Manufacturers wanting to produce parts for their products often find themselves at a crossroads. They are hesitating in weighing the pros and cons of two prominent manufacturing methods: CNC rapid prototyping and injection molding. Both processes offer unique advantages and cater to different production requirements, which forces manufacturers to evaluate their specific needs and objectives carefully before selecting the most suitable method for part production.
What Are CNC Rapid Prototyping and Injection Molding? How Do They Work?
- CNC rapid prototyping is a manufacturing process that utilizes Computer Numerical Control (CNC) machines to quickly produce parts or prototypes from various materials, such as metals, plastics, or composites. In this manufacturing process, a digital 3D model is used to guide the CNC machine, which removes material from a solid block or workpiece to create the desired part or prototype with high precision and accuracy.
CNC rapid prototyping is ideal for creating functional prototypes, low-volume production runs, and complex parts with intricate geometries that might be difficult or impossible to achieve through other manufacturing methods like injection molding. This process offers several benefits, including shorter lead times, greater design freedom, high-quality parts, and the ability to make design alterations without significant additional costs.
- Injection molding, on the contrary, is an additive manufacturing process that involves injecting molten material into a pre-designed mold cavity under high pressure. Once the material cools and solidifies within the mold, it replicates the shape of the mold cavity, and the final part is ejected or removed from the mold.
Injection molding is well-suited for mass production of parts with consistent quality, as it allows for the rapid and cost-effective manufacturing of large quantities of identical components. This process offers several advantages, including high production rates, low per-unit cost for large volumes, and the ability to create parts with complex geometries and intricate features. However, injection molding typically requires a significant upfront investment in mold design and manufacturing, making it less viable for low-volume production or projects with frequent design changes.
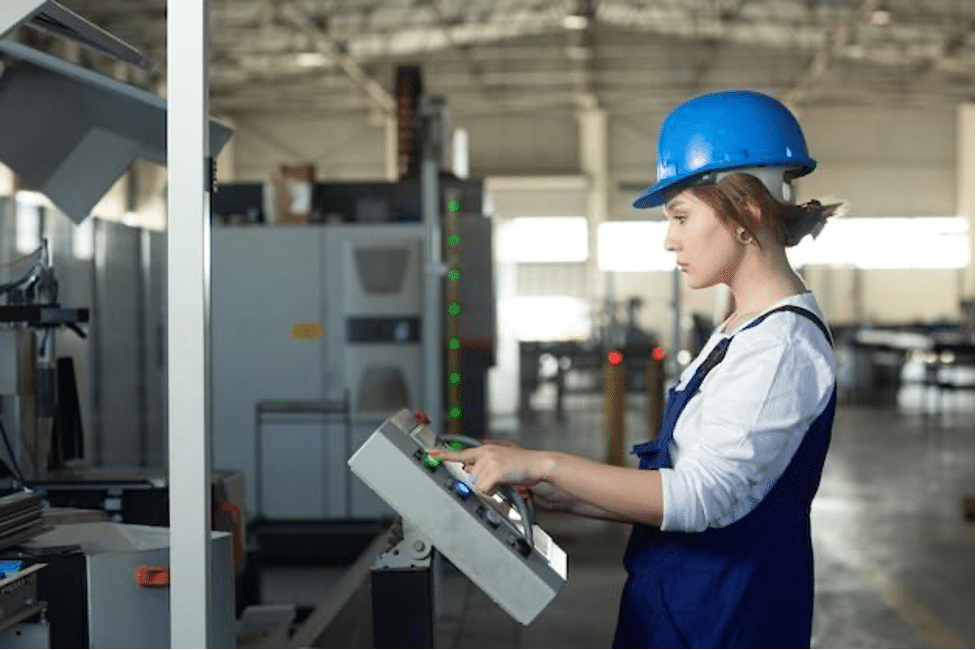
Comparing CNC Rapid Prototyping and Injection Molding
CNC rapid prototyping and injection molding can be compared based on the following factors.
1. Low MOQ (minimum order quantity)
CNC rapid prototyping is ideal for low-volume production, as there are no expensive mold costs. In contrast, injection molding typically requires a higher minimum order quantity to justify the upfront mold expenses.
