In today’s interconnected world, the intricate web of global supply chains faces a myriad of challenges—from fluctuating market dynamics to unforeseen disruptions in production. Factories span continents, and even a single lapse in quality control can trigger cascading effects that ripple throughout industries. Amid these uncertainties, a robust system of factory audits emerges as a critical linchpin, ensuring that every link in the supply chain upholds the standards necessary for reliability, safety, and quality. This article delves deep into the realm of factory audits, unraveling how they not only safeguard production integrity but also boost efficiency, compliance, and overall supply chain resilience.
Global supply chains have become the lifeblood of modern commerce, intricately connecting manufacturers, suppliers, distributors, and end users across vast distances. In a landscape fraught with challenges such as fluctuating quality standards, regulatory pressures, and the risk of operational inefficiencies, the necessity for rigorous oversight has never been more pronounced. Factory audits, as a systematic approach to evaluating production facilities, serve as a preemptive measure against potential failures that could otherwise disrupt entire markets. Partnering with industry leaders through a QCADVISOR factory audit provides tailored insights and robust safeguards to ensure that every link in your supply chain meets the highest standards of quality and compliance.
The persistent pressures of globalization and rising consumer expectations compel companies to scrutinize every stage of their manufacturing processes. With geopolitical tensions, pandemics, and rapid technological shifts posing constant threats, these audits become an essential tool for risk management. They provide organizations with tangible insights into operational practices and reveal both strengths and vulnerabilities in production. By identifying issues before they evolve into critical problems, audits ensure quality control and bolster confidence among international partners. In essence, the practice of conducting thorough factory evaluations is as indispensable to supply chain management as the logistics that transport goods across the globe.
Moreover, effective audits bridge the gap between compliance and operational excellence, facilitating a proactive rather than reactive management style. As we explore the multifaceted benefits of these inspections, it becomes clear that their role extends far beyond simple quality checks; they are a cornerstone of global supply chain security and continuity.
What are Factory Audits and Why Are They Critical?
Factory audits are systematic, in-depth assessments conducted to verify the operational integrity, production processes, and compliance of manufacturing facilities. Much like the comprehensive explanations found on platforms such as Wikipedia—where a term is precisely defined and contextualized—factory audits are designed to evaluate the adherence of factories to both internal standards and external regulations. They involve detailed reviews of operational workflows, safety protocols, quality control systems, and regulatory compliance measures that collectively form the backbone of modern supply chain operations.
Factory audits are indispensable in today’s global marketplace because they serve as a critical checkpoint against operational risks and inefficiencies. By scrutinizing every facet of a facility’s operations, these audits help organizations detect deviations from industry best practices and potential non-compliance issues before they escalate into larger problems. Their role is not only preventive but also developmental; audits frequently identify opportunities for process improvements and cost savings, ultimately fostering a culture of continuous improvement across supply chains.
Before exploring a bullet list of key benefits, it is important to understand that the power of a factory audit lies in its multifaceted approach. It goes beyond a superficial check, offering a granular view of everything from machinery maintenance to employee working conditions. This holistic evaluation enables companies to optimize operations, mitigate risks, and maintain a competitive edge in increasingly complex markets. The benefits of a rigorous audit process can be summarized as follows:
- Risk mitigation
- Quality assurance
- Regulatory compliance
- Enhanced transparency
These benefits underscore why factory audits are critical components in securing the integrity of global supply chains, ensuring that each facility contributes positively to the overall network.
How Do Factory Audits Secure Global Supply Chains?
