What guarantees that oil and gas pipelines can withstand extreme pressure, harsh environments, and years of continuous operation? The answer lies in material testing, which verifies pipeline materials’ mechanical properties before use.
Among the different testing methods, tensile testing is one of the most crucial for evaluating a pipeline’s strength, ductility, and resistance to mechanical stress. It determines whether a material can withstand operational forces without deforming or breaking.
According to PHMSA, over 5,500 pipeline failures have occurred in the last two decades, often due to material weaknesses. Tensile testing helps prevent such failures by identifying potential defects early, making sure that only high-quality, reliable materials are used in pipeline construction.
Without tensile testing, pipelines would be far more vulnerable to fractures, leaks, and costly structural failures. This testing method is key in making pipelines stronger, safer, and more durable for long-term use.
The Role of Tensile Testing in Pipeline Strength and Durability
Oil and gas pipelines experience constant mechanical stress, pressure fluctuations, and exposure to corrosive environments. A single material defect or failure in structural integrity can result in hazardous leaks, economic losses, and safety risks. Tensile testing assists in preventing such failures by evaluating how materials respond to stress and verifying that they meet the stringent requirements of the industry.
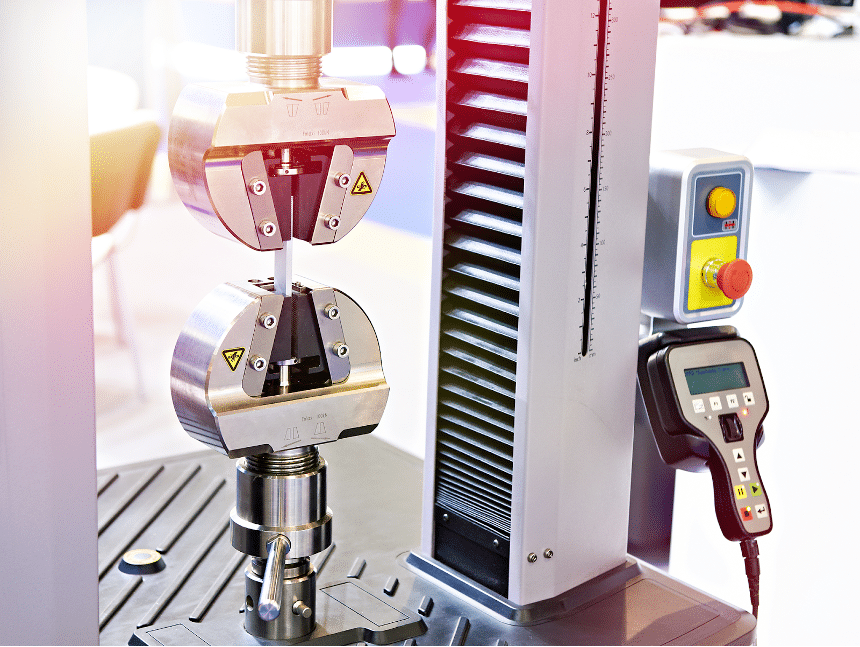
Measuring Key Mechanical Properties
Tensile testing is a controlled mechanical test involving stretching material until it fractures. The data obtained allows engineers to assess:
Yield Strength – The point at which the material deforms permanently.
Tensile Strength – The maximum stress a material can endure before breaking.
Elongation – The material’s ability to stretch without fracturing, which impacts flexibility and toughness.
Fracture Behavior – How the material fails under stress, revealing potential structural weaknesses.
Each of these properties determines whether a pipeline material is suitable for high-pressure applications. A material with low yield strength may deform under operational stress, while low tensile strength increases the risk of rupture. Poor elongation properties make a material brittle and prone to cracking, especially in cold or high-strain environments.
Adapting to Harsh Operating Conditions
Pipelines are often deployed in extreme environments, from deep-sea installations to freezing Arctic conditions. Materials must be able to endure:
Thermal expansion and contraction caused by temperature variations.
Seismic activity and ground movements in earthquake-prone regions.
