Factory and warehouse wages keep climbing—manufacturing pay jumped 8.7% last year while output barely budged[1]. Meanwhile, warehouses are demanding significantly higher minimum fees, yet still struggle to hire enough staff, a pattern echoed in persistent shortages across production lines, trucking, and storage, which push delivery costs up.
To tame these pressures, many operators now rely on automated material handling, which has proven effective in reducing labor costs and maintaining a steady goods flow, even amid staffing shortages.
Impact of Rising Labor Costs on Material Handling Operations
Warehouse managers are scrambling to find people, offering higher wages and sign-on bonuses to candidates, and the extra pay is straining budgets. Amazon invested $2.2 billion into wages last year to push the average fulfillment pay above $22 an hour[2], a costly benchmark for its rivals. Yet forklifts still sit idle because certified drivers are in short supply.
UK listings show driver pay up 8% and vacancies up 169% in just a year[3]. The overtime bills and temp-agency mark-ups sap funds for maintenance and slow order flow.
To relieve labor strain, many firms are investing in automated material handling systems that keep goods flowing without relying on scarce manpower. The global market is expected to grow from $33.3 billion in 2024 to $51.0 billion by 2029, at a CAGR of 8.9%[4], a clear sign of accelerating adoption.
What Is Automated Material Handling?
Automated material handling refers to the use of computer-controlled equipment to move, store, and manage goods with minimal human intervention. Key building blocks include conveyors that form fixed routes, automated guided vehicles that follow software-defined paths, and automated storage and retrieval systems that place and fetch items from dense racks. Sensors and warehouse control software link those machines, allowing them to see where goods are and avoid bumping into each other.
In a contemporary facility, conveyors transport pallets from receiving docks to an AS/RS, where shuttles or cranes automatically slide them into storage. When an order drops, the software releases the load and sends an AGV forklift to bring the tote to a packing bench. Because the control layer updates inventory in real time, people spend less time walking and more time handling exceptions while the system keeps goods moving around the clock.
Automated vs. Manual Handling: Cost and Efficiency
As automation becomes more accessible, its advantages over manual processes are increasingly evident in day-to-day operations.
Factor | Manual material handling | Automated material handling |
Labor costs | High and unpredictable due to wages, overtime, and staffing shortages. | Lower over time; after initial investment, maintenance costs are stable. |
Error rates | Prone to human errors such as mispicks, incorrect labeling, and misplaced goods. | High accuracy and consistency |
Downtime | Susceptible to disruptions from absenteeism, fatigue, shift changes, and labor disputes. | Capable of continuous operation with minimal interruptions, especially with preventive maintenance. |
Safety incidents | Higher risk of workplace injuries like strains, collisions, and falls. | Reduced incidents due to standardized processes, machine precision, and safety protocols. |
AGVs: Flexible Core of Automated Material Handling
Automated material handling includes a wide range of technologies such as conveyors, robotic arms, and smart storage systems. Among them, automated guided vehicles (AGVs) stand out as one of the most practical and versatile entry points. Their ability to navigate dynamic warehouse environments, integrate with existing layouts, and scale with operational needs makes them a core component of many automation strategies. For businesses seeking a practical starting point, AGVs offer a low-friction path to automation with minimal disruption and high adaptability.
Toyota’s assembly line now uses AGVs to transport car bodies, reducing both chain-conveyor noise and idle time. A heavy-vehicle manufacturer has adopted a similar approach, moving frames between work cells with less manual lifting and improved ergonomics. In the warehousing sector, Amazon’s new Ontario super-site operates over 7,000 mobile robots that deliver entire racks to pickers and help sort outbound cartons.
These AGV fleets not only streamline the movement of parts and parcels but also integrate seamlessly into broader automated material handling strategies.
What to Consider Before Adopting AGVs
While AGVs deliver clear efficiency gains, deploying them isn’t a plug-and-play process. From infrastructure readiness to workflow alignment, several factors should be considered before adoption.
- Layout: Confirm aisle widths, floor quality, and clearance weights to ensure AGVs can navigate safely and efficiently.
- Integration: Verify the AGV control software integrates with Warehouse Management System/Manufacturing Execution System and safety systems for smooth material handling automation.
- ROI Evaluation: Access total ownership costs, including acquisition, software, maintenance, and energy, against expected labor savings to verify the investment meets business goals.