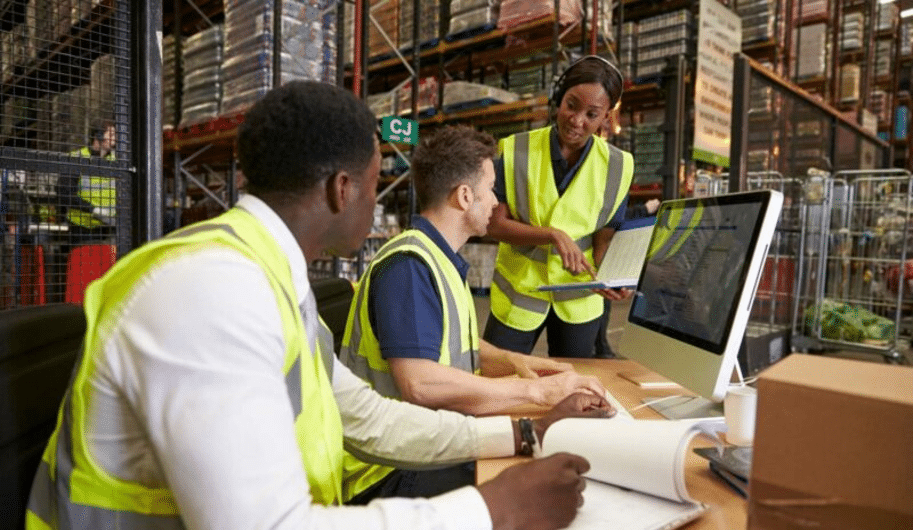
Factory audits secure global supply chains by systematically identifying and addressing potential vulnerabilities within manufacturing processes. They work as an essential checkpoint that ensures factories meet stringent quality standards and regulatory requirements, thereby reducing the risk of substandard products entering the market. Each audit is a deep-dive investigation into operational practices that, when executed correctly, minimizes disruptions and fortifies the trust between suppliers and buyers.
At the heart of this process is a detailed evaluation of both operational efficiency and product quality. Audits verify that manufacturing practices comply with predefined standards and industry regulations, thus preemptively identifying any deviations that might lead to production bottlenecks or compliance issues. Furthermore, these evaluations not only expose areas of weakness but also highlight opportunities for operational improvements, fostering a proactive approach toward risk management.
Before considering the specific mechanisms, it is crucial to note that the integrity of the supply chain depends on a continuous cycle of assessment, improvement, and re-assessment. The systematic nature of audits ensures that potential risks are addressed before they escalate. The main ways in which audits secure supply chains include:
- Ensuring product quality
- Verifying compliance with international standards
- Mitigating operational risks
This approach not only safeguards individual facilities but also reinforces the reliability and resilience of the entire supply chain, making factory audits a fundamental element in global operational strategy.
What Are the Different Types of Factory Audits?
Factory audits are not a one-size-fits-all process; they come in various types, each tailored to address specific aspects of manufacturing and compliance. Understanding these different audit types helps companies choose the right approach for their unique needs and challenges. Each type has its distinct focus, pros, and cons, and they collectively contribute to a comprehensive risk management strategy.
Manufacturers may engage in several forms of audits, including evaluations before production begins, during active production, after production is complete, and audits focusing on social, environmental, and safety standards. These specialized audits ensure that every facet of the manufacturing process is scrutinized for compliance, efficiency, and ethical considerations. By differentiating between these audit types, organizations can better tailor their oversight strategies to address specific operational nuances and market demands.
Pre-Production Audits
Pre-production audits are conducted before the manufacturing process begins. They assess the factory’s readiness in terms of equipment, workforce, and systems to meet production standards.
- Pros:
- Identifies potential issues early
- Prevents costly disruptions
- Cons:
- May delay production schedules
- Requires upfront investment of time and resources
In-Production Audits
In-production audits occur during the manufacturing process, allowing real-time monitoring of quality and operational consistency.
- Pros:
- Real-time issue identification
- Immediate corrective actions possible
- Cons:
- Can disrupt production flow if not managed carefully
- Limited scope for long-term strategic assessment
Post-Production Audits
Post-production audits evaluate finished goods to ensure they meet quality and compliance standards before market release.
- Pros:
- Ensures final product quality
- Acts as a final safety net
- Cons:
- Issues found may require costly rework
- Limited impact on process improvements during production
Social Compliance Audits
Social compliance audits focus on labor practices, worker conditions, and ethical manufacturing practices.
