The wire harness manufacturing process involves bundling different electrical wires, often with many individual cables covered. In addition, it provides excellent protection from environmental and damaging factors while ensuring a protective sheath around standard, military-grade, and customized electrical wires.
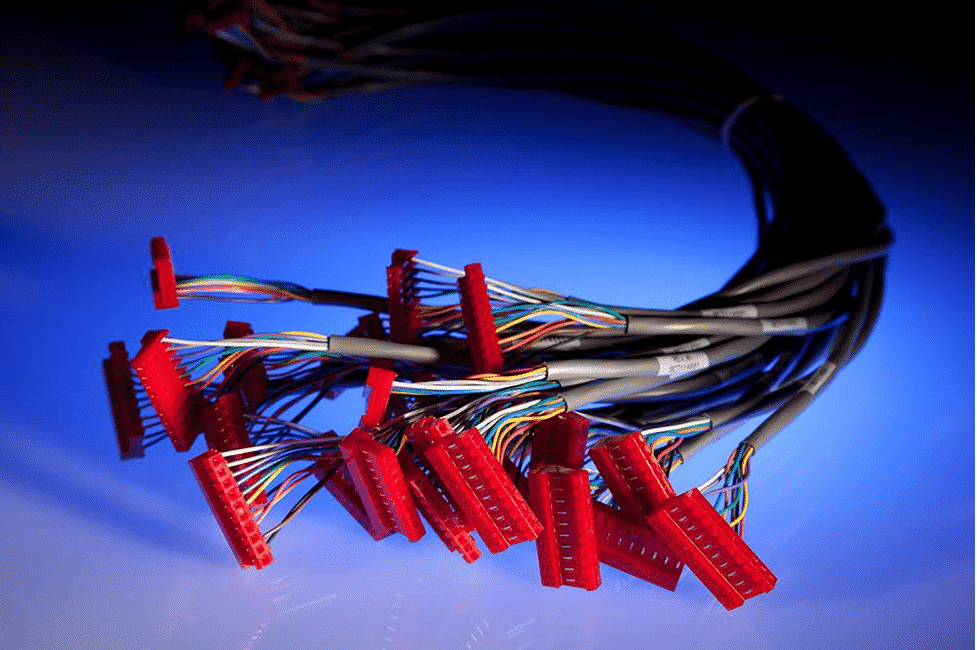
What Are Wire Harnesses and Their Advantages?
There are numerous organizations, businesses, and municipal companies that require a customized wire harness assembly process. Wire harness ranges from providing homes with power and communication services to ensuring telecommunication security between military installations.
The reasons these industries turn to professionals and industry leaders for the wire harness manufacturing process is because:
· Efficient optimization of space by grouping essential wires together
· Customized needs are met for unique applications
· Quality care and extended service life
· Improved security and safety
· Bespoke lengths and sizes are met without minimal to no errors
· And more!
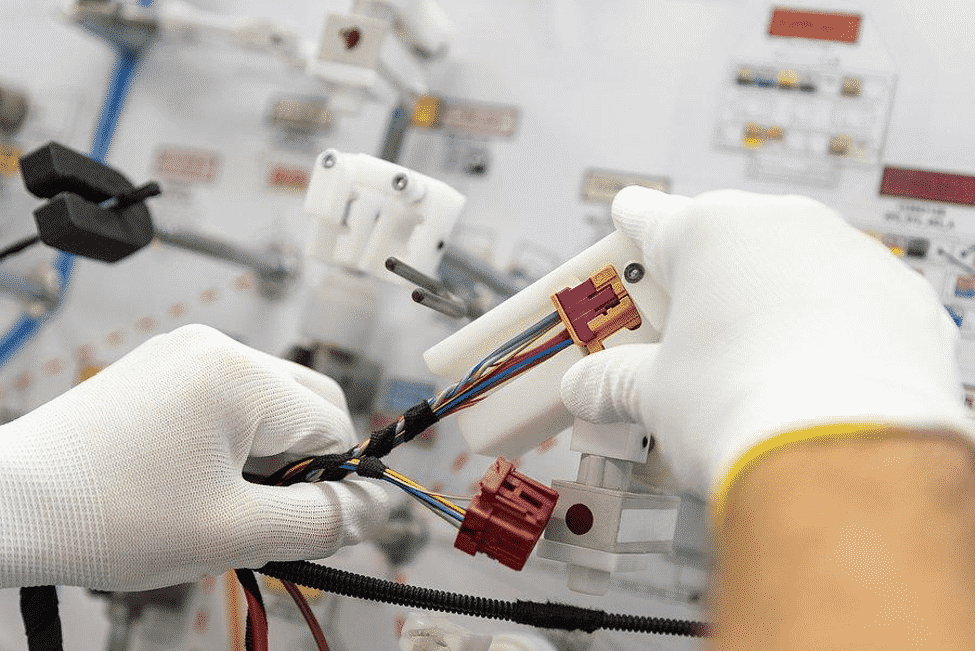
What Are the Steps in the Wire Harness Manufacturing Process?
