Understand Your Project Requirements
Selecting the right industrial equipment begins with a comprehensive understanding of your project’s unique demands. Every worksite operates under specific circumstances, from extreme weather conditions and uneven terrain to rigorous time constraints and material specifications. Accurately defining these needs is essential, as misjudgments at this stage can lead to equipment mismatches that compromise efficiency, increase costs, and risk safety lapses. Begin by assessing your project’s primary objectives, the scope of daily tasks, and the materials you will be handling. Factors in the operational environment include climate, typical worksite hazards, and the duration of operation.
For projects in North Carolina’s industrial sector, for example, procurement teams often rely on the expertise of industrial suppliers in North Carolina who bring valuable local knowledge. They understand regional regulatory standards, are familiar with common challenges like humidity or temperature swings, and have insights into the most durable equipment for such settings. Local suppliers not only recommend equipment that meets industry benchmarks but also offer solutions tailored to your project’s particular requirements. This targeted approach ensures long-lasting, compliant, and efficient equipment deployment from the outset.
Evaluate Equipment Durability and Build Quality
Durability stands as a cornerstone for any industrial equipment purchase, especially for demanding jobsites where frequent breakdowns can derail timelines and inflate project costs. When evaluating machinery, prioritize those constructed from high-grade materials such as reinforced steel or engineered specialty alloys proven to withstand severe wear and tear. Investigate not just the visible structure, but also the internal components, welding quality, and the robustness of joints and fasteners.
Leading manufacturers back their equipment with certifications and compliance with industry-recognized quality standards, which can serve as indicators of toughness. Additionally, machines that feature advanced protective coatings can resist erosion, corrosion, and exposure to harsh chemicals, which are critical for worksites susceptible to weather extremes or abrasive materials. With recent advances in design, machinery now offers ergonomic improvements that protect both workers and the equipment itself, maintaining consistent productivity and reducing long-term repair needs.
Consider Equipment Versatility
Modern worksites rarely operate with a single type of task day in and day out. That’s why equipment versatility is so valuable—it allows construction, manufacturing, or processing teams to adapt quickly to shifting priorities without the need for constant reconfigurations or additional purchases. Invest in multi-functional machines like skid steer loaders, excavators with interchangeable attachments, or backhoe loaders capable of tackling all kinds of roles, from trenching and earthmoving to lifting heavy loads and clearing debris.
The actual versatility of a machine comes down to its compatibility with a broad range of attachments and its proven track record in the field. Explore not only the manufacturer’s list of compatible accessories but also real-world case studies and operator testimonials. Versatile equipment minimizes costly downtime, maximizes machine utilization, and helps manage dynamic project schedules. The ability to quickly adapt a machine to a new task also provides valuable risk mitigation should project requirements evolve unexpectedly, helping maintain productivity even amid rapidly changing conditions.
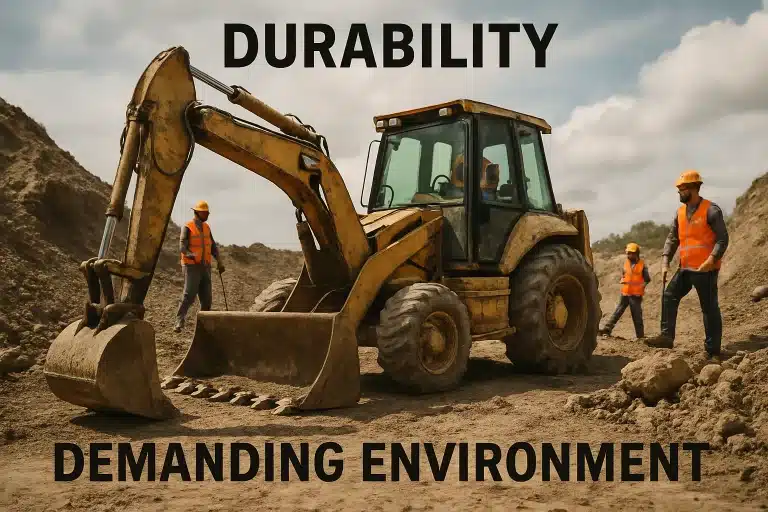
Assess Maintenance Requirements and Support
Even the most rugged equipment requires consistent care to remain reliable and to extend its service life. When comparing potential investments, pay close attention to design features that simplify ongoing maintenance. Favor equipment models with easy-access panels, built-in diagnostic systems, and modular parts—these enhancements allow for quicker, more efficient checkups and repairs, minimizing costly downtime and labor demands. Consider the availability and pricing of consumables like filters, belts, or lubricants, all of which directly influence the long-term upkeep budget.
Equally important is the reputation and accessibility of the manufacturer’s or distributor’s support network. Exceptional after-sales support, comprehensive warranties, and guaranteed rapid access to spare parts can make all the difference in emergencies. Opt for manufacturers known for robust service infrastructure in your region, transparent technical support, and established protocols for on-site repairs.
Prioritize Safety Features
Safety cannot be compromised in any industrial environment, particularly where heavy-duty machinery is involved. Prioritizing equipment outfitted with robust safety features—such as emergency stop systems, operator protection guards, audible and visual warning alarms, and ergonomically designed controls—is crucial for safeguarding crew members. Well-designed safety mechanisms also help equipment operators respond rapidly to unforeseen dangers, reducing the risk of injury or costly accidents that can halt operations.
Beyond physical safeguards, ensure that every machine complies with both local and national safety regulations and comes with documentation proving such compliance. Seek out equipment providers that offer additional resources, like operator training programs or formal safety certifications, ensuring your team maintains up-to-date best practices. Understanding and embracing the latest safety technologies and protocols not only protects workers but minimizes liability for your business.
Consider Total Cost of Ownership
It’s easy to focus on sticker price when outfitting your jobsite with new equipment, but the true value lies in understanding the total cost of ownership (TCO). TCO encompasses not only the upfront purchase price, but also ongoing operating expenses—routine maintenance, energy consumption, cost of replacement parts, labor for repairs, downtime, and eventual equipment disposal. Machines with a higher initial price tag may prove more cost-effective over time due to improved reliability, greater energy efficiency, or superior resale value.
To make the most informed investment, conduct a thorough cost-benefit analysis that examines projected maintenance frequencies, average lifespan, downtime risks, and warranty coverage. By weighing these factors, you can identify equipment that consistently performs under pressure and generates long-term value. Consider consulting with vendors who can provide operational efficiency data, customer references, and detailed warranty terms so you can maximize both financial performance and productivity.
Conclusion
Choosing the most durable and appropriate industrial equipment for challenging worksite conditions isn’t just about making a purchase—it’s a strategic decision that impacts every aspect of your operation, from productivity and safety to profitability and legal compliance. By thoroughly analyzing your project requirements, prioritizing durability and safety, seeking out equipment with genuine versatility, planning for a strong maintenance partnership, and calculating the total cost of ownership, you ensure your investments withstand the rigors of your industry and return the highest value.
Building strong partnerships with established industrial suppliers will streamline your search for high-quality machinery and offer peace of mind with locally tailored support. Remember: strategic equipment decisions made today lay the groundwork for tomorrow’s efficient, safe, and profitable worksites. Set your standards high, consult with trustworthy experts, and always stay proactive in your approach to industrial procurement.