- Pros:
- Enhances brand reputation
- Encourages fair labor practices
- Cons:
- Can be time-consuming and complex
- May face resistance in regions with lax labor laws
Environmental & Sustainability Audits
These audits assess a factory’s adherence to environmental regulations and its commitment to sustainable practices.
- Pros:
- Promotes environmental responsibility
- Identifies energy and resource efficiencies
- Cons:
- Implementation can be costly
- Standards may vary significantly by region
Security & Safety Audits
Security and safety audits focus on protecting workers and assets by evaluating risk management and emergency preparedness protocols.
- Pros:
- Enhances workplace safety
- Reduces liability risks
- Cons:
- Requires continuous monitoring
- May necessitate frequent updates to protocols
What Are the Main Components of an Effective Factory Audit?
An effective factory audit is a comprehensive examination that covers multiple dimensions of a facility’s operations. It scrutinizes both the physical and procedural aspects of production to ensure that every element meets stringent standards. This level of detail helps companies safeguard product quality, enforce regulatory compliance, and streamline operations for enhanced efficiency. The audit process is methodical, combining on-site inspections, detailed documentation, and rigorous evaluations of manufacturing practices.
To achieve a holistic view, auditors conduct a range of activities that capture both qualitative and quantitative data. They inspect machinery and production lines, review process documentation, and even engage with workers to assess the practical implementation of established protocols. This multifaceted approach is crucial in uncovering latent issues that might not be immediately visible through superficial inspections.
Before presenting a concise list of essential components, it is important to understand that every audit must blend physical assessments with in-depth document reviews and personnel interactions. These practices ensure that the audit is not merely a tick-box exercise but a dynamic process that fosters continuous improvement. The core components of an effective factory audit include:
- Facility inspections
- Document reviews
- Worker interviews
- Process evaluations
- Quality control checks
This comprehensive methodology ensures that every aspect of production is scrutinized, paving the way for improved operational reliability and long-term supply chain security.
How to Conduct a Comprehensive Factory Audit?
Conducting a comprehensive factory audit requires meticulous planning, structured execution, and thorough follow-up. The process begins with careful preparations and culminates in the detailed documentation of findings, ensuring that every insight leads to actionable improvements. This step-by-step guide is designed to help companies plan and execute audits that are both efficient and insightful.
The process is divided into several key stages, each of which is crucial in building a complete picture of the facility’s operational status. By addressing everything from pre-audit preparations to the final reporting of findings, organizations can create a framework that not only identifies areas for improvement but also lays the groundwork for continuous progress. Prior to outlining the key stages, it is essential to emphasize that each step plays a vital role in ensuring the audit’s overall success.
- Key Stages in the Audit Process:
- Initial planning and risk assessment
- On-site inspections and data collection
- Analysis of findings and documentation
- Review meeting with management
- Follow-up actions and corrective measures
Within this structured framework, the audit is further broken down into specific focus areas:
What Preparations are Necessary Before the Audit?
Before stepping into the facility, auditors must ensure all preparatory steps are completed. This includes setting clear objectives and assembling the right team.
- Preparatory Steps:
- Defining audit criteria
- Assembling the audit team
- Scheduling the visit
- Gathering previous audit reports
What Key Areas Should Be Focused on During the Audit?
During the on-site visit, it is essential to concentrate on core operational areas. Auditors must pay close attention to critical aspects that directly influence product quality and safety.
- Focus Areas:
- Manufacturing processes
- Quality control measures
- Labor practices
- Safety protocols
- Environmental compliance
How Should Audit Findings be Documented and Reported?
Proper documentation is vital for ensuring that audit findings lead to meaningful improvements. A well-structured report not only highlights issues but also provides a roadmap for corrective actions.
- Reporting Structure:
- Clear summary of findings
- Detailed observations and evidence
- Recommendations for corrective actions
- Follow-up timelines and responsibilities
This systematic approach to planning, executing, and documenting audits ensures that every factory inspection contributes to a robust and resilient supply chain.
What Are the Advantages of Regular Factory Audits?
