CNC machining has been transforming the manufacturing industry by providing unparalleled precision in the production of complex parts. According to recent data, the global CNC machining market is expected to reach $80.4 billion by 2028[1], reflecting its growing importance across various sectors. The precision and repeatability offered by CNC machining have made it indispensable in industries such as aerospace, automotive, and medical devices.
Choosing the proper CNC machining manufacturer is crucial to achieving the desired quality and performance of your final product. A reliable CNC machining manufacturer not only provides high-quality components but also ensures timely delivery and cost-effective solutions. This initial decision significantly impacts the overall success of your production process, making it essential to choose a CNC manufacturing collaborator who can meet your specific requirements for CNC manufacturing.
In today’s article, we will explore the factors to choose the best CNC machining manufacturer in this vast market to fit your CNC machining demands.
CNC Machining Process: How to Ensure High-Quality and Reliable Production
To ensure precision in CNC machining, it is essential to follow a structured procedure. Here are the key steps involved:
1. Design Validation
Before any metal hits the machine, it’s crucial to validate the design. This step ensures the design is optimized for CNC machining, with considerations for manufacturability, material choice, and geometry. Using software tools for simulation can help predict potential issues before production begins, saving both time and resources.
2. Material Inspection
The foundation of a high-quality CNC machined part lies in the quality of the material used. Inspecting materials upon receipt for consistency and properties such as tensile strength, hardness, and corrosion resistance ensures that the final production will perform as expected under operational stresses.
Common materials used in CNC machining factories include various metals (such as aluminum and titanium) and plastics (such as ABS, PEEK, and polycarbonate).
3. Machining Parameters Optimization
Setting and optimizing machining parameters is critical for balancing efficiency and quality. Parameters such as depth of cut need, cutting speed, etc. to be adjusted based on the material and the specific part design. Advanced software can assist in optimizing these parameters to reduce wear on tools and prevent material waste.
4. CNC Operational Program Validation
Before production, the CNC operational program must be thoroughly checked to prevent errors. This includes verifying tool paths and ensuring that the sequence of operations is correct.
5. First Piece Inspection
The first piece inspection acts as a prototype for subsequent production. This crucial step involves checking the first machined part against the design specifications. Any discrepancies found here can lead to adjustments in the CNC program or machining parameters.
6. Periodic and Final Inspections
Quality control doesn’t end after the first piece. Periodic inspections throughout the manufacturing process help ensure that each batch maintains the same high standards. A final inspection of completed parts is essential for verifying dimensions, surface finish, and functionality.
7. Surface Quality Check
Assessing the surface quality of finished parts is vital for applications where aesthetic appearance or surface texture impacts functionality. Techniques such as visual inspection, tactile probes, or laser scanning can detect imperfections like burrs, scratches, or uneven finishes.
8. Record Keeping for Traceability
Maintaining detailed records throughout the CNC machining production process supports traceability and quality control. Documentation should include details about material batches, machine parameters, inspection results, and corrective actions. This data is invaluable for continuous improvement and in case of any need for recalls or audits.
The Choice of a Great CNC Machining Manufacturer: What You Should Consider
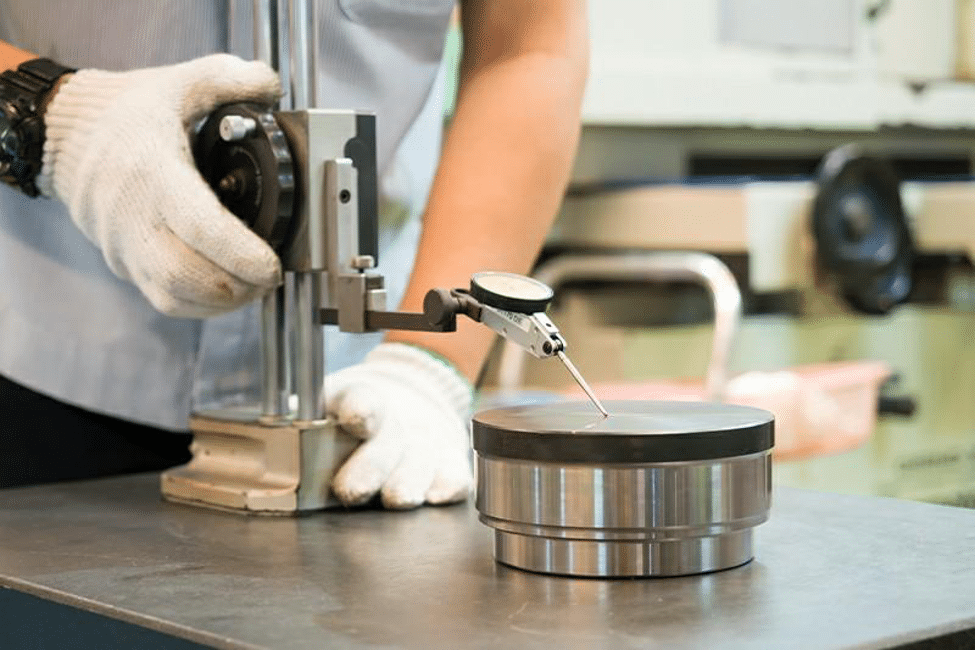
To achieve production followed by a strict working process just like the one mentioned above, your choice of a CNC machining manufacturer is a must. Several critical factors can significantly impact your decision. Evaluating these aspects ensures you select a partner capable of delivering your specific needs consistently.
