Modern factories fight the same battle every day: how to make high-quality parts faster, at lower cost, and with fewer headaches. CNC precision custom machining is one of the simplest ways to win that fight. By turning digital designs into metal or plastic parts with micrometer accuracy, it gives production managers more control, more flexibility, and more peace of mind than traditional methods ever could.
Understanding CNC Precision Custom Machining
When it come to machine something, there are lots of methods to choose from. But when it comes to “custom precision machining”, CNC machining maybe the first choice in many people’s mind. What do “CNC” stand for? CNC machining means Computer Numerical Control Machining. Due to the smart computer control, the machining process goes in a precision way.
What “Precision” Really Means
CNC machines move along 3-, 4-, or even 5- axis while powerful controllers check position thousands of times per second. This tight loop keeps every cut within a tiny tolerance band—often ±0.005 mm. When each part matches the CAD model so closely, assembly time drops and downstream rework almost disappears.
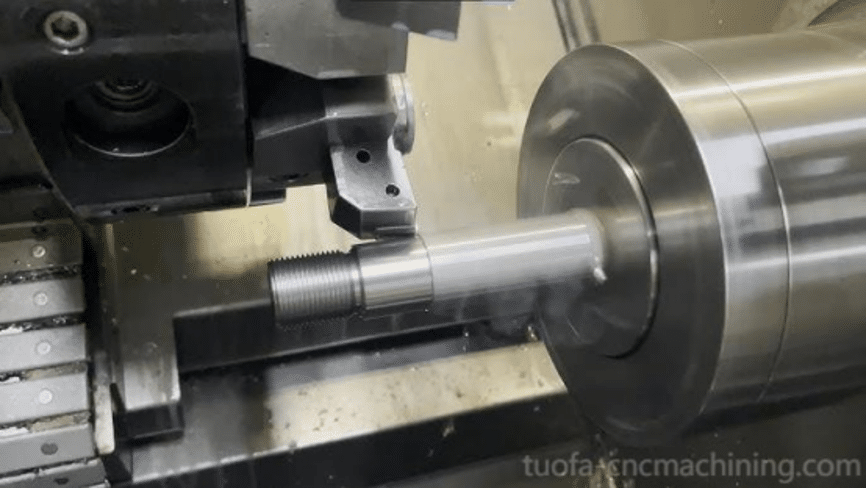
Digital Workflows Drive Accuracy
A single digital thread links design, simulation, tool-path generation, and final inspection. Engineers design the part in CAD, translate it into CAM tool paths, and send this code straight to the machine. Because no manual templates or jigs intervene, the risk of human error stays low.
From Prototype to Mass Production
You can cut one test piece in the morning and a thousand production parts by nightfall on the same machine. That flexibility shortens development loops and lets you validate design tweaks in real time.
Key Benefits for Your Production Line
Everyone wants stable. That’s why more and more people choose CNC machining for own projects. For many companies that want to create their own branded products, CNC custom precision machining is a better choice.
1. Consistent Quality – Every part meets the print, so downstream fixtures fit and field failures fall.
2. Shorter Cycle Times – High spindle speeds, rapid tool changes, and automated pallet loaders keep chips flying around the clock.
3. Lower Scrap Rates – Tight tolerances mean fewer rejects and less wasted material.
4. Design Freedom – Complex curves, pockets, and threads are routine, not special-process headaches.
5. Scalable Volumes – Run five parts today, five thousand next month, without fresh tooling.
6. Easier Traceability – Machines log every run, making audits and root-cause checks simple.
Investing in custom metal machining amplifies each of these wins because the service tailors tools, work-holding, and process parameters to your exact material and geometry. That personal fit drives even tighter tolerances and smoother finishes than generic job-shop programs can achieve.
Custom Lathe Work: Turning Ideas into Round Realities
Rotational parts—shafts, bushings, valves—live at the heart of almost every mechanical system. High-speed turning centers combine live tooling, sub-spindles, and bar feeders to finish these parts in a single setup. With custom lathe work you can:
l Hold roundness within a few microns for low-vibration assemblies.
l Cut complex features such as grooves, undercuts, and internal threads without extra milling steps.
l Swap between aluminum, stainless, or exotic alloys by dialing in custom speeds and feeds.
l Automate deburring and part-off to reduce manual handling and injury risk.
Because the lathe script comes directly from your CAD file, changeovers need little more than a tool-offset tweak. That lets maintenance teams order small batches on demand instead of stockpiling spares that may never leave the shelf.
Integrating CNC Precision Services into Your Workflow
1. Review the Design for Machining
l Keep wall thickness uniform.
l Add fillets to sharp internal corners.
l Avoid unnecessarily tight tolerances.
l Small tweaks here can slash cycle times by 30 % or more.
2. Choose the Right Material Early
l Match strength and corrosion needs to an alloy that the shop machines often.
l Ask your vendor for heat-treat options to reach final hardness in-house.
3. Partner With an Experienced Vendor
l Tour their facility or request a video audit.
l Confirm they own metrology gear—CMMs, optical comparators—that can verify the promised tolerance.
4. Run a Pilot Batch
l Test fit, function, and surface finish in your own line.
l Feedback at this stage costs pennies; redesigns after launch cost thousands.
