The injection molding process is fundamentally simple, but it has a lot of nuances and innate complexity. These complexities determine the difference between good and bad manufacturers. One of these complex elements is the type of gate to use for a molding process.
An injection molding gate determines the structural integrity of mold. It also affects how easy or hard demolding and accuracy will be. There are pros and cons to all the injection molding gate designs. This article will focus on the direct and side gates, to give you an in-depth analysis of the two variants.
Importance of Injection Molding Gate Design
Injection molding gate designs are crucial because they determine the quality of the finished product. The gates carry the molten plastic from the nozzles to the mold cavity. The structural integrity of the finished product may vary depending on the gate type.
Optimal gate locations tend to produce better results, while poor gate design can lead to flaws or defects in the molded part. The gates also play a slight role in the aesthetic side of things since removing a sprue without leaving a witness mark is exceedingly hard. So, the plastic injection mold design needs to have the gate in a less conspicuous section of the product.
Injection Molding Gate Structural Difference: Direct Vs. Side
Injection molding gate designs come in quite a few varieties. The direct and side gates are usually the most common in the industry. The fundamental difference between their structures is their position on the mold.
Direct gates inject the molten pallets directly through the sprue cavity. Manufacturers need to place it in a centralized position for the best effect due to its nature. But that helps it inject the plastic more evenly. The only downside to the direct gate is that it usually leaves a very noticeable witness mark.
Side gates- as the name suggests; are placed at the side of the molded product. The feeder pushes the molten plastic through a sprue that connects the mold with a smaller gate. You would usually see the side gates on the parting line of the molded item.
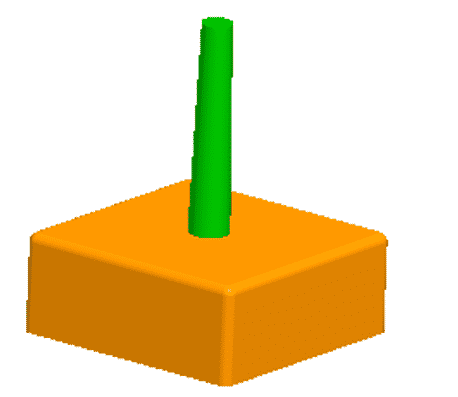
Gate Vs. Side Injection Molding Gate Comparison
Here’s a comparative breakdown of the effectiveness of the two injection molding gate designs:
1. Size Accuracy
Both of these injection molding gate designs have high accuracy. In order to maintain the precise size of the molding products, manufacturers need quite a bit of experience to design the temperature profiles, guaranteeing a defect-free molded part.
2. Filling
Direct injection molding gate has a distinct advantage over the side gate when it comes to filling. The direct one has a centralized position which helps it spread the molten plastic more evenly. It usually gives a more uniform filling than the side gate.
3. Demold
Direct gates use a single sprue cavity to inject all the molten material. That creates a particularly large sprue. Demolding a direct gate is problematic because it generally has more vacuum pressure. The Side gate only leaves a small sprue and does not create too much pressure. So demolding them is usually easier.
4. Deformation
Direct injection molding gate has a single cavity to send all the molten material. It also applies all the material from the base of the mold. That creates a lot of residual stress, which can lead to deformation.
Side gates have smaller openings and do not apply too much pressure. That results in lesser residual stress. So, the deformity is less likely to happen in the finished product.
5. Stress Loss
The progressive decrease of residual stress is greater with the side gates, while the direct gates maintain a uniform albeit higher stress retention.
Applications of Different Injection Molding Gates
Direct injection molding gates are good at transferring molten plastic evenly. That makes it a perfect choice for injection molding large parts. The direct gate also has the largest cavity among all the gates. That allows it to transfer highly viscous material, which other gates may struggle with.
Side gate is the most common variant of injection molding gates. Many smaller or common plastic molds are made with the side gate.
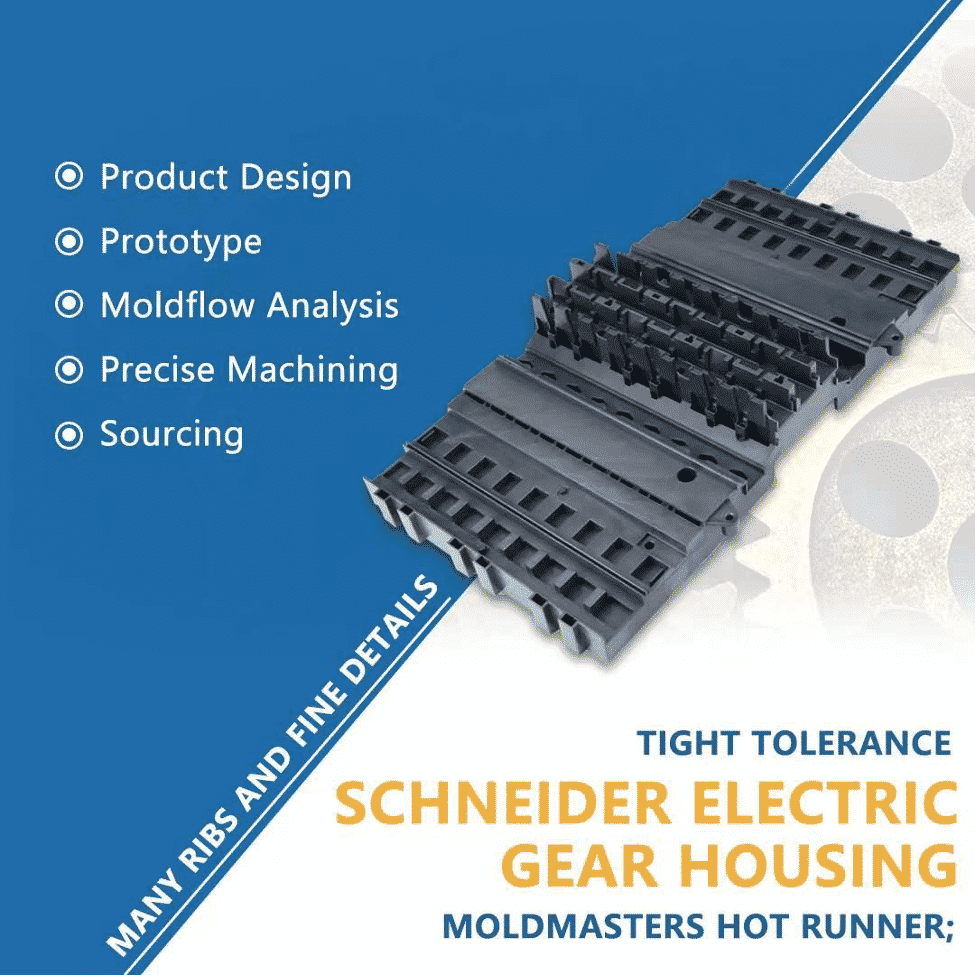
Conclusion
Low-quality molds will give you terrible finished products no matter what injection molding gate you use. Low-quality molds will give you terrible finished products no matter what injection molding gate you use. However, with Abery, who provides the best injection molds in the industry and ensures fast delivery to each of their customers, you will no longer suffer from low-quality injection molding products. Contact them right away to get the most satisfying injection mold supplies!