If you could cut steel, stone, and composites without heat, smoke, or waste—wouldn’t you? That’s exactly the promise of waterjet technology. As industries chase cleaner, leaner ways to shape the world, waterjet cutting is stepping into the spotlight as a sustainable alternative. More manufacturers are now turning to quality waterjet cutters from TECHNI Waterjet to meet both precision and sustainability goals.
Driven by rising environmental regulations, pressure to reduce emissions, and a growing market for greener products, manufacturers are seeking out fabrication methods that tread lightly. Waterjet cutting is proving to be not just precise—but surprisingly planet-friendly.
What is waterjet cutting and how does it work?
Waterjet cutting is a cold-cutting process that uses a high-pressure stream of water—sometimes mixed with abrasive particles—to slice through materials without heat or mechanical stress. It’s valued for precision, versatility, and environmental safety.
There are two primary types:
- Pure waterjet cutting, ideal for soft materials like foam or rubber.
- Abrasive waterjet cutting, used for hard materials such as metal, stone, and glass.
Here’s how the process unfolds:
- Pressurizing water
Water is pressurized up to 90,000 psi using a high-performance pump. - Adding abrasives (if applicable)
For tougher materials, garnet or similar abrasives are mixed into the water stream. - Focusing through the nozzle
A precision nozzle shapes and directs the cutting jet at the target. - Cutting the material
The focused jet slices through material with minimal heat or stress. - Waste and drainage management
Spent water and abrasives are collected, filtered, and in many cases, recycled.
Why is waterjet cutting considered a sustainable technology?
Unlike traditional thermal or mechanical methods, waterjet cutting minimizes environmental impact. There’s no heat, smoke, or deformation—just clean, accurate cuts.
Its key sustainability benefits include:
- No heat-affected zones
Eliminates thermal distortion and material fatigue. - Minimal material waste
Precise cuts reduce offcuts and scrap rates. - Recyclable water
Most systems use closed-loop filtration to reuse water. - No hazardous fumes
Cuts without releasing toxic emissions into the environment. - Versatile material compatibility
Reduces the need for multiple specialized cutting systems.
What materials can be cut using waterjet technology?
A waterjet cutter is effective on a wide range of materials. It accommodates differences in hardness, density, and thermal sensitivity—all without introducing contamination.
Metals (Aluminum, Steel, Titanium, etc.)
- Aluminum – Lightweight, soft, recyclable
- Stainless Steel – Dense, corrosion-resistant
- Titanium – Strong, low weight-to-strength ratio
- All exhibit minimal burring post-cut and retain mechanical properties.
Composites
- Carbon fiber, Kevlar, and GFRP
- No delamination
Excellent for aerospace applications
- Avoids resin burn-off
- No delamination
Ceramics
- High-hardness materials like zirconia and alumina
- No cracking from thermal shock
- Ideal for medical and electronics uses
- No cracking from thermal shock
Plastics
- Polycarbonate, PVC, HDPE
- No melting or toxic fume release
- Clean edges reduce post-processing
- No melting or toxic fume release
Glass
- Float glass, borosilicate, laminated varieties
- Sharp cuts without edge chipping
- Not suitable for tempered glass
- Sharp cuts without edge chipping
Stone and Marble
- Granite, slate, marble
- No dust emission
- Maintains natural patterns and veining
- No dust emission
Recycled and eco-materials
- Recycled composites, eco-foams, reused sheet metals
- Enables reuse in circular production loops
- Supports zero-waste goals
- Enables reuse in circular production loops
What are the different types of waterjet cutting?
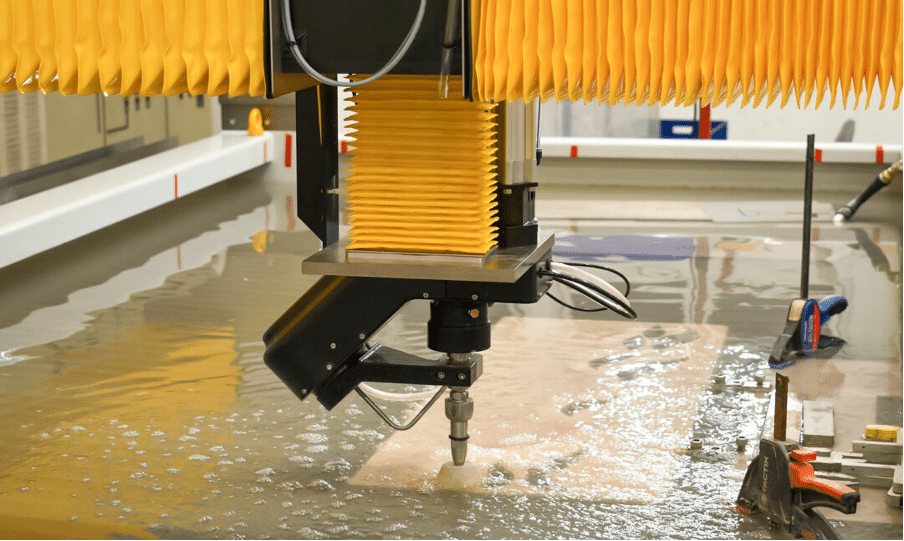
Different materials and tolerances call for different waterjet techniques.
Pure waterjet cutting
- Best for: Soft materials like foam, rubber, cardboard
- Pros: No abrasives needed, low cost, minimal wear
- Cons: Limited to non-metallic, soft materials
Abrasive waterjet cutting
- Best for: Metals, stone, glass, and composites
- Pros: Cuts nearly anything, excellent precision
- Cons: Requires abrasive disposal, higher operating cost
Micro waterjet cutting
- Best for: Electronics, micro-mechanics
- Pros: Ultra-fine nozzles for tiny components
- Cons: Expensive setup, slow cutting speed
What are the main components of a waterjet cutting system?