5. Lock Down Quality Control Plans
l Define sampling frequency, traceability tags, and packaging rules.
l Share them in writing so both teams follow one playbook.
6. Scale Confidently
Once the pilot passes, lift the order volume without changing programs or fixtures. The same code will run predictably week after week.
Practical Tips for Maximizing ROI
l Bundle Parts by Material – Running all 6061 aluminum parts in one slot reduces tool changes and setup cost.
l Standardize Hole Sizes – Using the same drill diameters across families lets the shop reuse cutters and speeds up quoting.
l Design for Fixturing – Add shallow flats or pickup points to odd-shaped castings so the shop clamps them in a single pass.
l Share Forecasts – Even informal volume projections help your partner plan raw-stock inventory and pre-stage fixtures.
l Track Cost per Good Part, Not per Hour – Cheap hourly rates mean nothing if scrap runs high.
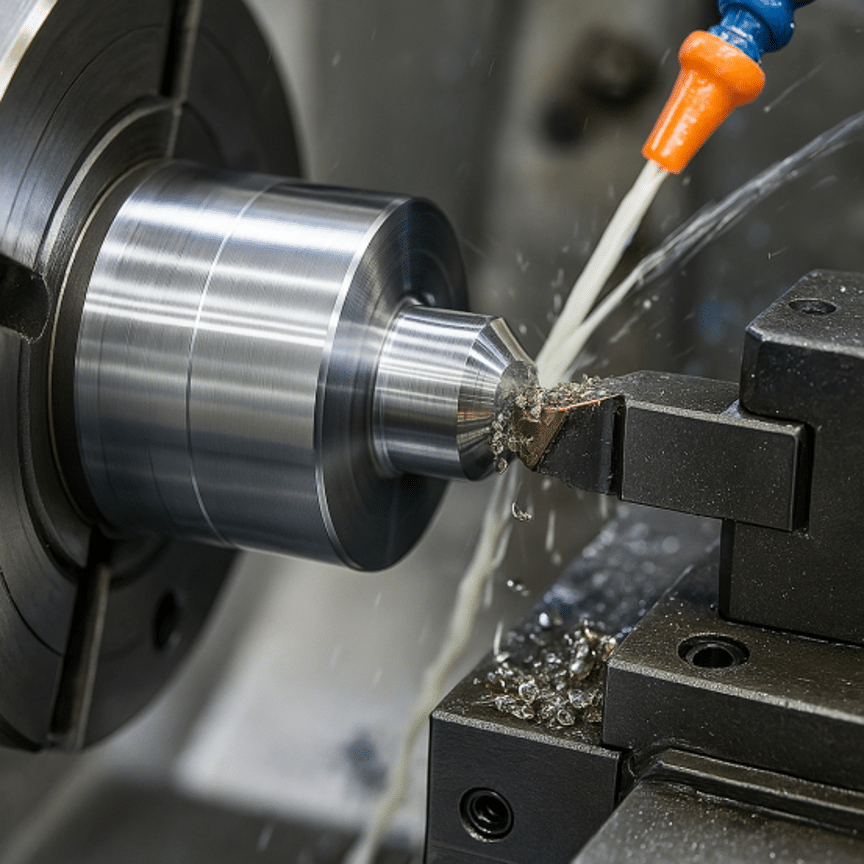
Come to TUOFA CNC Machining for Your Custom Projects
Whether it is five-axis machining or milling machining, TUOFA CNC Machining has rich machining experience. TUOFA has rich industry experience – nearly 20 years – and can process hard metals, such as titanium alloys, as well as soft metals, etc.; from CAD to production, TUOFA can provide one-stop overall service support.
Material Class | Representative Grades | Typical Tolerance | Core Processes | Common Finishes |
Hard Metals | Ti-6Al-4V, Inconel 718, 17-4 PH,etc. | ± 0.005 mm | 5-axis milling, mill-turn, wire EDM, grinding | Passivation, TiN coating, micro-blasting |
Stainless Steels | 304/304L, 316/316L, 420,etc. | ± 0.008 mm | 3- & 5-axis milling, CNC turning, deep-hole drilling | Electropolish, bead-blast, black oxide |
Aluminum Alloys | 6061-T6, 7075-T6, 5083,etc. | ± 0.01 mm | High-speed milling, 4th-axis rotary, tapping | Clear/black anodize, chem-film, hard-coat |
Copper & Brass | C110, C360, C145,etc. | ± 0.01 mm | Live-tooling turning, 4-axis milling | Bright dip, nickel plate, tin plate |
Engineering Plastics | PEEK, Delrin, PTFE, ABS,etc. | ± 0.02 mm | Vacuum-fixtured milling, low-clamp-force turning | Vapor polish, media tumble, dye coloring |
CNC precision custom machining is more than a buzz phrase. It is a proven path to faster launches, leaner lines, and better products. By leveraging custom lathe work for rotational parts and broader custom metal machining for prismatic shapes, you remove variation, cut downtime, and free your team to innovate. When the right design practices meet the right machining partner, production stops being a bottleneck and starts becoming a competitive weapon.