Factory audits play a crucial role in verifying compliance, ensuring product quality, and upholding ethical manufacturing practices. These audits provide businesses with a structured approach to assessing their suppliers and identifying potential risks in production. Industries such as automotive, electronics, textiles, pharmaceuticals, and food processing rely heavily on factory audits to maintain stringent quality control and regulatory compliance.
Key Benefits of Factory Audits
- Regulatory compliance – Ensuring adherence to national and international laws
- Quality assurance – Preventing defects and maintaining product consistency
- Ethical labor practices – Promoting fair wages and safe working conditions
- Supply chain security – Reducing risks of fraud, counterfeiting, and disruptions
- Environmental responsibility – Monitoring sustainability efforts and reducing waste
What is a Factory Audit?
A factory audit is a structured assessment of a manufacturing facility to evaluate compliance with quality, safety, environmental, and ethical standards. Companies conduct factory audits to ensure their suppliers meet contractual obligations, legal requirements, and industry best practices.
Factory audits play an essential role in supply chain management, offering a transparent view of production conditions and supplier reliability. By identifying risks early, businesses can mitigate production delays, avoid reputational damage, and improve operational efficiency. For a comprehensive and professional assessment, businesses can benefit from a QCADVISOR factory audit, which ensures that suppliers adhere to the highest industry standards.
Why Are Factory Audits Important?
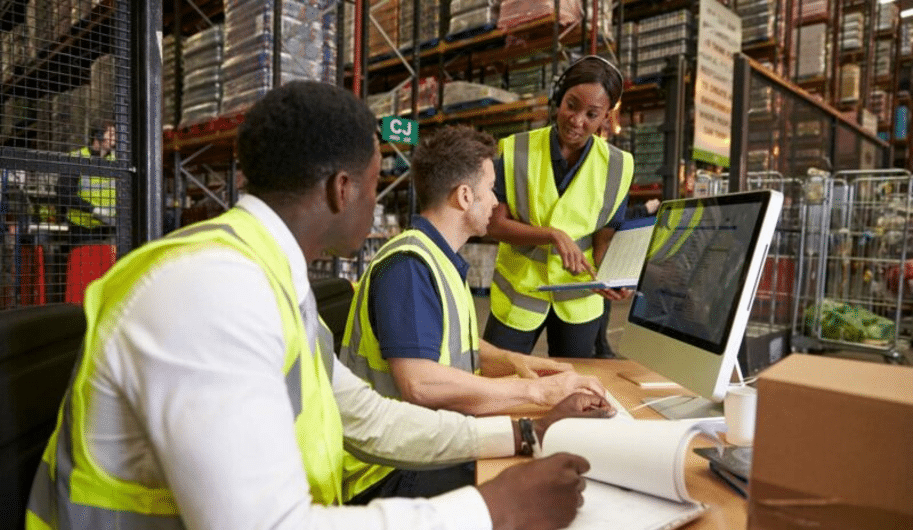
Factory audits are critical for businesses that rely on outsourced manufacturing. These assessments ensure that suppliers comply with regulations, maintain quality control, and uphold ethical labor practices. Below are the primary reasons why companies invest in factory audits:
- Regulatory Compliance – Meeting international standards (ISO, OSHA, FDA, etc.)
- Product Quality Assurance – Reducing defects and maintaining consistency
- Ethical Labor Practices – Ensuring fair wages, worker safety, and human rights
- Supply Chain Risk Management – Identifying vulnerabilities before they escalate
Main Risks of Not Performing Factory Audits
- Legal penalties for non-compliance with regulations
- Product recalls and safety hazards due to quality failures
- Reputational damage from unethical labor practices
- Supply chain disruptions due to unreliable suppliers
- Financial losses from fraud, defects, or production delays
What Are the Different Types of Factory Audits?
Factory audits vary depending on the objectives and areas of assessment. Below are the key types of factory audits:
Quality System Audits
Quality system audits ensure that manufacturers adhere to industry quality management standards such as:
- ISO 9001 – International standard for quality management systems
- Six Sigma – Process improvement methodology reducing defects
- Good Manufacturing Practices (GMP) – Guidelines for food, pharma, and medical device production
Social Compliance Audits
Social compliance audits focus on working conditions, employee rights, and ethical labor practices. Common frameworks include:
- SA8000 – Social accountability standard ensuring fair labor conditions
- BSCI (Business Social Compliance Initiative) – Ethical labor assessment framework
- SEDEX (Supplier Ethical Data Exchange) – Global supply chain ethical standards
Environmental Audits
These audits assess a factory’s sustainability practices and environmental impact. Common standards include:
- ISO 14001 – Environmental Management certification
- LEED (Leadership in Energy and Environmental Design) – Sustainable building practices
Security Audits
Security audits evaluate supply chain security and risk mitigation strategies. Standards include:
- C-TPAT (Customs-Trade Partnership Against Terrorism) – Securing international supply chains
- TAPA (Transported Asset Protection Association) – Reducing theft and counterfeiting risks
Ethical Audits
Ethical audits assess corporate responsibility and worker welfare. These audits check for:
- Child labor and forced labor policies
- Fair wages and safe working conditions
- Freedom of association and anti-discrimination policies
How Do Factory Audits Work?

