Steel alloys and aluminum are popular choices for different manufacturing operations, forming, bending, machining, deep-drawing, etc. Aluminum has a higher strength-to-weight ratio, whereas steels are known for high strength. However, the issue of corrosion influences the steel part’s performance in humid and harsh environments. So, steels are coated with zinc to protect against rust formation, called galvanized steel. There are many distinctions between galvanized steel vs aluminum, including properties, uses, cost, machinability, etc.
Let’s discuss the comparative advantages, disadvantages, and key differences in properties.
What is Galvanized Steel?
First, a galvanized metal refers to a metal coated by a thin protective layer of zinc material. The thickness of this galvanized coating can range from 5 to 110 µm. It is typically applied to ferrous metals and alloys, like iron and carbon alloys. A galvanized steel is carbon steel coated with this protective zinc layer to save it from corrosion, wear, and stains. Here, the superior corrosion protection properties of zinc increase the performance & lifespan of the underlying steel.
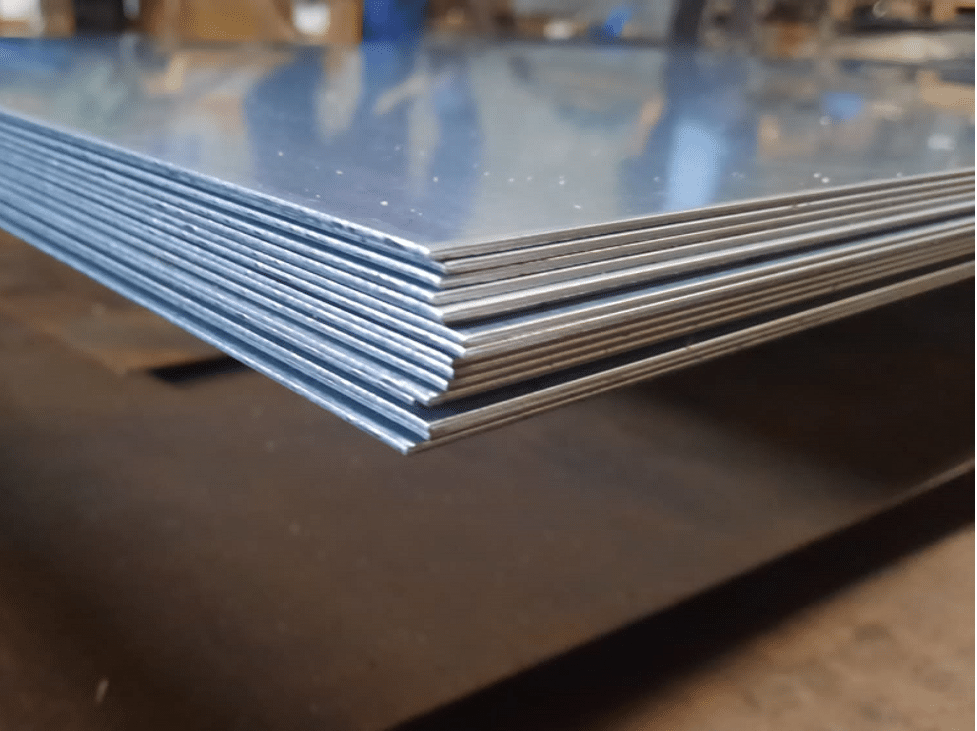
The protection of the zinc layer and the high strength of steel combined make it popular in screws, outdoor items, automotive panels, and agricultural machinery parts.
Advantages of Galvanized Steel
- Mechanical Strength: Galvanized steel offers high mechanical strength and is also heavier than aluminum metal.
- Corrosion Resistance: The protective zinc layer over carbon steel protects the steel from rust formation as it acts as a barrier layer between the substrate and the external environment.
- Cost-effectiveness: Although being a high-strength and durable material, the cost of galvanized steel is lower, if we especially compare galvanized steel vs aluminum.
Disadvantages of Galvanized Steel
- Aggressive and harsh chemical conditions weaken the integrity of the zinc layer on galvanized steel, compromising the corrosion resistance.
- If you are using it as a finishing option for steel sheets, it can be expensive compared to painting, powder coating, and other methods.
What is Aluminum?
Aluminum is a lightweight metal that provides considerable good mechanical strength, although not as high as galvanized steel sheets. It is also ductile and has high formability. Additionally, aluminum grades also exhibit good thermal and electrical conductivity.