Regular factory audits serve as the backbone of a robust quality assurance and risk management framework. By routinely scrutinizing production processes, companies are able to stay ahead of potential pitfalls and continuously enhance operational standards. Consistent auditing helps to reinforce internal controls, ensuring that deviations are swiftly identified and rectified, thereby minimizing the risk of production halts or quality failures.
A routine audit not only bolsters quality control but also fosters an environment of transparency and accountability across the organization. With periodic reviews, management gains valuable insights into operational trends and recurring issues, which facilitates proactive decision-making. This ongoing commitment to evaluation and improvement ultimately leads to more efficient production processes, greater supplier reliability, and significant cost savings by addressing problems early on.
Before listing the key advantages, it is important to recognize that the benefits of regular audits extend beyond immediate operational improvements. They also create a culture of continuous improvement and strategic foresight, essential in the fast-paced world of global manufacturing. The primary advantages of conducting regular factory audits include:
- Enhanced quality control
- Risk mitigation
- Compliance with international standards
- Improved transparency
- Cost savings through early problem detection
These benefits underscore the strategic importance of regular audits, ensuring that companies not only maintain high standards but also achieve long-term operational excellence.
How Do Factory Audits Improve Global Supply Chain Efficiency?
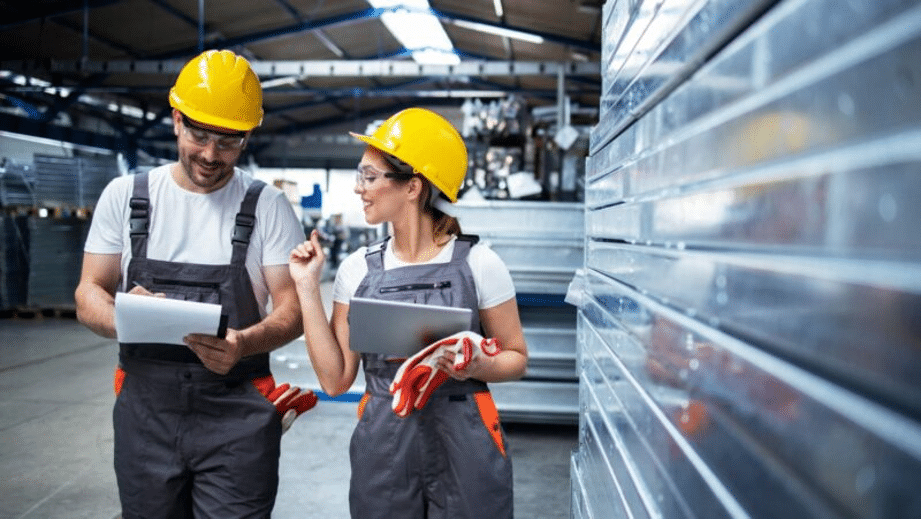
Factory audits are instrumental in streamlining operations, reducing production delays, and reinforcing overall supply chain efficiency. By identifying bottlenecks and inefficiencies within the production process, audits enable companies to fine-tune their operations and maintain a steady flow of high-quality products. The systematic nature of these evaluations encourages continuous process improvements that directly translate into enhanced reliability and operational effectiveness.
When audits uncover operational shortcomings, the resulting insights lead to targeted interventions that improve overall manufacturing performance. These interventions often include process optimization, better resource allocation, and enhanced communication between different segments of the supply chain. By facilitating these improvements, factory audits contribute significantly to reducing downtime and minimizing disruptions that can arise from non-compliance or operational failures.
Before enumerating the specific efficiency improvements, it is crucial to appreciate that every audit drives a cycle of assessment and remediation. The feedback loop created through regular audits ensures that each facility continuously evolves, adapting to changing market conditions and operational demands. The primary ways in which factory audits improve global supply chain efficiency are:
- Reduced production downtime
- Enhanced supplier reliability
- Improved logistical planning
These improvements not only accelerate production timelines but also ensure that the supply chain remains resilient and capable of responding effectively to dynamic global challenges.
What Are the Common Challenges in Conducting Factory Audits?