- Employee Training: Schedule safety and operations training (hands-on demos, emergency actions, and daily troubleshooting) to help staff work confidently alongside AGVs.
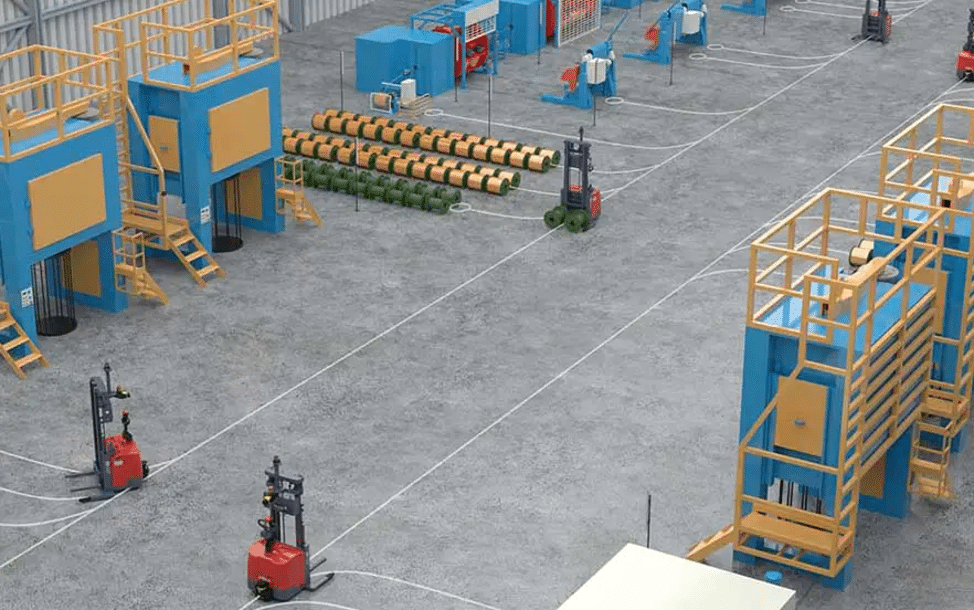
Partner With HELI for AGV Solutions
Labor-related pressures are reshaping how goods move through modern supply chains. Automation offers a scalable, sustainable response to rising costs and operational constraints. AGVs are a core tool in factory automation, combining efficiency and accuracy.
With decades of expertise in forklifts, HELI delivers advanced material handling solutions for intelligent logistics. Its AGV lineup includes pallet trucks, stackers, counterbalanced, and heavy-duty models, supporting tasks such as rapid sorting, unmanned warehousing, and production-line feeding. These vehicles integrate with WMS and MES platforms for seamless automation across factory and warehouse environments.
Additionally, HELI AGVs can handle precise material transfers, avoid obstacles using laser sensors, and automate replenishment tasks, thereby streamlining operations while advancing environmental goals.
If rising labor costs are holding back your operations, it may be time to explore intelligent automation. AGVs offer a smart, scalable entry point into Industry 4.0, helping you move faster, safer, and more efficiently. Reach out to HELI to discover the right solution for your facility.
References
- Labor Productivity Increases In Trucking But Decreases In Warehousing. Available at: https://www.forbes.com/sites/stevebanker/2025/07/07/labor-productivity-increases-in-trucking-but-decreases-in-warehousing/ (Accessed on July 9, 2025)
- Amazon raises pay of US hourly workers in fulfillment, transport ops. Available at: https://www.reuters.com/business/retail-consumer/amazon-raises-pay-hourly-workers-fulfillment-transport-ops-2024-09-18/ (Accessed on July 9, 2025)
- Driverless Forklifts are the Solution to Warehouse Recruitment Issues. Available at: https://www.eubusinessnews.com/driverless-forklifts-are-the-solution-to-warehouse-recruitment-issues/ (Accessed on July 9, 2025)
- Automated Material Handling Equipment Growth. Available at: https://industrytoday.com/automated-material-handling-equipment-growth/ (Accessed on July 9, 2025)
- 7,000 Robots power the largest US AMAZON Warehouse. Available at: https://www.agvnetwork.com/news/7-000-robots-power-the-largest-amazon-warehouse (Accessed on July 9, 2025)