In the world of 3C devices—Computers, Communications, and Consumer electronics—expectations are getting higher and higher. Today’s consumers are no longer satisfied with devices that simply function well. They demand products that feel premium, perform flawlessly in various environments, and retain their form and function over time.
This shift in consumer demand puts intense pressure on brands and manufacturers to choose materials and processes that can deliver on all fronts. Liquid Silicone Rubber (LSR) injection molding comes into the spotlight. Known for its unique combination of flexibility, strength, safety, and precision, LSR injection molding has emerged as a key solution for manufacturing modern 3C needs.
Understand LSR: What Makes it Special?
To understand why LSR injection molding is ideal, we need to first look at the material itself. Liquid Silicone Rubber (LSR) is a high-performance elastomer with characteristics that set it apart from conventional materials like thermoplastic elastomers (TPE). Let’s break it down!
Chemical Structure and Characters of LSR
LSR is part of the silicone elastomer family—better-termed polysiloxanes. It features a Si–O–Si backbone with organic side groups (like methyl or vinyl) attached to the silicon and is supplied as two liquid components (A and B) that are mixed and vulcanized—typically via a platinum-catalyzed reaction.
This distinctive chemistry gives LSR exceptional thermal stability, chemical inertness, and hydrophobicity because of methylated siloxane chains.
Physical Properties of LSR
LSR’s structure results in a low-viscosity liquid before curing—ideal for filling microfeatures and thin walls in molds. Post-curing, LSR transforms into a flexible yet resilient elastomer that maintains excellent elasticity, high tear and tensile strength, and low compression set across a vast temperature window—from roughly –60 °C to +250 °C, or even broader depending on the formulation.
It also withstands UV, ozone, humidity, and harsh chemicals while being biocompatible, hypoallergenic, fire-retardant, odorless, and tasteless.
LSR vs TPE: The Differences in Different Types of Rubber
Thermoplastic Elastomers (TPEs) and LSRs are both soft, rubbery materials—but they differ fundamentally:
Feature | LSR (Liquid Silicone Rubber) | TPE (Thermoplastic Elastomer) |
Material Type | Thermoset – undergoes irreversible cross-linking when heated | Thermoplastic – melts and re-solidifies without chemical change |
Temperature Range | Very wide: −60 °C to +200 °C; excellent at extremes | Moderate: −40 °C to +130 °C |
Mechanical Properties | Superior tear strength, low compression set, consistent elasticity | High elasticity, but shear sensitive and low resistance to aromatics |
Chemical & UV Resistance | Excellent: ozone, weather, solvents, chemicals, biocompatibility | Good weather & chemical resistance; better abrasion |
Processing Ease | Requires precise injection molding, 2-part dosing, post-cure; molds need tight tolerances | Simpler injection molding with pellets; fast cycles; recyclable scraps |
From Material to Method: What Is LSR Injection Molding and Why It Matters for 3C Devices?
Now that we understand the unique characteristics of Liquid Silicone Rubber (LSR), the next question is: how to deliver the high-performance parts that 3C devices demand? The answer lies in LSR injection molding—a manufacturing process designed to unlock the full potential of this versatile material.
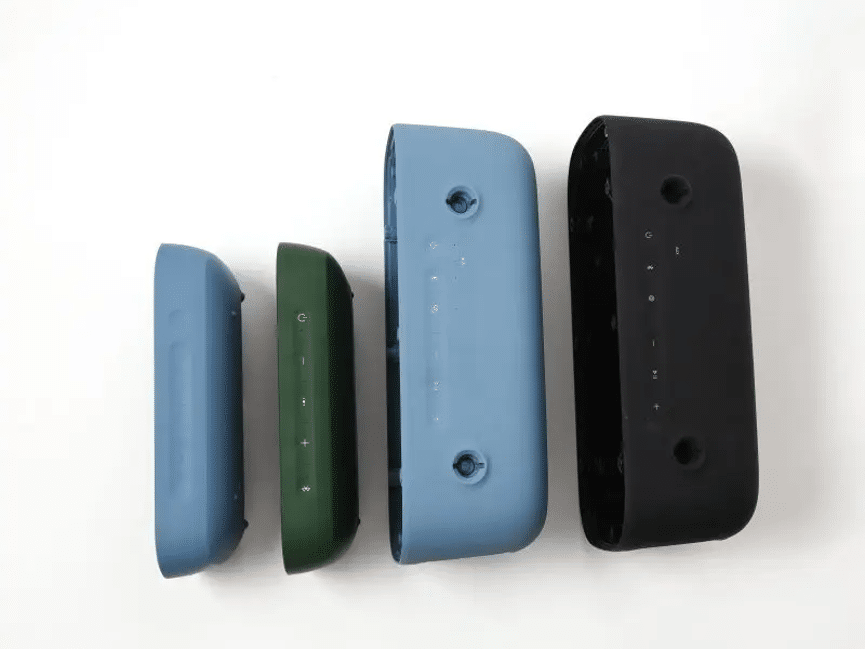
What Is LSR Injection Molding?
LSR injection molding is a high-precision, automated manufacturing process where silicone rubber is mixed and injected into a closed mold under pressure and then cured (or vulcanized) at elevated temperatures.
What are the Benefits of LSR Injection Molding for 3C Devices?
For manufacturers of smartphones, wearables, accessories, and other consumer electronics, LSR injection molding offers several advantages that align directly with product requirements and user expectations:
High Precision for Complex Designs: With its low viscosity before curing, LSR can flow into intricate mold cavities—perfect for components like gaskets, seals, and waterproof enclosures that demand geometric accuracy.
