Introduction
In the fast-paced world of engineering, the demand for rapid prototyping and production is higher than ever. While high-speed PLA has been widely recognized for quick and easy printing, the development of high-speed PETG has emerged as a game-changer for engineers seeking both speed and strength in their parts. Bambulab and Kingroon launched high-speed PETG in August this year, followed by more brands releasing high-speed PETG. This article dives into the unique benefits of high-speed PETG, the best practices for successful prints, and its transformative impact on engineering.
Overview of PETG in 3D Printing
PETG, or Polyethylene Terephthalate Glycol, is known for its durability, flexibility, and chemical resistance, making it an excellent choice for engineering applications. Traditionally, PETG has been slower to print than PLA, but with advancements in high-speed PETG formulations, engineers can now produce functional parts at a faster rate without compromising on quality or durability.
Importance of Speed in Engineering Parts Production
Speed is critical in engineering, where the ability to quickly prototype and iterate can make or break project timelines. With high-speed PETG, engineers no longer need to choose between speed and material performance, paving the way for streamlined workflows and faster time-to-market.
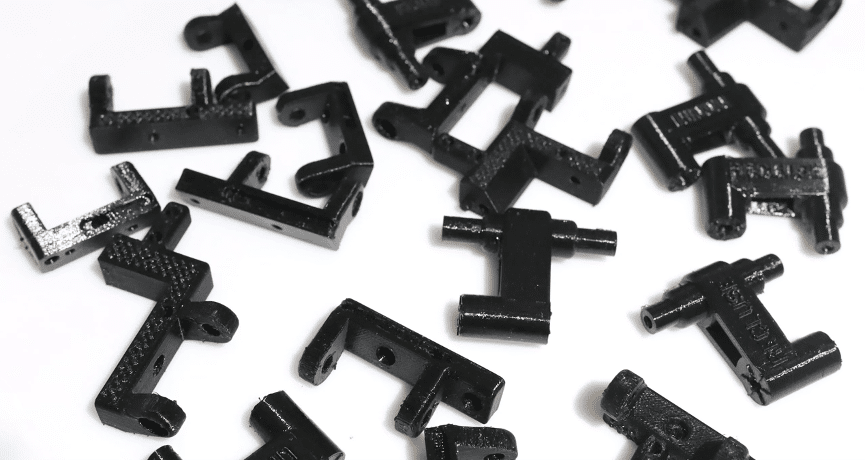
Understanding PETG
Properties and Benefits of PETG
PETG has a balanced set of properties that include flexibility, toughness, and chemical resistance, making it suitable for functional parts that need to withstand stress, impact, or exposure to harsh environments. This filament can handle more rigorous applications compared to PLA while being easier to work with than ABS.
Comparison with Other Filaments
In comparison to standard PLA, PETG is more durable and less brittle, though it can be prone to stringing and oozing during the print process. Unlike ABS, PETG doesn’t require a heated chamber, making it more accessible for desktop printers while still delivering high-quality mechanical properties.
Advancements in High-Speed PETG
Recent Innovations and Technologies
Recent innovations in PETG formulations have led to the introduction of high-speed PETG filaments that retain the durability and flexibility of traditional PETG but are optimized for faster print speeds. This improvement meets the demand for rapid production in engineering while maintaining the filament’s structural integrity.
How High-Speed PETG Differs from Standard PETG
High-speed PETG is designed with lower viscosity and optimized melt flow characteristics, allowing for quicker extrusion without increased warping or stringing. This upgrade reduces print time while still yielding strong, durable parts, bridging the gap between conventional PETG and high-speed PLA.
Benefits for Engineering Parts
Increased Efficiency in Prototyping and Production
High-speed PETG enables faster production cycles, which is ideal for engineering projects that require frequent prototyping. Engineers can now test and refine their designs more efficiently, reducing the time needed to bring a product to market.
Enhanced Strength and Durability for Functional Parts
Engineering parts require a balance between strength and flexibility. High-speed PETG’s durability makes it suitable for load-bearing parts and functional components that endure regular use, positioning it as a reliable option for long-term applications.
Best Practices for Printing
Optimal Printer Settings and Techniques
To get the best results with high-speed PETG, it’s essential to fine-tune retraction settings to minimize stringing, a common challenge with PETG. A higher retraction speed and distance, combined with a print speed of around 80–100mm/s, usually yield optimal results.
Tips for Achieving High-Quality Results
Using a heated bed (around 70–80°C) and a cooling fan can improve adhesion and reduce warping. Adjusting print speed and extrusion temperature (230–250°C) is also key to reducing issues like stringing and ensuring smooth, quality finishes on complex geometries.
Case Studies
Examples of Successful Engineering Projects Using High-Speed PETG
High-speed PETG has been used in various engineering fields for projects that require quick prototyping with reliable material properties. For instance, automotive engineers have utilized high-speed PETG to produce custom jigs and fixtures rapidly, while electronic component designers have found success in creating durable casings for prototype devices.
Feedback from Engineers and Designers
Engineers report that high-speed PETG’s balance of speed and performance has significantly reduced their prototyping cycles. Many note the enhanced reliability for functional parts, citing PETG’s impact resistance and flexibility as standout features compared to other high-speed filaments.
Challenges and Considerations
Potential Limitations and How to Address Them
Despite its benefits, high-speed PETG can still present challenges, such as stringing and ooze. Engineers can mitigate these by carefully adjusting retraction settings and using well-maintained nozzles. However, in extreme cases, slower speeds may still be necessary to achieve certain fine details.
Cost and Accessibility Factors
High-speed PETG is generally more expensive than standard PETG or PLA, which may impact its accessibility for some users. However, its enhanced efficiency and reliability in production often offset the higher cost in professional engineering environments.
Future of High-Speed PETG
Emerging Trends and Potential Developments
As 3D printing technology continues to advance, we can expect further innovations in PETG formulations tailored for even higher speeds and better print quality. Machine learning and AI-assisted print settings may also contribute to refining high-speed PETG use in complex engineering applications.
Impact on the Engineering and Manufacturing Industries
The adoption of high-speed PETG is set to transform engineering and manufacturing, offering an efficient alternative to traditional methods and materials. As accessibility improves, high-speed PETG has the potential to become a standard in rapid prototyping and low-volume production.
Conclusion
High-speed PETG combines the durability of standard PETG with faster print capabilities, making it ideal for engineering parts. From rapid prototyping to durable, functional components, this material is redefining the capabilities of 3D printing in engineering.
As more engineers adopt high-speed PETG, the impact on prototyping and production timelines will be profound. This filament is a powerful tool in the 3D printing world, promising new possibilities in engineering and manufacturing.