2. Good prototypes
CNC rapid prototyping is an excellent choice for creating functional prototypes, as it allows manufacturers to test and refine designs before committing to large-scale production. This is not the case in injection molding, however, as most manufacturers are hesitant to test the things when expensive mold is involved in the project.
3. Freedom of design
CNC rapid prototyping offers greater design freedom, enabling the production of intricate and complex geometries that may be difficult to achieve through injection molding.
4. Quality
CNC prototypes generally exhibit higher dimensional accuracy and precision compared to injection molded parts, as the process eliminates the risk of shrinkage and warping associated with molding.
5. Lead time
CNC rapid prototyping often has shorter lead times than injection molding, as it does not require the lengthy process of designing and manufacturing molds.
6. Alteration
Design changes are easier to implement in CNC rapid prototyping, as they can be made directly in the digital file without the need for modifying or creating new molds.
7. Strength
CNC rapid prototyping can produce parts with consistent material properties and strength, whereas injection-molded parts may have variable strength due to the cooling process.
8. Surface finish
CNC machined parts typically have a superior surface finish compared to injection molded parts, as the latter may exhibit surface defects like sink marks, flash, or weld lines.
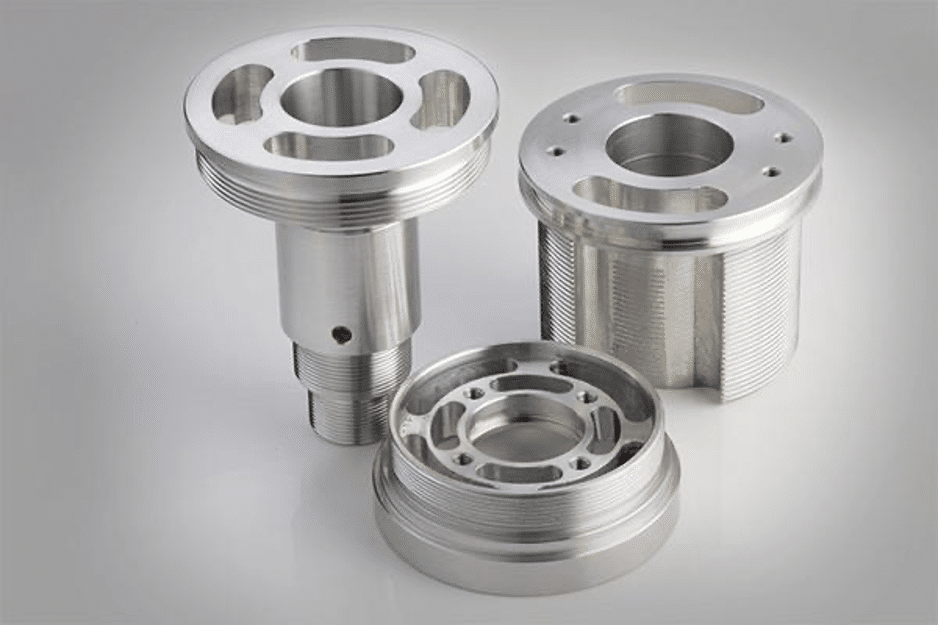
KAIAO’s Recommendation
KAIAO is a reliable rapid prototype supplier with over 20 years of experience. Utilizing advanced CNC software and equipment, they produce precision machining parts that achieve the highest international production standards. With a highly efficient process, they are committed to meeting client deadlines through fast quotations and standardized production processes. Their extensive material choices include engineering plastics such as ABS, PMMA, and PVC and engineering alloys like aluminum, titanium, and stainless steel. KAIAO ensures precision and quality in every project through experienced management, machine programming and operation, material selection, and inspection.
Wrapping Up
KAIAO is a leading supplier of CNC prototyping services, products, and solutions. Under the guidance of experienced professionals, KAIAO excels in providing exceptional product development experiences. With over 100 technical experts and a 3,000 sq. meter production plant, KAIAO has served more than 10,000 satisfied customers across 26 industries. KAIAO offers a wide range of services, including CNC rapid precision machining, surface finishing, and rapid sheet metal fabrication. Choosing KAIAO for rapid prototyping ensures industry-leading expertise, cutting-edge equipment, intelligent quotations, and rapid completion times without compromising quality.