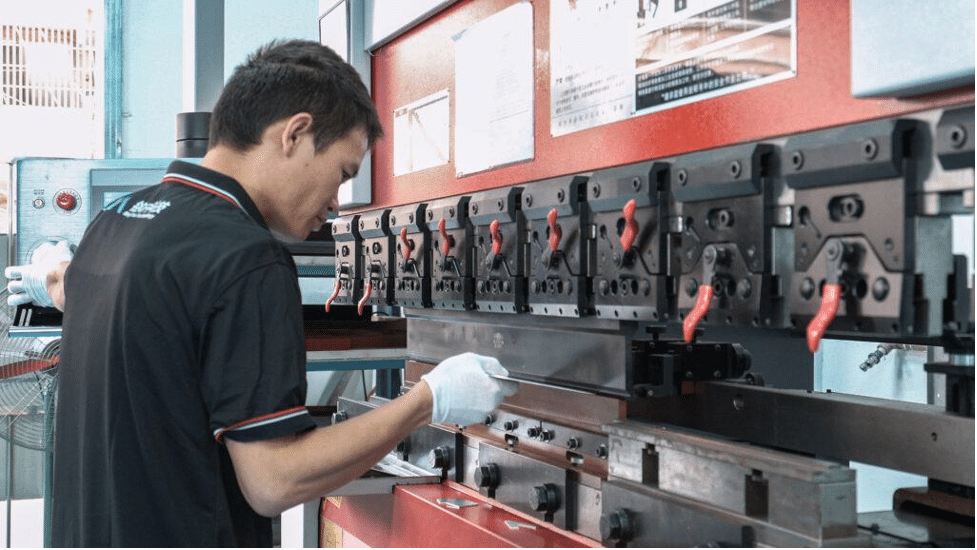
Also, there is no minimum order quantity, which makes this sheet metal supplier even more famous.
One of the most compelling aspects of MY Prototyping’s offering is the diversity of materials and processes at your disposal. This is further enhanced by the option to choose from a wide range of materials, including but not limited to aluminum, stainless steel, and copper.
Moreover, MY Prototyping understands the importance of the finishing touch. With a variety of surface finishing options available, you can ensure your products not only function optimally but also align with your desired look and feel.
Wrapping-Up
MY Prototyping has served over 2,000 companies and produced more than 200,000 unique parts for clients in over 50 countries during its 14+ years in business. Over the years, MY Prototyping has evolved into a one-stop solution for design, low-volume manufacturing, large-scale production, surface finishing, and product assembly. They excel in swiftly turning innovative ideas into high-quality, tangible prototypes, thereby accelerating the product development process.