- High-pressure pump
- Cutting head and nozzle
- Catcher tank
- Abrasive hopper
- CNC control unit
- Water filtration system
These parts work together to deliver precision and sustainability in every cut.
How precise is waterjet cutting?
Waterjet systems offer exceptional accuracy, making them suitable for both prototyping and production work.
- Kerf width: 0.04″ to 0.05″ (1.0 to 1.27 mm)
- Dimensional tolerance: ±0.003″ to ±0.005″ (0.076 to 0.127 mm)
- Surface roughness: Ra 3.2–25 μm, depending on feed rate and material
How sustainable is the waterjet cutting process?
From water use to power consumption, waterjet systems are engineered for efficiency.
- Closed-loop water systems
Recycle over 90% of used water. - Garnet recycling or disposal best practices
Spent garnet can be repurposed in construction or properly landfilled. - No toxic gas emissions
No combustion or melting means no airborne toxins. - Low energy per cut for thin materials
Especially compared to thermal methods.
What industries use waterjet cutting for sustainable fabrication?
- Aerospace – Composite trimming without fiber burn
- Architecture – Cutting stone without silica dust
- Automotive – Prototypes with no heat warping
- Electronics – PCB slotting without delamination
- Green construction – Tiles and flooring from recycled stone
What are the key benefits of using waterjet cutting?
Waterjet cutting brings several clear advantages, especially when sustainability is a priority.
- Cold cutting = no thermal distortion
- Works on virtually any material
- High precision
- No secondary finishing required
- Eco-friendly process
- Reduced kerf and waste
- Excellent for prototyping
How do waterjet and laser cutting compare?
Each technology has its place, but waterjet stands out in several green aspects.
- Material compatibility – Waterjet cuts more types, including composites
- Heat impact – Waterjet is cold; laser introduces heat
- Cutting speed – Laser cutting is faster on thin metals
- Accuracy – Both can be extremely precise
- Environmental footprint – Waterjet produces no fumes
- Maintenance requirements – Laser optics need frequent alignment; waterjet parts wear with use
What are the most important setup and operational parameters?
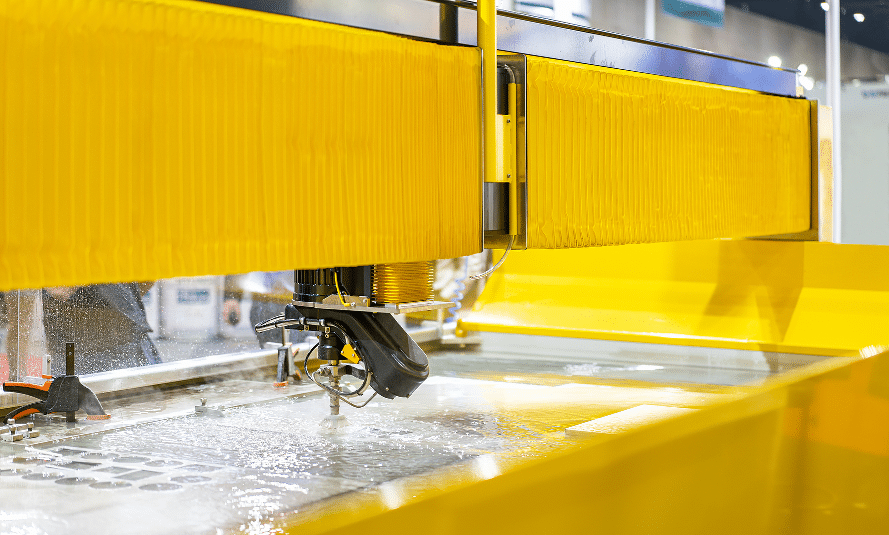
Performance and efficiency depend on proper settings.
- Water pressure (40,000–90,000 psi)
- Nozzle size
- Cutting speed
- Type and flow of abrasive
- Stand-off distance
How much water does waterjet cutting use—and is it recycled?
Waterjet systems can consume 0.5 to 1.5 gallons per minute, depending on pressure and nozzle size. However, modern systems use closed-loop recycling to minimize waste.
- Usage per hour – ~30 to 90 gallons per cutting head
- Recirculation options – In-house water recycling units
- Filtration types – Multi-stage filters, sediment separators, and reverse osmosis
How is waterjet technology evolving to support greener manufacturing?
Modern advances are pushing the boundaries of sustainable cutting.
- Reduced power consumption – Through energy-efficient pumps
- Eco-abrasives – Less mining impact and recyclable materials
- Smart optimization algorithms – Reduce cutting time and waste
- Integration with renewable energy sources – Solar-powered shops and hybrid systems
What are the alternative cutting technologies—and how eco-friendly are they?
While viable for some use cases, alternatives often fall short in sustainability.
- Laser cutting – Fast but energy-intensive
- Plasma cutting – Quick yet produces harmful gases
- Mechanical saws – Create noise, dust, and material loss
- EDM – Slow, with electrical discharge waste
- Knife cutting – Limited to soft or thin materials
Conclusion
Waterjet cutting has quietly become a cornerstone of sustainable fabrication. By eliminating thermal damage, reducing waste, and supporting closed-loop resource use, it offers a rare blend of precision and environmental responsibility.
As sustainability shifts from buzzword to baseline, engineers and manufacturers alike should keep their eyes—and their clean cuts—on waterjet technology.