Factory audits, while immensely beneficial, are not without their challenges. Auditors often encounter obstacles that can hinder the thoroughness and accuracy of the evaluation process. These challenges range from language and cultural barriers to restricted access to certain areas within the facility, all of which can impede a complete assessment of operational practices.
In addition, the variability of audit standards and the potential for fraudulent practices further complicate the auditing process. Organizations sometimes struggle to implement uniform protocols across diverse regions, which may result in inconsistent audit outcomes. Such challenges require auditors to be not only meticulous in their evaluations but also adaptable in their approach. Addressing these issues head-on is essential for ensuring that audits deliver reliable and actionable insights.
Before outlining specific challenges, it is necessary to understand that these obstacles are often symptomatic of broader operational and cultural complexities inherent in global manufacturing. The most common challenges in conducting factory audits include:
- Language and cultural barriers
- Limited access to certain facility areas
- Inconsistent audit standards
- Potential audit fraud
How Can These Challenges Be Overcome?
Overcoming these challenges demands a strategic approach that leverages local expertise and technological innovation. Practical solutions often involve forming local partnerships and standardizing audit protocols to ensure consistency across regions.
- Strategies:
- Establishing local partnerships
- Adopting standardized protocols
- Integrating advanced technology
- Providing continuous training
These strategies enable auditors to navigate cultural nuances and regulatory variances, thereby enhancing the overall efficacy of the audit process.
What Are the Regulatory and Compliance Considerations?
Factory audits operate within a complex framework of legal and regulatory requirements that vary across different regions and industries. Companies must adhere to a multitude of global regulations, certifications, and industry standards designed to ensure both product safety and ethical manufacturing practices. The regulatory landscape plays a critical role in shaping audit methodologies and determining the benchmarks for compliance.
Organizations must remain agile and informed about evolving legal standards, as non-compliance can result in severe financial and reputational consequences. A robust audit process is essential for verifying that manufacturing practices meet these stringent regulatory requirements, thereby safeguarding the company against legal liabilities and operational disruptions. Before highlighting the specific regulatory aspects, it is important to acknowledge that adhering to these frameworks is not merely a legal obligation but also a strategic advantage that reinforces stakeholder trust.
The key regulatory and compliance considerations include:
- Adherence to global regulations
- Obtaining relevant certifications
- Meeting industry standards
How Do International Standards Influence Factory Audits?
International standards, such as ISO and SA8000, serve as benchmarks that drive audit practices globally. These standards ensure that factories not only maintain quality but also operate ethically and sustainably, influencing audit criteria and methodologies.
What Role Do Governmental Agencies Play in Audit Compliance?
Governmental agencies are pivotal in enforcing compliance and ensuring that manufacturers adhere to established standards. Their involvement includes monitoring, auditing, and imposing penalties for non-compliance. Before listing their roles, it is vital to understand that governmental oversight is essential for maintaining public trust and ensuring industry-wide accountability.
- Governmental Involvement:
- Monitoring compliance
- Enforcing regulations
- Supporting industry certifications
- Mandating corrective measures
This regulatory framework provides the foundation for robust factory audits, ensuring that all stakeholders operate within a safe and legally compliant environment.
How Can Technology Enhance Factory Audits?
The integration of modern technology into factory audits is revolutionizing the way inspections are conducted and data is analyzed. Digital audit platforms, remote auditing tools, AI-driven analytics, and blockchain-based traceability systems are transforming traditional methods, making audits more efficient, accurate, and transparent. Technological advancements facilitate real-time monitoring, enhance data collection, and streamline communication between auditors and facility managers.
By embracing these tools, organizations can overcome many of the challenges traditionally associated with manual audits. Technology not only expedites the data collection process but also ensures that audit findings are documented and analyzed with greater precision. Before presenting the specific technologies that enhance audit processes, it is important to emphasize that these innovations are integral to maintaining a competitive edge in today’s fast-paced manufacturing environment.
