Mulcher blades are crucial components in the operation of mulching machines, and they are responsible for cutting and shredding vegetation into smaller pieces. Whether used in agriculture, landscaping, or forestry, the efficiency and durability of mulcher blades directly impact the performance and longevity of the equipment. Therefore, it is imperative to ensure that you are dealing with a supplier that will meet the quality you need in these blades.
Visit Carbide Mulcher Teeth, one of the reputable and reliable manufacturers of mulching blades and many other mulcher parts. They have an impressive catalog with affordable and quality mulcher parts, which is the reason for their strong foothold in the market.
So, what are the key factors you need to consider when it comes to mulcher blades? In this guide, we will delve into the materials used in mulcher blade manufacturing, quality control measures, and essential maintenance practices to ensure optimal functionality. Read more:
Materials Used in Mulcher Blades:
Mulcher blades are essential components of mulching machines, tasked with the demanding job of cutting and shredding vegetation. The choice of materials for mulcher blade construction is paramount to ensure durability, cutting efficiency, and resistance to wear. Several materials are commonly employed in the manufacturing of mulcher blades:
Hardened Steel
Blades crafted from hardened steel alloys, such as high-carbon steel or alloy steel, are renowned for their exceptional strength and durability. This usually forms the body of the blades. The choice of steel alloys is majorly determined by the condition in which they will be used. For mulching weeds and other soft foliage, the steely alloy may be different from the blades for mulching brushes and tree limbs.
Therefore, it is important to check the quality or the hardness of the steel material when buying. In some cases, the choice of the steel materials might be different. Therefore, there is a need to be extra careful to avoid selecting the wrong material. Note that the body (steel) is the part that takes the heat generated by the blades when mulching. So, the size or surface area matters.
Carbide Tipped Blades
Carbide-tipped mulcher blades feature inserts made of tungsten carbide along the cutting edge. Tungsten carbide is renowned for its hardness and resistance to abrasion, enhancing the cutting performance and longevity of the blades. Therefore, it can maintain its hardness for a longer time than steel and other metals. Carbide-tipped blades excel in applications where the terrain is rocky or abrasive, ensuring consistent cutting efficiency.
Boron Steel
Mulcher blades constructed from boron steel exhibit outstanding strength, hardness, and toughness. Boron steel blades are highly resistant to bending, fracturing, and wear, making them ideal for heavy-duty mulching tasks. These blades maintain their cutting ability even when subjected to demanding conditions, contributing to efficient vegetation processing.
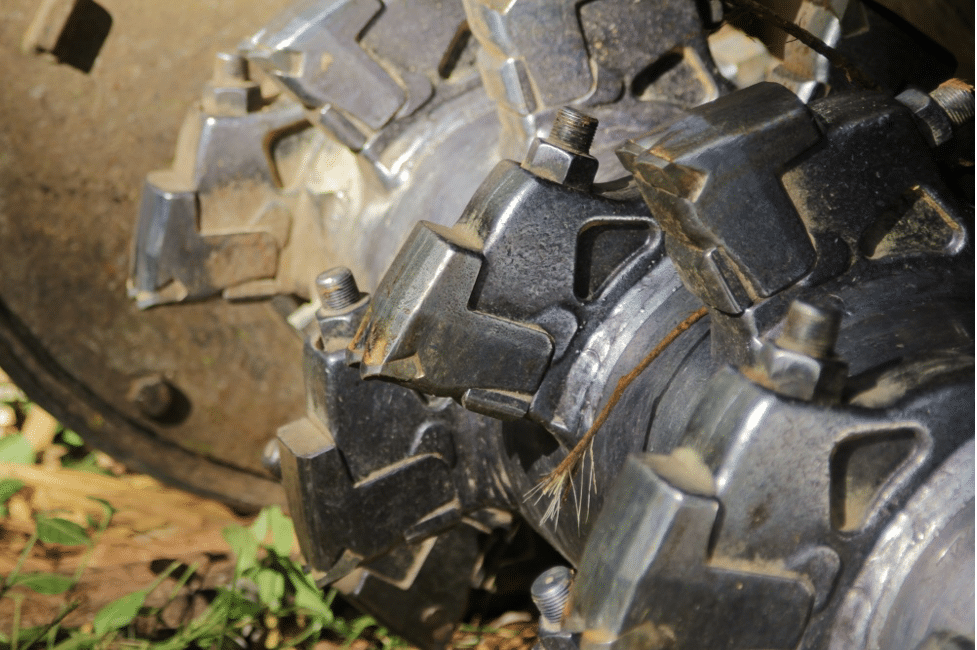
Quality Control Measures:
Ensuring consistent quality in mulcher blade manufacturing is essential to guarantee performance, reliability, and user satisfaction. Manufacturers implement stringent quality control measures throughout the production process to maintain high standards of blade quality. These measures encompass various aspects, including material selection, precision machining, heat treatment, and inspection procedures:
Material Selection
The first step in ensuring blade quality is selecting high-quality raw materials with the required mechanical properties and chemical composition. Manufacturers source materials from reputable suppliers and conduct thorough testing to verify material integrity and suitability for mulcher blade applications.