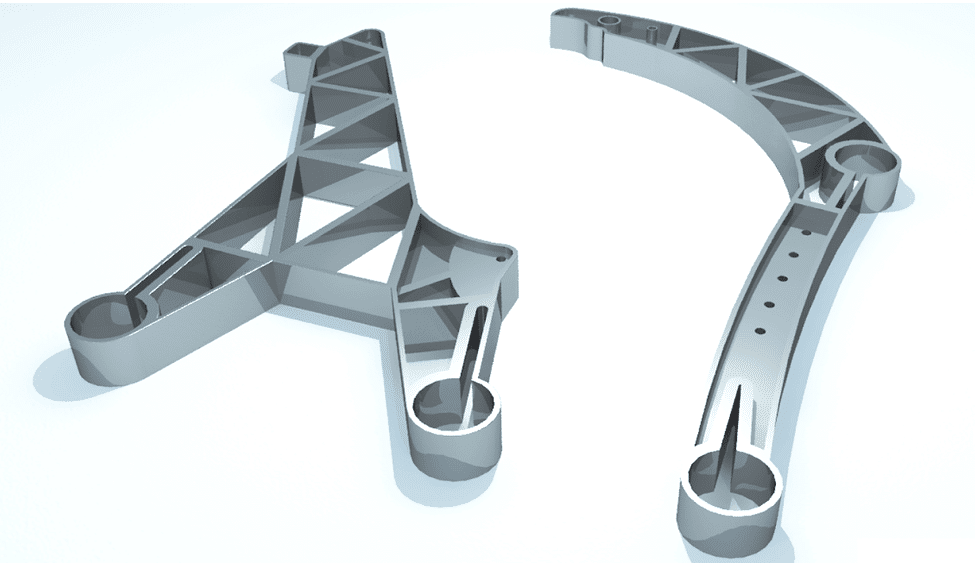
Several industrial grades of aluminum are used in machining & metal fabrication processes, such as 6065, 7071, 6061, 7075, etc. In these grades secondary elements like iron, manganese, magnesium, and silicone are added into aluminum for enhanced properties.
Advantages of Aluminum
- Low Weight: Although being a light engineering material, aluminum has a lower weight than other materials like steel, iron, zinc, etc.
- Corrosion Protection: After air exposure, the aluminum surface forms a proactive oxide layer that protects from corrosion.
- Conductivity: Aluminum and its alloys are conductive to heat and electricity.
- Machinability & Formability: Aluminum has excellent machinability and formability that allows to shape of raw aluminum into functional items accurately.
Disadvantages of Aluminum
- In comparison of galvanized steel vs aluminum, it is relatively more costlier than steel.
- Low melting points make aluminum unstable in high-temperature applications.
Key Differences between Galvanized Steel and Aluminum
After the comparative pros & cons of galvanized steel vs aluminum, let’s compare them head-to-head on various aspects, strength, conductivity, uses, etc.
Criteria | Galvanized Steel | Aluminum |
Composition | Steel coated with zinc for corrosion protection | Pure aluminum or aluminum alloys |
Weight | Heavier | Lightweight |
Strength | High mechanical strength; heavier than aluminum | Lower strength compared to galvanized steel; lightweight |
Corrosion Resistance | Protected by a zinc layer, effective in moderate environments | Forms a natural oxide layer that protects it from corrosion |
Conductivity | Limited conductivity | High thermal and electrical conductivity |
Cost | More cost-effective | Generally more expensive |
Applications | Outdoor, automotive, and agricultural machinery parts | Machining, metal fabrication, electrical applications |
Limitations | Susceptible to harsh chemicals; zinc layer may degrade | Low melting point; not ideal for high temperatures |
Subsequently, let’s compare the physical-mechanical properties with their approximate numerical values. Analyzing their numerical values helps to make better choices between them.
Property | Galvanized Steel | Aluminum |
Density (kg/cm³) | 7850 | 2700 |
Electrical Resistance (Ωmm²/m) × 10² | 0.093 | 2.66 |
Thermal Conductivity (W/(m·K)) | 60 | 235 |
Thermal Expansion Coefficient (mm/mm°C × 10⁻⁶) | 12 | 24 |
Melting Temperature (°C) | 1370 | 660 |
Ultimate Tensile Strength (MPa) | 400 | 91.5 |
Yield Strength (MPa) | 300 | 35 |
Young’s Modulus (GPa) | 210 | 69 |
Poisson’s Ratio | 0.3 | 0.33 |
Elongation (by %) | 22 | 30.1 |
Hardness (HV) | 200-250 | 57.98 |
Can I Galvanized Aluminum?
The main purpose of galvanized metal is to protect the surface metal & alloys that are prone to corrosion and wear, typically for the ferrous material. Here, aluminum is already resistant to surface corrosion as it forms an aluminum oxide layer(Al2O3) on the surface naturally whenever it comes into contact with the environment. So, aluminum does not need galvanization in general. However, if you need galvanized aluminum for specific applications, use the hot-dip method under controlled dipping & curing parameters.