CNC machining involves computer-directed machines utilizing preset software instructions to guide tools in forming raw stock into designed geometries. Cutting tools precisely shaped by automated machinery can craft three-dimensional designs from metal, composite, etc., according to programmed specifications. Obtaining an optimized CNC prototype surface quality is important because of its performance benefits, aesthetics, and more.
Measuring the Surface Roughness of a Machined Part
To gauge how machining parameters and sequences influence surface quality, part roughness must be accurately quantified. Surface roughness testers facilitate this evaluation via a tracing stylus characterizing peaks and troughs across workpiece topographies. From these scans, average roughness (Ra) and other specifications describing micro-surface texture are calculated. Professionals rely on such instrumentation to appraise relationships between manufacturing methods and resultant surface finish levels objectively.
Another common way is to use a contact-type surface roughness tester with a diamond-tip tracer that travels over the surface and transmits roughness data to a computer for processing. The computer then displays, stores, and analyzes the roughness parameter values.
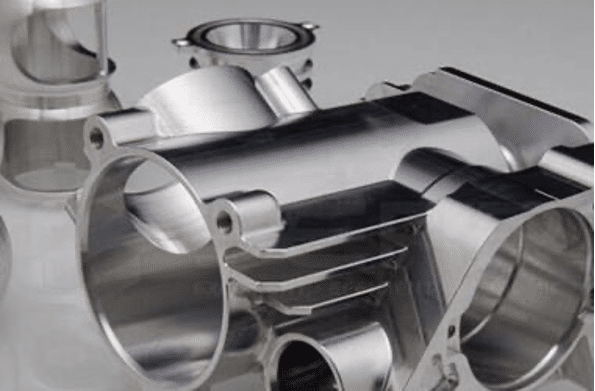
7 Methods for Improving CNC Prototype Surface Smoothness
There are several effective methods for achieving a smoother surface finish on a CNC prototype:
1. Increase the SFM (Surface Feet Per Minute)
Increasing the cutting speed of the tool results in smaller burrs and a glossier finish. The optimal SFM depends on work material, tool material, and geometry. Going too far beyond the optimal SFM can damage tools through excessive friction and heat. Most materials can be machined at higher SFMs for improved surface finish.
2. Reduce the Feed Rate
A slower traverse speed of the tool produces less friction between the tool and workpiece surfaces. This results in less vibration and lower cutting forces, leaving a smoother CNC prototype surface. Generally, lower feed rates are good for enhancing surface finish. However, reducing feed too much can compromise part accuracy and dimensional tolerance.
3. Increase the Top Rake Angle
Tool geometry has a strong impact on surface quality. A more positive rake angle reduces the cutting-edge pressure on the workpiece material. This lowers friction between the tool and workpiece surfaces, allowing for a finer finish. However, very high positive rake angles can weaken the cutting edge.
4. Use a Chip Breaker and Clean the Chip
Chip breakers help control chip evacuation from the prototype machining area for an improved surface finish. They break long, continuous chips into shorter chips to prevent recutting of the newly machined surface. Cleaning chips and debris also prevents such recutting that degrades the quality of the finish.
5. Use a Large Nose Radius
Sharp corners on cutting tools induce a large amount of stress on the workpiece material. A filet or convex nose radius on the tool avoids these stress concentration effects. It results in less workpiece material being forcibly displaced, leaving a smoother CNC prototype surface with reduced chances of cracks or burrs.
6. Use a Wiper with an Insert
A specially designed wiper tool attachment with additional machining edges can be used after roughing processes to remove burrs and leave a superior surface finish. Such wipers follow the same tool path as the roughing tool in a finishing operation.
7. Check the Tool-Holding and Work-Holding
Any vibrations transferred from improper or loose clamping of tools or workpieces degrade the quality of the CNC prototype surface finish. Rigid holding of both the tools and parts is important to maintain dimensional accuracy and surface smoothness.
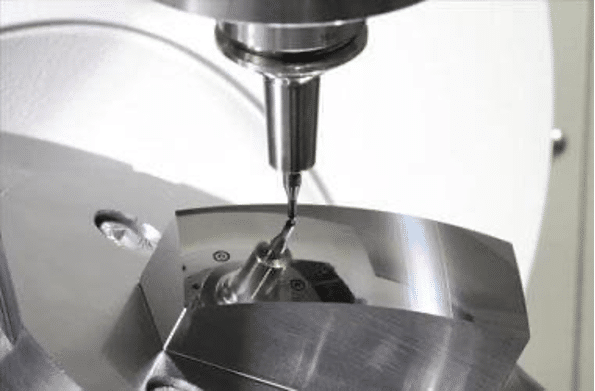
HPrapid: A Professional Machined Part Supplier
HPrapid is a seasoned CNC machining service provider. The company is committed to delivering top-quality rapid prototyping and low-volume manufacturing with high-precision axis CNC milling and turning machines. The manufacturer has a professional team that can achieve the tight tolerances specified. Furthermore, it also has a material testing facility and CMM machine for quality verification and measurement.
HPrapid offers CNC milling and turning of plastics, metals, and various other materials to exact specifications. Some key advantages include:
- Precision machining within tight tolerances
- Capable of complex geometries, internal features, and threads
- High-speed machining of plastics and metals
- Can machine-hardened materials like stainless steel
- Fast turnaround times and quick design iterations
Conclusion
Overall, the seven methods highlighted above are effective in improving the surface smoothness of a CNC prototype. A professional CNC machining supplier like HPrapid with the latest equipment and technical expertise can ensure prototypes are manufactured within specifications for testing and validation. The manufacturer’s fast, affordable, and reliable services fulfill rapid prototyping needs. Contact HPrapid for the production of custom, high-quality CNC machined parts.