Tubing in most pressure fluid systems is the common area of failure compared to pumps or valves. Failing to close the shutdown costs hundreds of thousands of dollars per hour of production. A sudden rupture can stop this. This is why engineers initiate reliability by matching the pressure, chemistry, and temperature of the material that fits.
Fluoropolymers are a notable choice. Most designers choose PFA tubes due to their resistance to acids and their flexibility between -328°F and 500°F. Making the wrong decision invites leakages, contamination, and unplanned, expensive downtimes.
Understanding Pressure and Flow
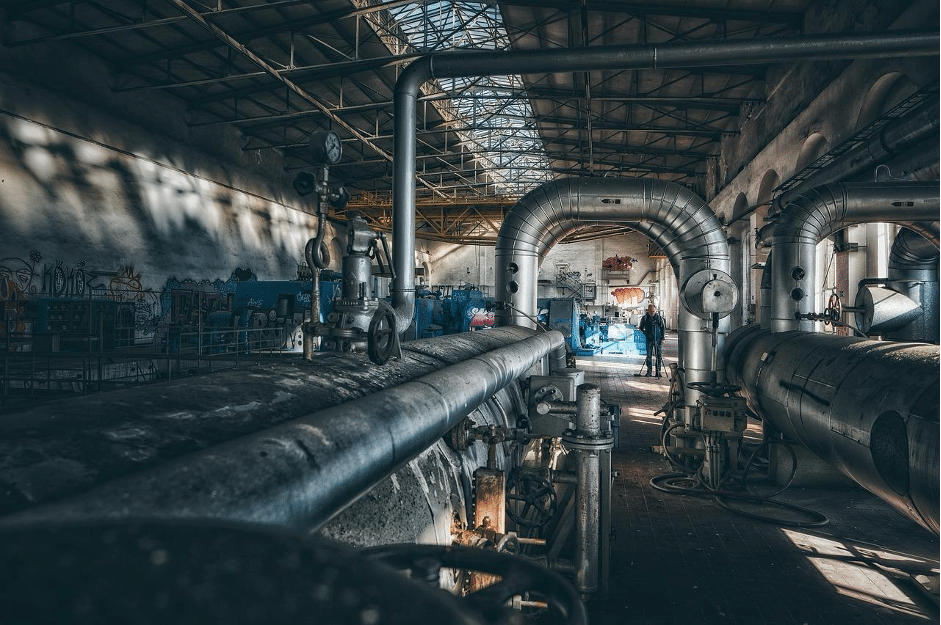
Designers apply ASME-based equations to calculate the maximum allowable working pressure. They consider the weight of the partial wall and its tensile strength. The rating is derived at higher temperatures because of the softening of polymers as heat increases. Best practice will include an overshoot factor of four to soak up transients. Failure to observe these leads to disastrous backfires that spray operators with harsh chemicals.
Within the line, speed encounters friction. A low-roughness fluoropolymer bore reduces pressure drop. Tight dimensions increase velocity, increase drops, and encourage cavitation in pumps.
Fluoropolymer Advantages Under Stress
Mostly inert and used in virtually all applications, PTFE, FEP, and PFA resist acids, bases, solvents, and oxidizers. Such detachment protects product purity during biopharma skids, semiconductor wet benches, and aggressive clean-in-places. It also prevents the leaching of small extractables in formulations. The polymers are low gas permeable, protecting labile reagents against atmospheric moisture.
Fluoropolymers bend at -100°F and maintain mechanical strength at 500°F, which metals can only dream about. Both FEP and PFA can transmit ultraviolet light, allowing designers to sterilize lines online using UVC lamps. Transparent walls assist in rapid bubble checking during chromatography runs. Viscous fluids leave the surface clear within seconds, and cleaning takes less time between batches, owing to the non-stick surface.
Choosing Tubing for High-Pressure Service
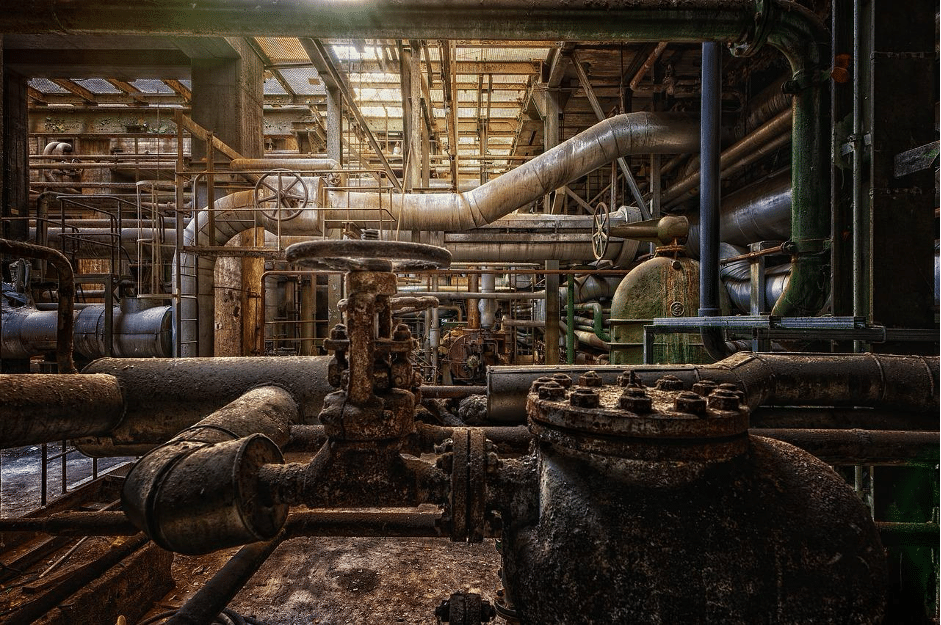
Wider bend radii are required with thicker walls, which increase burst pressure. The dimensions are kept tight with precision extrusion, which helps to ensure that the compression fittings are bitingly even and that they seal on the first bite. It is specification work that manufacturers publish the table connecting the diameter, wall, and working pressure with the speed of work.
Plant panels are densely lined in an elaborate contour. PFA can bend more tightly than PTFE and sustains the same pressure rating. It also has a five-to-one force on tensile strength to PVC and has well passed its heat limit of 167°F. The installers should not use any kinks since, under a cyclic flex, micro-cracks spread and result in pinhole leaks.
Tubing Up for the Challenge
Pressure is implacable, but tubing may be prepared. By selecting materials that disregard heat, chemicals, and UV, the system has an extended lifetime.
Leaks contract, downtime evaporates, and maintenance budgets exhale. Decisions made here minimize energy consumption as the pumps work at a lower differential pressure. A minor choice during design alters all subsequent runs.