The prototype development process involves creating physical models that represent the design of a product, allowing teams to evaluate form, fit, function, and potential manufacturing challenges. Speed is a crucial factor in the prototyping stage. The quicker a prototype can be developed, tested, and refined, the sooner a product can reach the market.
CNC turning services have become essential in speeding up prototype development. By leveraging the precision and efficiency of computer-controlled machining, companies can significantly reduce the time required to produce prototypes. CNC turning delivers parts with high dimensional accuracy, minimizing the need for rework. Additionally, the process can accommodate a wide range of materials and complex shapes, further contributing to faster development.
In this article, we’ll explore five ways CNC turning services can speed up your prototype development, ultimately enhancing your product’s chances of success.
Rapid Prototyping Capabilities
One of the primary advantages of CNC turning services is their ability to produce prototype parts quickly. Traditional manufacturing methods, such as manual turning or casting, can be time-consuming and labor-intensive, often requiring multiple steps to create a single part. In contrast, CNC turning automates the process, allowing for the rapid creation of precise components directly from CAD models.
The speed of CNC turning is further enhanced by its ability to operate continuously, with minimal human intervention. This means that once a design is programmed into the CNC machine, the production of prototypes can proceed uninterrupted, leading to significantly shorter lead times compared to traditional methods.
Iterative Design Process
Prototyping is inherently an iterative process. As designs are tested, they often require modifications to improve functionality, address unforeseen issues, or incorporate new features. The ability to quickly iterate on a design is essential for maintaining momentum in the development process.
CNC turning services excel in this area by facilitating rapid design changes. With traditional manufacturing, modifying a prototype can be a cumbersome process, often requiring the creation of new molds or fixtures. CNC turning, however, allows for easy adjustments to the design program, enabling quick production of revised prototypes. This flexibility not only saves time but also reduces costs associated with tooling and setup.
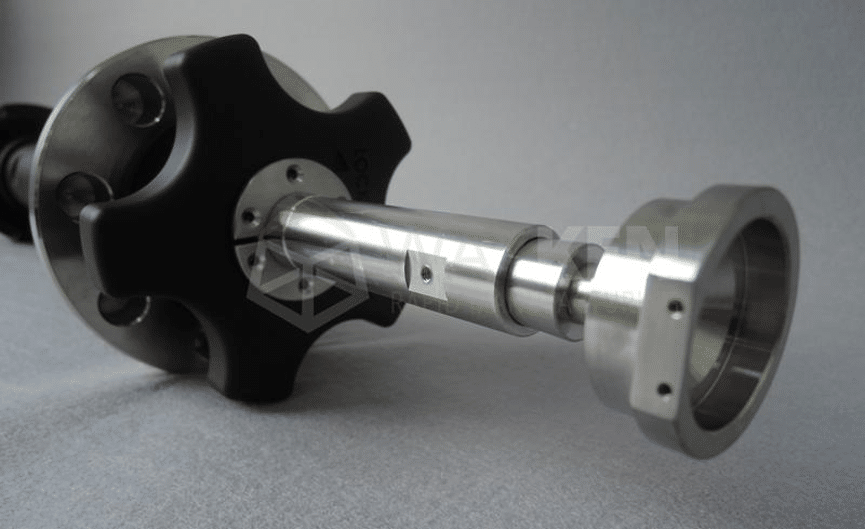
Complex Part Manufacturing
As product designs become more sophisticated, the need for complex, intricate parts in prototypes increases. Traditional manufacturing methods may struggle to produce these parts accurately and efficiently, leading to delays in the prototyping process. CNC turning services, however, are well-equipped to handle complex part manufacturing, thanks to their high precision and versatility.
CNC turning machines can produce parts with intricate geometries, tight tolerances, and fine details, all of which are essential for modern prototypes. This capability not only accelerates the development of complex products but also ensures that the prototypes are accurate representations of the final design. As a result, companies can confidently move forward with their designs, knowing that their prototypes meet the necessary specifications.
Reduced Lead Times
Lead time is a critical factor in product development, especially when it comes to prototyping. The longer it takes to produce a prototype, the longer it takes to validate the design and move on to the next phase of development. CNC turning services help reduce lead times by streamlining the production process.
Several factors contribute to the reduced lead times offered by CNC turning. First, the automation of the machining process eliminates the need for manual intervention, allowing for faster production. Additionally, the precision of CNC turning reduces the likelihood of errors and rework, further speeding up the process. Finally, the ability to produce complex parts in a single setup minimizes the need for additional machining operations, resulting in faster turnaround times for prototypes.
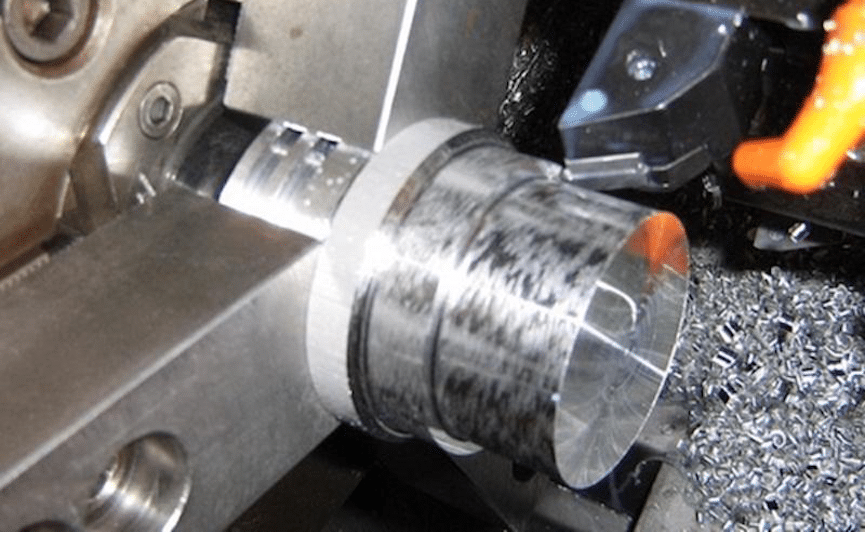
Material Versatility
Prototyping often involves testing different materials to determine which one best suits the final product. The versatility of CNC turning services in accommodating a wide range of materials is a significant advantage in this regard.
Whether the engineering prototype requires metals, plastics, or composite materials, CNC turning can handle the machining process with precision and efficiency.
This material versatility speeds up the prototyping process by allowing for quick material testing and selection. Instead of being limited to a specific material or waiting for specialized tooling, companies can rapidly produce prototypes in various materials, compare their performance, and make informed decisions about the final product. This flexibility not only accelerates the development process but also enhances the quality and durability of the final product.
Conclusion
CNC turning services have revolutionized the prototyping process, offering a range of benefits that contribute to faster and more efficient product development. From rapid prototyping capabilities to reduced lead times, the advantages of CNC turning are clear. By enabling quick design iterations, handling complex part manufacturing, and accommodating a wide variety of materials, CNC turning services accelerate prototype development and help companies bring their products to market faster.