CNC (Computer Numerical Control) automation has become a key technology in modern manufacturing, not only improving production efficiency but also significantly reducing human error in the process. For factories that produce precision parts and complex products, CNC machines are core technologies for boosting productivity and lowering costs. As automation advances, these machines have gradually integrated into various industries, playing a critical role in crane manufacturing and related applications.
Key Advantages of CNC Automation
CNC automation allows manufacturers to control machine operations through digital instructions, minimizing the need for manual intervention. This not only increases production efficiency but also ensures product precision and consistency. The main advantages of CNC automation include:
- Cost Reduction: CNC machines can operate around the clock, reducing material waste and minimizing production costs.
- Faster Production Speed: CNC machines can perform multiple tasks simultaneously, significantly faster than traditional manual operations.
- Consistency and Mass Production: Once programmed, CNC machines can maintain high-quality consistency across large-scale production.
- Safety: By reducing direct human involvement in hazardous tasks, CNC automation significantly improves workplace safety.
Common CNC Machines and Their Applications in Crane Manufacturing
There are many types of CNC machines used across various manufacturing processes. Below are some common CNC machines and their specific applications in crane manufacturing:
- Milling Machines: CNC milling machines are ideal for manufacturing key crane parts such as brackets, pulley assemblies, and wheels. Their precision ensures these components have high load capacity and durability, suitable for extreme working conditions.
- Lathes: CNC lathes are used to process components like crane drums and bearings, ensuring high accuracy and durability. These parts are critical to smooth crane operation, where any error could impact the equipment’s safety and performance.
- Plasma Cutters: In large-scale crane manufacturing, CNC plasma cutters can quickly and accurately cut steel for main beams, columns, and other vital structures. Plasma cutting offers efficiency and precision, meeting the high-strength requirements of crane manufacturing.
- Water Jet Cutters: Widely used for cutting various materials such as metal and glass, water jet cutters play an important role in crane manufacturing, especially when processing thick materials or irregularly shaped components. Water jet cutters offer exceptional precision and flexibility.
The Integration of CNC Automation and Lifting Equipment
CNC automation not only plays a critical role in crane manufacturing but can also integrate seamlessly with crane operations. For example, cranes’ Rail Guided Vehicles (RGVs) can be integrated with CNC machines, using automated systems to transport materials within a factory. This automation process reduces manual intervention, increasing production efficiency and overall operational safety.
In crane manufacturing, parts produced by CNC machines must not only meet high precision standards but also be durable and strong. CNC automation ensures these requirements are met while minimizing errors from manual processes. This is crucial for the safety and long-term use of lifting equipment.
Case Study: Intelligent Production at Henan Kuangshan Crane
As a leading company in China’s crane manufacturing industry, Henan Kuangshan Crane Co., Ltd. has greatly improved its production efficiency and product quality by adopting CNC automation and intelligent manufacturing systems. Henan Kuangshan Crane operates a 740,000-square-meter intelligent industrial park with over 100 automated production lines, covering the full production process from component machining to complete crane assembly.
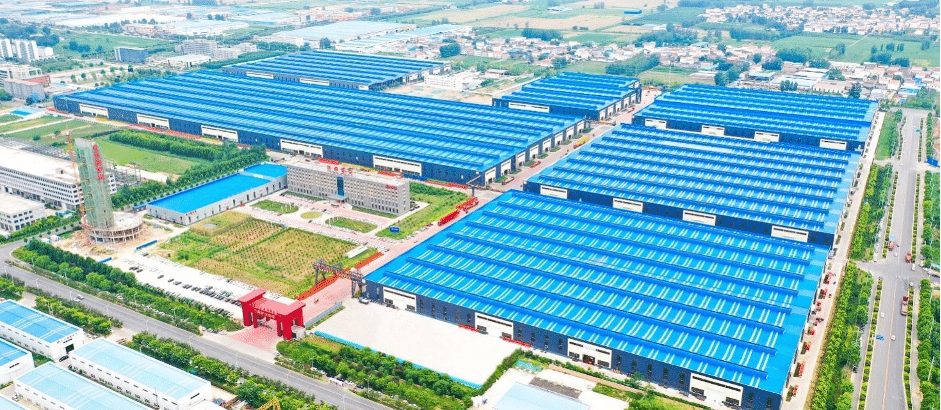
Henan Kuangshan Crane’s intelligent manufacturing system utilizes CNC automation for efficient production in its workshops. In their No. 4 workshop, hundreds of robots replace manual labor for key processes like welding and assembly. These robots use laser scanning technology to automatically identify the start of welding seams and ensure welding precision through arc tracking technology.