Factory audits follow a systematic process to evaluate a supplier’s compliance and operational efficiency.
Pre-Audit Preparations
Before conducting an audit, businesses must:
- Select an accredited audit firm or internal auditing team
- Review compliance requirements and industry standards
- Gather necessary documentation and supplier records
On-Site Inspection Process
During the audit, inspectors assess:
- Production facilities and machinery conditions
- Quality control procedures and documentation
- Health, safety, and environmental compliance
Interviewing Workers and Management
Interviews provide insights into:
- Wages, working hours, and overtime policies
- Workplace conditions and employee grievances
- Adherence to ethical and social compliance standards
Sampling and Product Testing
Auditors select product samples for testing, ensuring:
- Material quality and durability
- Compliance with safety and regulatory requirements
Reporting and Compliance Evaluation
After the audit, businesses receive a detailed report highlighting:
- Non-compliance areas and corrective actions
- Audit scoring and overall supplier assessment
What Are the Key Criteria in a Factory Audit?
Factory audits focus on the following criteria:
- Product quality standards and testing procedures
- Facility safety and emergency preparedness
- Environmental impact and waste management
- Labor conditions, wages, and ethical policies
What Are the Most Common Factory Audit Failures?
Factories often fail audits due to:
- Poor working conditions and safety violations
- Non-compliance with labor laws and wage requirements
- High defect rates and inconsistent product quality
- Environmental regulation breaches
How to Prepare for a Factory Audit?
Businesses can improve their audit readiness by following these steps:
Internal Pre-Audit Checklist
- Conduct self-assessments before official audits
- Identify and rectify compliance gaps
Employee Training and Awareness
- Educate employees on regulatory compliance
- Conduct mock audits to ensure preparedness
Organizing Documentation
- Maintain accurate records of quality control and labor policies
- Ensure accessibility of past audit reports and corrective actions
What Happens After a Factory Audit?
Following an audit, businesses should:
- Implement corrective action plans for non-compliance issues
- Schedule re-audits to verify improvements
- Develop supplier improvement programs to enhance performance
How to Choose the Right Factory Audit Service?
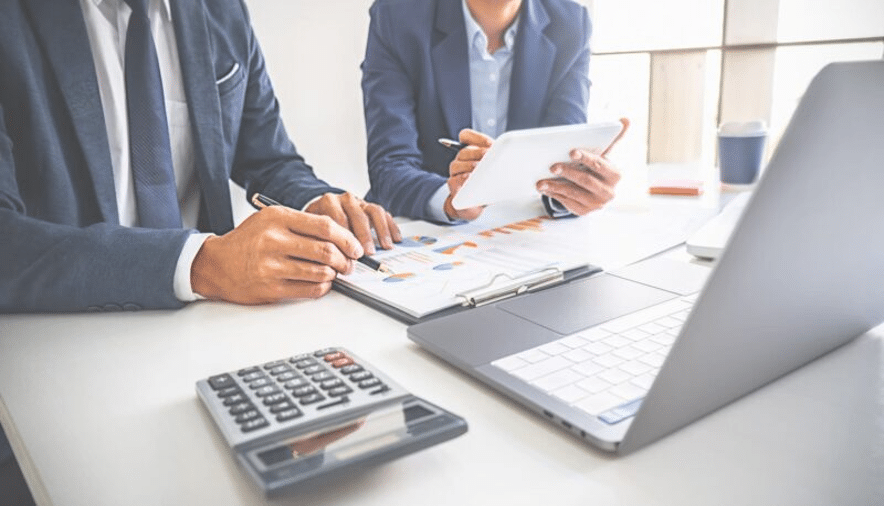
Consider these factors when selecting an audit provider:
- Accreditation and industry expertise
- Audit methodology and reporting structure
- Global reach and supplier network coverage
What Are the Costs of a Factory Audit?
Audit costs depend on factors such as location, audit type, and complexity.
Factors Influencing Factory Audit Costs
- Factory location and size
- Number of auditors required
- Type and depth of assessment
What Are the Alternatives to Traditional Factory Audits?
Companies can explore other compliance monitoring methods:
- Remote auditing via digital tools
- Supplier self-assessment programs
- Blockchain-based supply chain tracking
Conclusion
Factory audits play a pivotal role in ensuring compliance, product quality, and ethical manufacturing. By conducting regular audits, businesses can minimize risks, build stronger supplier relationships, and enhance their brand reputation. Investing in proper audit procedures today ensures a more sustainable and responsible supply chain for the future.