Corrosive exposure to soil chemicals, moisture, and transport substances.
Tensile testing replicates these real-world conditions, allowing engineers to select materials that can withstand long-term operational stress without premature failure.
One significant challenge in pipeline engineering is hydrogen embrittlement—a process where hydrogen atoms infiltrate metal, causing it to become brittle and crack over time. Tensile testing in high-pressure hydrogen environments is fundamental for assessing whether pipeline steels can handle hydrogen transportation, a key consideration as the industry shifts toward hydrogen fuel infrastructure.
The Impact of Tensile Testing on Pipeline Safety and Longevity
Oil and gas pipelines are built to operate under enormous stress for decades, yet mechanical failure remains a major concern. While external factors like corrosion and ground movements contribute to pipeline degradation, the inherent strength and flexibility of the material itself play the most crucial role in determining long-term performance. This is where tensile testing provides vital data, helping engineers make certain that pipelines can endure not just immediate pressures, but also prolonged exposure to strain, fatigue, and operational wear.
Preventing Fatigue-Related Failures
Pipelines do not fail because of a single, overwhelming force—they degrade over time through a process called material fatigue. Constant pressure changes, temperature shifts, and vibrations from nearby infrastructure all contribute to the gradual weakening of the pipeline’s internal structure.
Tensile testing allows engineers to measure how a material responds to repeated stress cycles and determine its fatigue resistance. This is particularly important in high-pressure pipelines where stress variations occur frequently. A material with poor fatigue resistance might initially pass strength tests but degrade rapidly over time, leading to unexpected fractures or leaks.
Beyond fatigue, tensile testing also reveals the material’s resistance to stress corrosion cracking (SCC)—a failure mode where microscopic cracks form due to a combination of tensile stress and corrosive environments. Pipelines running through areas with high moisture content, acidic soil, or exposure to hydrogen-rich substances are particularly vulnerable. By understanding a material’s fracture mechanics, engineers can select the best alloys, coatings, or manufacturing processes to maximize resistance to these threats.
Improving Safety in Welded Joints
Pipeline welded sections are often its weakest points. Even if the base material is strong, improper welding can lead to weak bonds, uneven stress distribution, and premature failure. Tensile testing is used extensively to assess weld mechanical integrity, verifying that they are as strong—or even stronger—than the surrounding material.
Specialized tensile tests for welded joints focus on joint efficiency, ductility loss, and failure modes. By refining welding techniques based on tensile test results, manufacturers can reduce defect rates, maximize pipeline resilience, and guarantee safe long-term operation.
Tensile Testing Standards and Compliance in the Oil & Gas Industry
The oil and gas sector operates under some of the most stringent safety and quality regulations in the world. Pipelines must meet specific tensile strength, ductility, and fracture resistance requirements before they can be approved for use. Tensile testing serves as the primary method for confirming compliance with industry regulations, assuring uniformity and reliability in every pipeline segment.
Key International Standards for Pipeline Tensile Testing
Several internationally recognized standards define the procedures and requirements for tensile testing in pipeline manufacturing:
ASTM A370 – Covers mechanical steel products testing, including tensile strength and elongation.
ISO 6892-1 – Specifies testing methods for metallic materials at room temperature.
API 5L and ISO 3183 – Set requirements for pipeline materials used in oil and gas transportation.
The Role of Compliance in Material Selection
Compliance with global testing standards means pipeline manufacturers maintain consistent quality and safety levels within different projects and regions. These standards dictate the minimum strength and flexibility requirements a material must meet, thus reducing the risk of subpar materials entering production.
Beyond material selection, tensile testing standards also affect pipeline design, installation methods, and maintenance cycles. Engineers rely on tensile test data to:
Determine the optimal wall thickness for durability and cost.
Establish safe operating pressure limits based on material strength.
Identify maintenance schedules based on expected wear and tear rates.
Additionally, the industry is seeing a shift toward hydrogen-ready pipelines, which require increased mechanical properties to withstand embrittlement and pressure fluctuations. Due to this, tensile testing protocols are constantly being updated, enabling pipeline manufacturers to meet emerging energy demands while maintaining the highest levels of safety.