This not only reduces errors in manual operations but also significantly increases welding efficiency. Compared to traditional welding techniques, Henan Kuangshan Crane’s automated production lines have improved efficiency by 30%, with welding quality approaching zero defects.
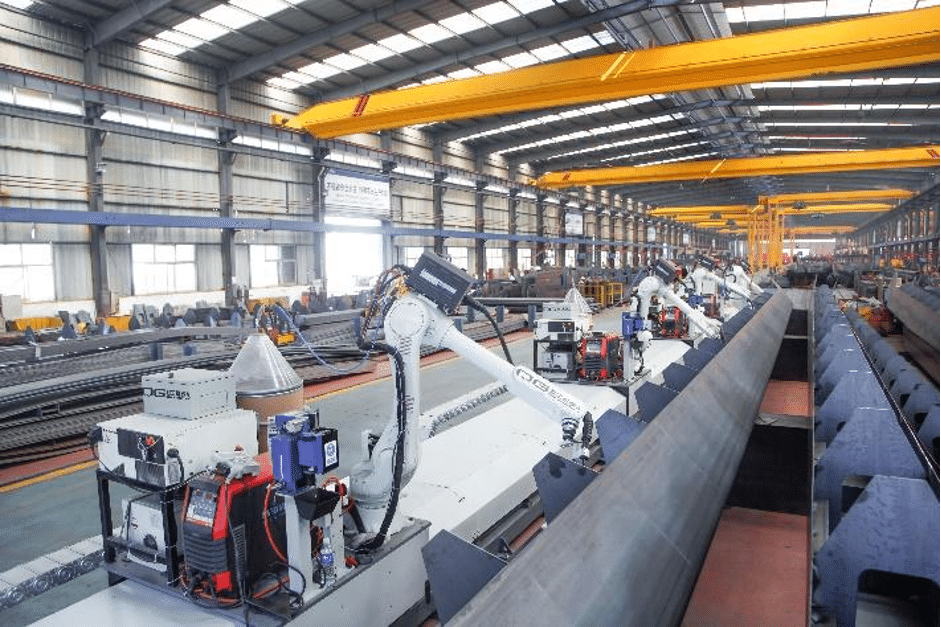
Furthermore, Henan Kuangshan Crane uses CNC automation for customized production to meet clients’ unique needs. For example, their fully automatic clean explosion-proof cranes feature intelligent functions such as automatic tool adjustment and obstacle avoidance, enabling high-precision tasks in complex working environments. These cranes are widely used in industries such as energy and mining, contributing to Henan Kuangshan Crane’s competitive advantage in domestic and international markets.
The Role of CNC Operators in Automation
While CNC automation significantly reduces reliance on manual labor, skilled CNC operators still play an irreplaceable role in programming, debugging, and quality monitoring during the manufacturing process. In crane manufacturing, CNC operators ensure that each critical component is accurately produced to guarantee the crane’s safe operation.
Operators are responsible not only for writing CNC programs but also for monitoring machine operations to ensure all steps are executed as designed. As CNC automation technology continues to evolve, operators must also develop skills to work collaboratively with robotic systems, enabling more automated operations and further enhancing production efficiency.
Conclusion
CNC automation plays an indispensable role in manufacturing, and in the crane manufacturing sector, it brings significant advantages in terms of product quality and production efficiency. By integrating CNC automation with crane production, manufacturers can better meet complex production demands while improving overall operational efficiency in factories.
Henan Kuangshan Crane, a representative of crane enterprises, has greatly enhanced its production efficiency, product quality, and global competitiveness through intelligent production and CNC automation. As automation technology continues to evolve, the application of CNC machines will become more widespread, especially in high-demand manufacturing sectors like crane production. Whether it’s machining crane components or integrating automated material transport systems, CNC automation is driving the industry toward higher efficiency and intelligence.
For manufacturers, fully leveraging CNC automation technology can not only enhance product competitiveness but also secure a leading position in modern industry. If you are considering how to apply CNC automation to crane manufacturing, now is an excellent time. With these advanced technologies, you can further optimize production processes and achieve greater economic benefits.