1. Certificates
Certification is a key indicator of a manufacturer’s commitment to quality and industry standards. Look for manufacturers with the following certifications:
- ISO 9001: Ensures the manufacturer adheres to quality management principles
- ISO 13485: Relevant for medical device manufacturing, guaranteeing compliance with regulatory requirements
- AS 9100: Essential for aerospace industry standards, ensuring safety and reliability
These certifications demonstrate that the manufacturer follows stringent quality control processes and maintains high standards in production.
2. Innovative Tools and Machines Used in CNC Machining
The tools and machines used by a CNC machining manufacturer play a crucial role in determining the quality of the final product. Consider manufacturers that:
- Utilize advanced CNC machines, such as 3-axis, 4-axis, and 5-axis machining centers
- Upgrade their equipment to incorporate the latest technology
- Implement state-of-the-art CAM software for precise programming and tool path generation
Modern and well-maintained machinery ensures higher precision, better surface finish, and overall superior quality of machined parts.
3. Options for Customization
Flexibility in customization is vital for meeting unique project requirements. A good CNC machining manufacturer should offer:
- Various material options, including metals and plastics
- Customizable tolerances and surface finishes to meet specific design criteria
- Tailored solutions for both rapid prototyping and low-volume production
The ability to customize ensures that the manufacturer can accommodate various project specifications and deliver parts that meet your exact needs.
4. Reputation in the Market
The reputation of a CNC machining manufacturer is a strong indicator of their reliability and quality. To assess a manufacturer’s reputation:
- Check customer reviews and testimonials
- Look for case studies or examples of previous work
- Consider the manufacturer’s experience and longevity in the industry
By carefully considering these factors—certificates, innovative tools and machines, options for customization, and reputation in the market—you can make an informed decision when choosing the best CNC machining manufacturer to fit your demands.
Introducing KAIAO’s Rapid Prototyping Services
KAIAO offers high-quality rapid prototyping services that cater to diverse CNC machining needs from prototype to production. Here’s a chart to see the major offering of KAIAO’s rapid prototyping service:
Quotes | Certificate | Materials Choices | Tolerance |
1-1000 units Per CAD5 Days Delivery(Fastest) | ISO 2768 MediumISO 9001AS 9100ISO 13485 | Metals Aluminum, Brass, Copper, Stainless Steel, Steel Alloy, Titanium, etc. Plastic Acetal, ULTEN, CPVC, Nylon, PEEK, PS, PVC, etc. | ± 0.0003’’(0.010 mm) |
Conclusion
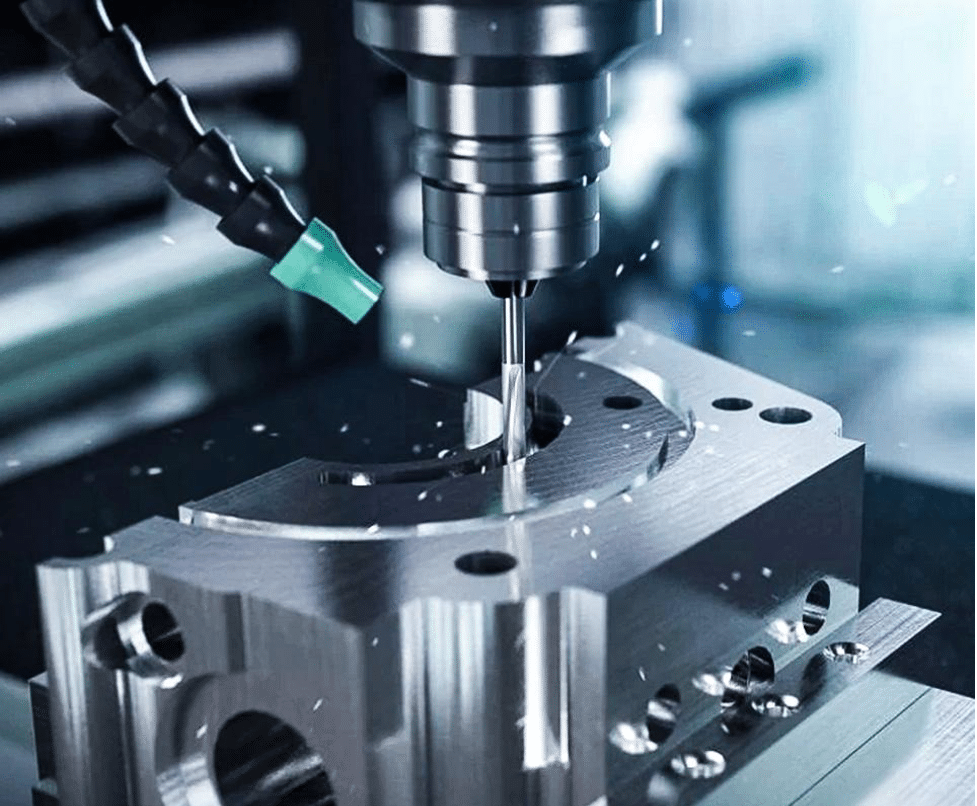
Choosing the right CNC machining manufacturer is crucial for achieving high-quality production. By considering factors such as certifications, advanced tools, customization options, and market reputation, you can ensure a successful partnership.
And KAIAO stands out with its comprehensive services, rapid prototyping capabilities, and industry-leading certifications. With over 20 years of experience, KAIAO offers advanced CNC machining, quick turnaround times, and exceptional quality control. Their tolerance control and experienced technicians ensure precise and reliable results. Trust KAIAO to be your reliable partner in CNC machining, providing top-notch solutions from prototype to production.
If you are interested, please visit their official website to learn more information and contact them!
Reference
- Available at: https://www.marketsandmarkets.com/Market-Reports/cnc-market-195192631.html