Superior Thermal and Environmental Resistance: LSR-molded parts withstand extreme temperatures, UV exposure, and moisture—ideal for wearables, outdoor gadgets, or rugged tech gear.
Enhanced Durability and Flexibility: LSR parts are tough yet flexible, resisting tearing, cracking, or deformation even after long use—extending the lifecycle of device components.
Skin-Friendly and Hypoallergenic: For products in direct contact with skin, such as smartwatch straps or earbuds, LSR offers medical-grade biocompatibility, ensuring comfort and safety for daily wear.
Aesthetic Finish and Color Stability: LSR allows for vibrant pigmentation, matte or glossy surfaces, and consistent texture—supporting the sleek, premium look expected in today’s electronics.
Design Freedom with Multi-Shot or Overholding Options: LSR can be over-molded onto plastics, metals, or glass, enabling multi-material assemblies that integrate touchpoints, seals, or shock absorption directly into the device design.
What are 3C Devices That Use LSR Injection Molding?
LSR injection molding is widely applied in 3C devices where durability, precision, and comfort are essential. Common applications include:
- Smartphone Accessories: Protective cases, button seals, and camera gaskets.
- Wearables: Smartwatch straps, sensor covers and sweat-resistant contact surfaces.
- Earbuds and Audio Devices: In-ear tips, soft-touch housings, and connector overmolds.
- Computer Peripherals: Silicone keypads, anti-slip grips, and device bumpers.
- Charging Accessories: USB cable boots, power plug gaskets, and strain relief features.
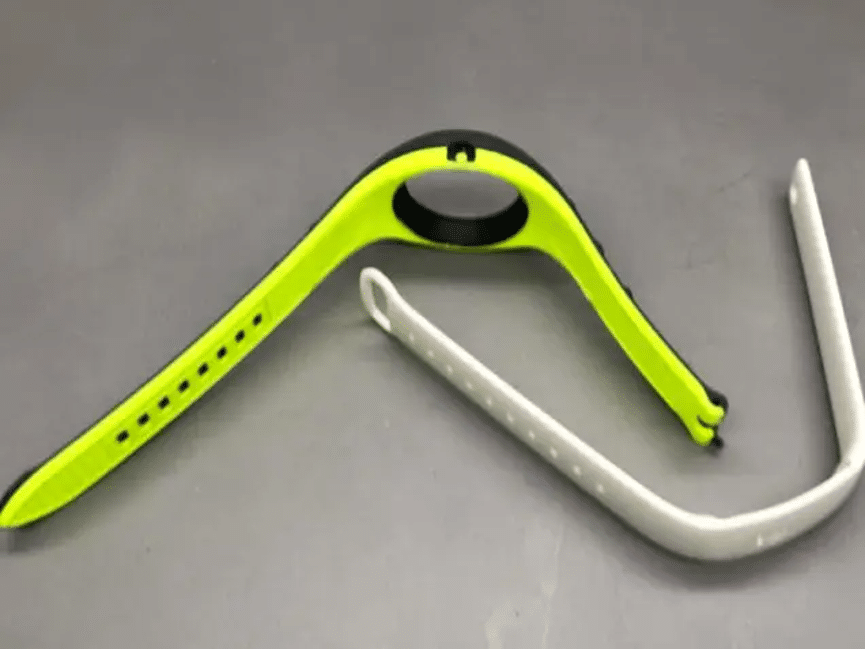
These examples show how the technology of LSR supports sleek, functional, and reliable designs in everyday tech.
Why Choosing Herny Precision’s Service?
For brands looking to bring high-performance 3C products to market, choosing the right manufacturing partner is just as critical as selecting the right material. At Herny Precision, they specialize in precision-engineered LSR injection molding, combining advanced technology with industry-proven expertise to help you achieve consistent quality, scalability, and speed.
High-Precision, Automated LSR Production: Herny Precision operates fully automated LSR injection molding systems equipped with vacuum degassing to minimize air bubbles and ensure consistent part integrity. This results in clean, dimensionally accurate components—ideal for high-performance 3C applications.
Comprehensive Quality Assurance: Every part has undergone strict optical measurement, tensile, and hardness testing in accordance with ISO 9001 and ISO 13485 certified processes, meeting tight industry tolerances and functional specifications.
Smart Engineering Support: The team at Herny Precision provides Design for Manufacturability (DFM) analysis and mold flow simulation to help optimize your part design before tooling begins. This reduces risk, shortens lead time, and improves long-term production stability.
Scalable Mass Production: For large-volume projects, Herny Precision offers on-demand mold solutions that support rapid part qualification and efficient ramp-up. With tools like scientific molding, GD&T-based CMM inspection, and secondary operations (like trimming, bonding, or post-curing), Herny Precision ensures reliable, end-to-end production with minimal downtime.
So, whether you’re developing the next generation of smart wearables or building rugged smartphone accessories, Herny Precision is your trusted partner for delivering quality LSR-molded parts—on time and at scale. For more information, please contact Herny Precision!
Reference
- https://www.silex.co.uk/news/uv-resistance/
- https://www.cntconta.com/en/what-is-tpe
- https://www.3erp.com/blog/flexible-injection-moldings-lsr-vs-tpe/
- https://www.immould.com/tpu-vs-tpe/
- https://omnexus.specialchem.com/selection-guide/thermoplastic-elastomer