Precision Machining
Advanced machining techniques help to achieve precise blade dimensions and profiles. Computer-controlled machining processes ensure uniformity and consistency in blade geometry, optimizing cutting performance and reducing the risk of blade defects.
Heat Treatment
Heat treatment processes, such as quenching and tempering, are applied to enhance the hardness, toughness, and wear resistance of mulcher blades. Controlled heat treatment cycles ensure uniform material properties throughout the blade, improving its ability to withstand the rigors of mulching operations.
Inspection and Testing
Rigorous inspection procedures are conducted at various stages of the manufacturing process to identify any defects or inconsistencies in the blades. Dimensional checks, hardness testing, visual inspections, and other quality control measures help ensure that only blades meeting specified standards are released for use.
Maintenance Practices:
Proper maintenance is essential to maximize the lifespan, efficiency, and performance of mulcher blades. Implementing a proactive maintenance routine can help prevent premature wear, ensure optimal cutting performance, and minimize downtime. Here are five key maintenance practices for mulcher blades:
Regular Inspections
Conduct regular visual inspections of mulcher blades to identify signs of wear, damage, or dullness. Inspect the cutting edges for chips, cracks, or excessive wear, and check for any abnormalities in blade alignment or mounting. Therefore, promptly replace worn or damaged blades to maintain cutting efficiency and prevent unnecessary strain on the equipment.
Sharpening
Keep mulcher blades sharp to ensure clean and efficient cutting. Dull blades can result in poor mulching performance, increased fuel consumption, and additional stress on the mulching equipment. Use appropriate sharpening tools, such as grinding wheels or sharpening stones, to maintain the sharpness of the blade edges. Follow manufacturer guidelines for the correct sharpening angle and technique to achieve optimal results.
Balancing
Imbalanced blades can cause vibrations and premature wear on the mulcher and its components. Periodically check the balance of mulcher blades using a balancing machine and make adjustments as necessary to ensure smooth operation. Balanced blades contribute to reduced vibration, improved cutting performance, and extended equipment lifespan.
Lubrication
Apply lubrication to the blade mounting bolts or nuts to prevent corrosion and facilitate easy removal during maintenance activities. Lubricating the mounting hardware helps prevent rust and corrosion, ensuring that blades can be quickly and safely replaced when necessary. Use a suitable lubricant recommended by the equipment manufacturer to maintain optimal performance and reliability.
Cleaning
Regularly clean mulcher blades and the surrounding components to remove debris, dirt, and vegetation buildup. Accumulated debris can hinder cutting performance, increase wear on the blades, and lead to overheating of the equipment. So, use compressed air, wire brushes, or pressure washers to remove stubborn debris and maintain optimal operating conditions.
Conclusion:
Mulcher blades play a vital role in the efficient operation of mulching equipment across various industries. By understanding the materials used in blade construction, implementing stringent quality control measures, and adhering to proper maintenance practices, users can maximize the performance and longevity of their mulcher blades. With regular inspection, sharpening, and maintenance, mulcher blades can continue to deliver superior cutting performance, contributing to productive and cost-effective mulching operations.