These individual steps can vary depending on the order size and need, but they generally follow a similar pattern. The methods used are determined by the technology and production equipment available by the company you are working with and indicate what kind of work can be completed.
1 – Wire Cutting
Make sure the wires are being cut into the correct length and size through a wire-cutting machine.
2 – Stripping
Remove/strip the skin at the end of the wire. So the wire can be exposed and fit with any necessary terminals or housings.
3 – Tin Dipping
The end of the wire needs to be tinned so that the wire is delivered to the customer without loose strands.
4 – Crimp Terminal
The crimping process is stamping the wires to the terminals.
5 – Dispensing
Ensure wires are along predetermined paths as ordered forming, so each wire harness can be sent as its correctly designed.
6 – Twisted Wire
The twisted wire increases the immunity of the wire to interference.
7 – Testing
After each wire harness assembly process is complete, each product must undergo electrical safety testing. This step prevents potential damage and increases the reliability of the final product.
Many in the wire harness process still rely on manual labor to ensure the safety and design of each product. Getting the most of your next project should include working with a company that blends advanced equipment with qualified and experienced individual workers, testers, designers, engineers, technicians, and support staff.
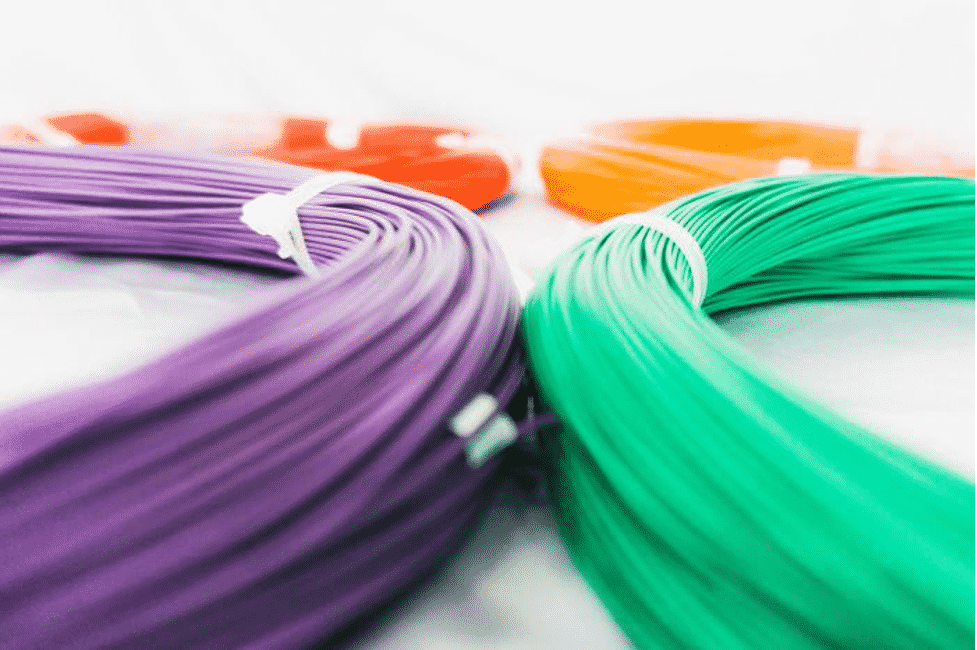
Features of a Qualified Wire Harness Manufacturer
The wire harness manufacturing process requires careful attention and experience for every output because electricity and communications rely on these products for safe and efficient use. Therefore, when selecting a manufacturer, you should always make sure they have a few qualifications.
Ask to review their advanced production equipment so that you can see if they are up to date on code, technology, and capability to fulfill your order. A good indication of this will be if they have a rich product line. The more diversity they offer, the more likely they are a fully outfitted company using the latest technology and equipment.
Check out some of the wire harness manufacturing process reviews for the companies you’re considering. Don’t be afraid to contact previous clients listed in their informational resources to verify that background. Instead, you want stable product quality every time they produce an order.
Make a special notation of the type of interactions you have with the company. For example, are you receiving high-quality customer service each time you reach out? Any reputable wire harness manufacturing process provider will emphasize customer service because it determines their competitive ability.
Choose Taifulong
Once you are looking for a tried and proven company with decades of experience, specifically in the wire harness manufacturing process, you should inquire with Taifulong.
They are a specialized wire and cable industry provider that has received acclaim as a “national Hi-tech Enterprise” and “Key Industry of Hi-tech in the China Torch Program.” Their wealth of knowledge and expert technicians are a perfect way to enhance your next project.
Offering stable products and high-quality customized service, Taifulong has won a lot of praise from customers worldwide. So don’t hesitate to call them today to schedule a consultation or visit their website to see the high-quality and diverse products they offer.