Polymer additives are substances added to plastics to make them perform better. These additives can change polymer strength, flexibility, anti-dripping properties, etc. Home appliances benefit greatly from these improvements. This article explores how polymer additives make home appliances safer and more durable.
Plastics Use in Home Appliances
Modern appliances contain plastics everywhere, from casings and insulation to internal components and electrical wiring. These plastics should have properties such as:
1. Anti-dripping Property
Appliance plastics need good Flame retardant property. This describes how plastics behave in the event of electric shorts. Regular plastics might melt under excessive heat and form burning drops. These drops can spread fire throughout the house. Anti-dripping plastics improved via polymer additives stay in place when heated. This meets important safety standards.
2. Impact Performance
Appliances might face bumps and knocks. For instance, vacuums might hit furniture. Blenders could fall off the counter. Good impact performance means the surface plastics won’t crack or break easily and the internal components will stay protected. This extends appliances’ lifespan.
3. Durability
Home appliances should last for years. Quality plastics help achieve this goal. They withstand regular use and can face heat, cold, and moisture daily. Durable plastics don’t fade or become brittle. They keep their shape and function over time.
Common Plastics Used in Home Appliances
There are different types of plastics used in home appliances. Common types include:
1. PC
Polycarbonate (PC) works great for appliance housings. It offers excellent clarity and strength. PC handles temperatures well. Food processors and water kettles often use it. But PC is generally susceptible to scratches.
2. PBT
Polybutylene terephthalate (PBT) excels in electrical parts. PBT resists chemicals effectively. It is often used in switch housings and connectors. However, PBT might degrade when exposed to moisture for extended periods and shows reduced strength when subjected to stress concentrations.
3. PP
Polypropylene (PP) is used in washing machines and refrigerators. PP resists most household chemicals and doesn’t react with food or detergents. Manufacturers use this type of plastic for large components. However, it is liable to chain degradation from exposure to temperatures above 100 °C.
The Significant Role of Polymer Additives
Basic, unmodified plastics often don’t perform well enough. They might burn easily and could break on impact. Polymer additive can enhance their performances. Manufacturers can supply safer and more reliable appliances. The following aspects highlight the significance of polymer additives:
1. Anti-dripping Agent
An anti-dripping agent prevents plastic from forming flammable drops. SN3307PF is an excellent example. Manufactured by the trusted polymer additive manufacturing brand Shine Polymer, it contains encapsulated PTFE. It helps products meet UL 94 safety standards. The key features of this polymer additive include:
- Free-flowing white to off-white granular form
- Excellent dispersion in various thermoplastics
- Enhances anti-dripping properties to meet UL 94 V0 and V1 standards
- Not easily agglomerated at room temperature
- Applicable to PC, PS, ABS, PBT, PPO and their alloys
- Creates smooth surfaces with fewer gels and knitlines
2. Impact Modifier
These polymer additives help plastic absorb energy better. LP2082 from Shine Polymer is a popular acrylic impact modifier. It has a special core-shell structure that distributes impact forces effectively. LP2082 works well in PC and PBT plastics. Its top characteristics include:
- Free-flow white powder form
- Crosslinked silicone and poly(butyl acrylate) core
- Grafted poly-methyl methacrylate shell
- High-impact modification capabilities
- Maintains excellent colorability
- Well-suited for PC, PBT, and PC blends
- Enhances durability in electrical/electronic components
- Extends the lifespan of appliance parts
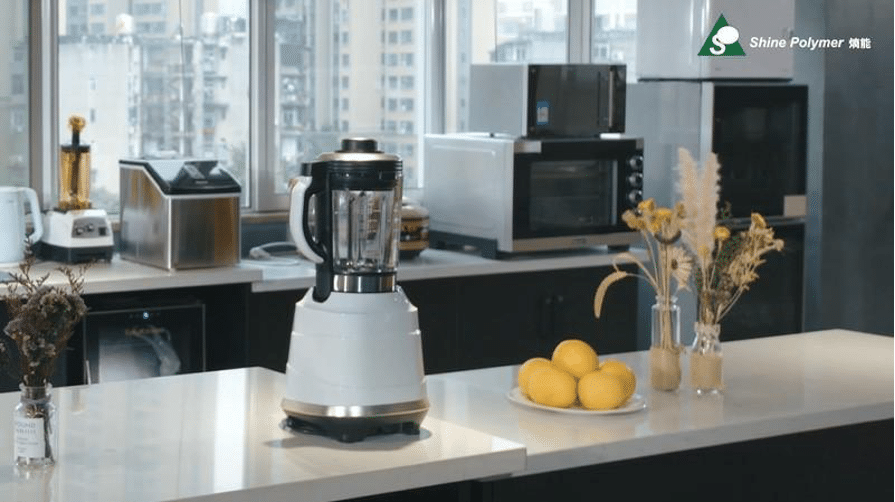
Conclusion
Polymer additives transform ordinary plastics into superior materials. Anti-dripping agents enhance fire safety significantly, while impact modifiers improve impact resistance for longer life.
The reputed brand Shine Polymer offers trusted solutions in this field. With over two decades of experience, the manufacturer provides high-quality polymer additive products. Their products meet international standards. Visit the company’s website to explore its polymer additives.