The key technologies driving modern factory audits include:
- Digital audit platforms
- Remote auditing tools
- AI-driven analytics
- Blockchain for traceability
What are Best Practices for Implementing Audit Technology?
Effective integration of technology into audits requires careful planning and adherence to best practices. Organizations must ensure that new systems are compatible with existing processes and that staff are adequately trained.
- Best Practices:
- Ensuring data security
- Providing staff training
- Integrating new systems with existing processes
How Do Remote Audits Compare to Traditional On-Site Audits?
Remote audits have emerged as a viable alternative to traditional on-site inspections, offering flexibility and cost-effectiveness. While remote audits facilitate broader coverage and reduced travel time, they may face limitations in terms of physical verification and hands-on evaluations.
- Comparison Points:
- Advantages: reduced travel costs, broader coverage, faster data collection
- Limitations: limited physical inspection, reliance on digital data accuracy
What Are the Best Practices for Communicating Audit Results to Stakeholders?
Effectively communicating audit results is as important as conducting the audits themselves. Clear, transparent, and actionable reporting builds trust among stakeholders and fosters collaborative efforts to address identified issues. The way audit outcomes are communicated can drive improvements, facilitate compliance, and enhance the overall reputation of the supply chain.
Before detailing specific strategies, it is important to understand that communication must be tailored to the audience. Whether addressing suppliers, manufacturers, or regulatory bodies, the clarity and structure of the report are paramount. A well-crafted report not only highlights findings but also provides constructive feedback and recommendations for future actions.
The recommended strategies for effective communication include:
- Clear and concise reporting
- Transparency in outlining findings
- Actionable feedback and follow-up plans
How Should Suppliers and Manufacturers Be Informed of Audit Outcomes?
Sharing audit outcomes requires a collaborative approach that fosters mutual understanding and joint problem-solving. Detailed, yet accessible reports are essential in communicating complex findings without overwhelming the recipients.
- Communication Methods:
- Regular review meetings
- Written reports with executive summaries
- Interactive presentations and follow-up workshops
What is the Role of Audit Reports in Strengthening Supplier Relationships?
Detailed audit reports contribute to long-term supplier relationships by building trust and encouraging continuous improvement. Transparent reporting helps suppliers understand expectations and work collaboratively toward compliance.
- Relationship-Building Strategies:
- Providing constructive, actionable insights
- Encouraging open dialogue about challenges
- Establishing joint improvement initiatives
How to Integrate Factory Audits into a Broader Supply Chain Risk Management Strategy?
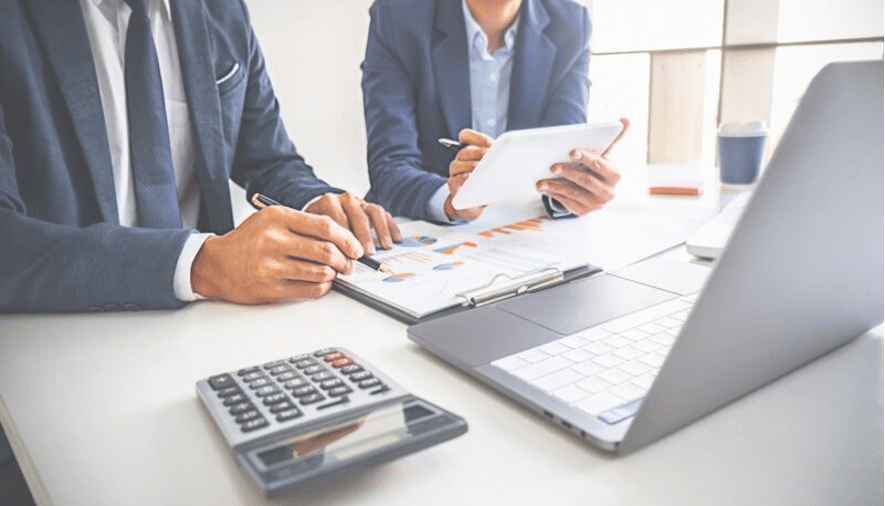
Integrating factory audits into a broader supply chain risk management strategy is essential for holistic operational resilience. By aligning audit processes with overall risk management frameworks, organizations can ensure that every potential threat is identified and addressed proactively. This integration creates a synergistic effect, where audits not only reveal operational weaknesses but also inform strategic risk mitigation efforts across the entire supply chain.