Equipment Used for Tensile Testing in Pipeline Development
Tensile testing requires not only strict procedures but also high-quality equipment. As we have already stated, pipelines are subjected to extreme pressure and environmental stress, which makes it necessary to conduct precise material assessments. Without advanced equipment, test results may be unreliable, leading to failures.
As the first step in a testing process, it is imperative to prepare test specimens accurately to obtain valid results. CNC machines for tensile specimen preparation make certain that samples meet ASTM and ISO standards, thereby preventing human error. This accuracy is especially important for high-strength steels and materials used in hydrogen pipelines, as even small deviations can lead to incorrect strength calculations.
Once prepared, specimens are tested using Universal Testing Machines (UTMs), which apply controlled force to measure yield strength, ultimate tensile strength, and elongation. Modern UTMs use digital controls and automated force application, minimizing variability and ensuring consistent results. Using these machines is a necessary step in assessing pipeline materials’ durability over long periods.
When manufacturers rely on high-quality CNC machines for specimen preparation and advanced UTMs for testing, they obtain comprehensive data that directly impacts pipeline durability and safety. Choosing equipment from trusted international suppliers, such as TensileMill CNC, known for its advanced solutions for both tensile sample preparation and testing, gives engineers confidence that every test delivers reliable insights. With precision at every stage, pipelines are built to withstand extreme conditions and operate safely for decades.
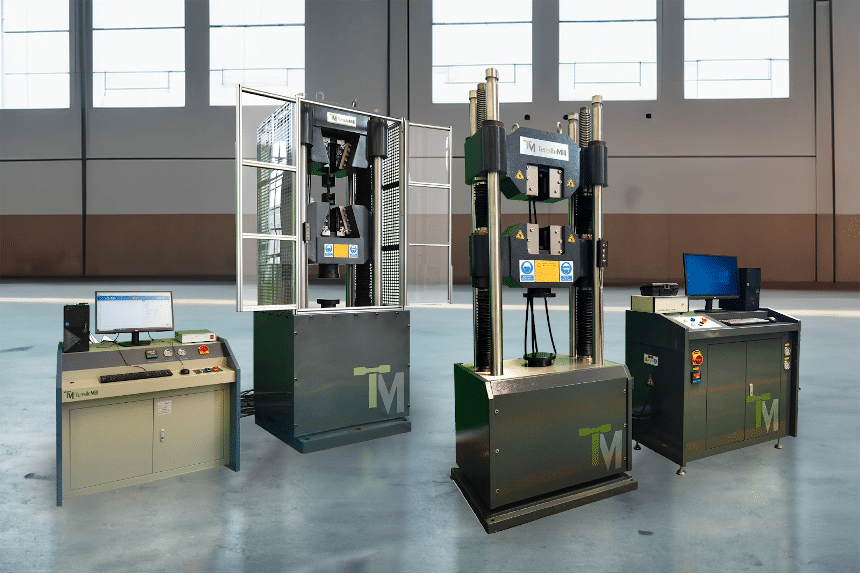
Tensile Testing: The Key to Stronger Oil & Gas Pipelines
Looking at the key points discussed, it’s clear that tensile testing is a vital component for verifying the strength, durability, and long-term safety of oil and gas pipelines. This testing method helps engineers assess critical mechanical properties, identify weaknesses before they become failures, and confirm that materials meet industry standards. Without it, pipelines would be far more vulnerable to fractures, leaks, and structural degradation over time.
Reliable results depend not only on strict testing procedures but also on high-precision equipment for specimen preparation and force application. With accurate data, manufacturers can make informed decisions about material selection, welding integrity, and structural design, ultimately creating pipelines that can withstand extreme pressures and environmental challenges.
With the growing need for energy and the emergence of new challenges, the need for in-depth material testing will only grow. By continually improving testing methods and equipment, the industry guarantees that pipelines remain safe, efficient, and built to last for decades.