The process begins with recognizing that audits are a critical component of an overarching risk management plan. They provide the data and insights necessary to assess vulnerabilities and implement corrective measures in a timely fashion. This alignment helps companies stay ahead of disruptions and maintain a consistent standard of quality and compliance across all stages of production.
Before summarizing the integration steps, it is crucial to note that a comprehensive risk management strategy encompasses not just audits but also a broader framework that includes continuous monitoring, strategic planning, and contingency measures. The essential steps for integrating factory audits into risk management include:
- Incorporating audit findings into risk assessments
- Aligning audit schedules with risk review cycles
- Integrating corrective actions into broader operational plans
What Are the Key Elements of a Supply Chain Risk Management Framework?
A robust risk management framework consists of several interrelated components that work together to mitigate operational risks. Each element plays a crucial role in ensuring that the supply chain remains resilient in the face of unforeseen challenges.
- Framework Elements:
- Risk identification
- Risk assessment
- Mitigation strategies
- Contingency planning
This comprehensive approach enables organizations to leverage audit data effectively, creating a dynamic environment where risks are managed in real time.
What Are the Future Trends in Factory Auditing and Supply Chain Security?
As global supply chains evolve, so too do the methods and technologies used in factory audits. Emerging trends such as increased automation, digital auditing platforms, enhanced data analytics, and a growing focus on sustainability are poised to redefine audit practices. These innovations not only streamline the audit process but also enhance its accuracy, efficiency, and overall impact on supply chain security.
The future of factory audits is marked by the integration of cutting-edge technologies that enable real-time monitoring and predictive analysis. With tools like artificial intelligence and blockchain, auditors can uncover hidden patterns and anticipate risks before they manifest into larger problems. This technological shift is fundamentally transforming how organizations approach compliance and quality control in an increasingly dynamic marketplace.
Before exploring specific future trends, it is important to acknowledge that innovation in auditing practices is driven by both technological advancements and evolving market demands. The key trends shaping the future of factory audits include:
- Increased automation
- The rise of digital audits
- Enhanced data analytics
- Growing emphasis on sustainability
How Will AI and Machine Learning Transform Factory Auditing?
Artificial intelligence and machine learning are set to revolutionize audit processes by enabling more precise data analysis and predictive insights. These technologies can automate routine tasks, flag anomalies in real time, and provide auditors with actionable intelligence that enhances overall accuracy.
- Impacts of AI & Machine Learning:
- Improved audit accuracy
- Faster data processing
- Enhanced predictive capabilities
How Do Global Events Impact Audit Practices?
Global events, from pandemics to geopolitical tensions, force organizations to continually reassess their audit methodologies. These events often trigger shifts in regulatory requirements and operational strategies, demanding greater agility in audit practices.
- Examples of Global Impacts:
- Pandemics altering on-site access protocols
- Geopolitical tensions affecting supply chain logistics
- Trade disputes prompting tighter regulatory scrutiny
Conclusion
Factory audits are not merely a compliance exercise; they are the cornerstone of a resilient global supply chain. In a landscape defined by unpredictability, rigorous evaluations ensure that every production facility meets the highest standards of quality, safety, and ethical conduct. From identifying risks before they escalate to fostering continuous improvement, audits drive operational excellence across continents. Their integration into broader risk management frameworks and the adoption of advanced technologies further enhance their impact, paving the way for a future where supply chains are both secure and agile. Unpredictably, every insight gleaned from an audit reinforces a commitment to excellence, and each recommendation resonates with the promise of a safer, more efficient production process. The interplay of meticulous planning, technological innovation, and proactive communication ultimately creates a robust environment where every stakeholder—from manufacturers to end consumers—benefits from an unwavering standard of quality and reliability.