Milling machines are invaluable tools in various industries, from manufacturing to construction. They are designed to work where precise shaping and cutting of concrete, asphalt, and materials is a major factor. Milling teeth, also known as milling cutters or end mills, are the most critical parts of these machines. They are the parts that do the cutting, and thus, they determine the milling machine’s performance and productivity.
Fitting your machine with the right milling teeth is the most important thing. You need to check not only the size of these teeth but also their quality. The best way to go around this is to deal with a reliable milling teeth manufacturer. JYF Machinery is one of the reputable companies in milling teeth production. Check them out for affordable milling cutter tools.
In this guide, we’ll explore the different types of milling teeth, their applications, how to replace them, and best practices for maintenance.
Types of Milling Teeth
The milling condition is among the factors determining the types of milling teeth. Milling asphalt surfaces may require different types of teeth from the concrete surfaces. The design of teeth may also be a factor in differentiating these teeth. Here are the most common types.
End Mills:
End mills are perhaps the most common type of milling teeth. They have cutting edges on the bottom and sides, allowing them to remove material from the surface and the side of the workpiece simultaneously. End mills come in various shapes and configurations, including square end, ball end, and corner radius end mills, each suited for specific cutting tasks.
Face Mills:
Face mills are larger milling cutters designed to remove material from the surface of the workpiece. They feature multiple cutting edges arranged on the circumference of the cutter. Face mills are commonly in facing operations, where large amounts of material need to be removed quickly and efficiently.
Shell Mills:
Shell mills are similar to face mills but have a larger diameter and fewer cutting edges. They are typically used for heavy-duty milling operations where high material removal rates are required. Shell mills are commonly used in machining centers and CNC milling machines.
Slotting Cutters: Slotting cutters, as the name suggests, are for cutting slots or channels in the workpiece. They have straight or helical teeth along the circumference of the cutter and are often used in conjunction with a milling machine’s indexing head for making precise cuts.
Ball Nose Cutters:
Ball nose cutters are specialized end mills with a rounded tip resembling a ball. These cutters are ideal for 3D contouring and sculpting operations, as they can create smooth curves and intricate shapes with ease.
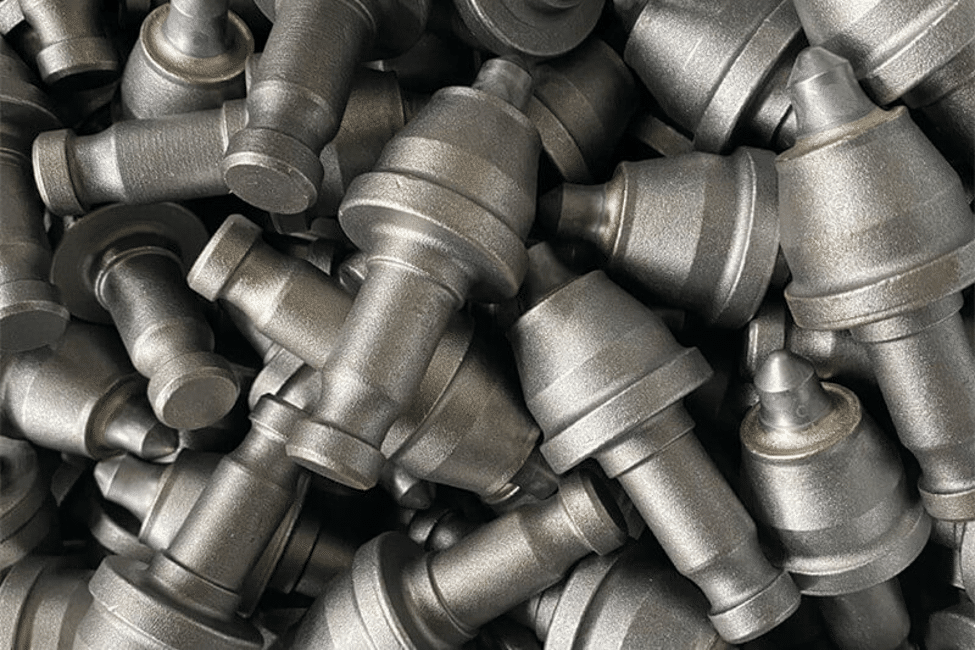
Applications of Milling Teeth
Here are major applications, especially in the construction industry:
Pavement Milling:
Pavement milling, also known as cold milling or asphalt milling, is a common process used to remove worn-out or damaged pavement layers from roads, parking lots, and other paved surfaces. Milling teeth are mounted on milling machines, which selectively remove asphalt or concrete pavement to a desired depth, preparing the surface for overlaying with new pavement.
Surface Preparation:
Milling teeth are used for surface preparation tasks such as leveling uneven surfaces, removing surface imperfections, and roughening concrete or asphalt substrates for better adhesion of coatings or overlays. This is particularly important in road construction and repair projects, as well as in the construction of industrial floors and parking areas.
Concrete Cutting and Profiling:
In construction projects involving concrete structures or elements, milling teeth are employed for cutting, shaping, and profiling concrete surfaces. This includes tasks such as creating expansion joints, removing excess concrete, and shaping concrete elements to precise dimensions.
Surface Texturing and Grooving:
In certain construction projects, such as bridge deck construction and repair, milling teeth are employed for surface texturing and grooving to improve skid resistance and drainage performance. Textured surfaces created by milling teeth help enhance the safety of roadways, bridges, and other transportation infrastructure by reducing the risk of skidding or hydroplaning in wet conditions.
Replacement of Milling Teeth
Replacing milling teeth is a routine maintenance task that ensures continued productivity and quality of machined parts. Here are the general steps for replacing milling teeth:
Select the Correct Replacement:
Identify the type and size of the milling tooth that needs replacement. Refer to the machine’s manual or consult with tooling suppliers to ensure compatibility.
Prepare the Machine:
Safely secure the milling machine and engage any locking mechanisms to prevent movement during the replacement process. Ensure that the machine is turned off and the power source is disconnected.
Remove the Old Tooth:
Use appropriate tools such as wrenches or spindle lock mechanisms to loosen and remove the old milling tooth from the machine spindle or arbor. Follow proper safety procedures and wear personal protective equipment as necessary.
Install the New Tooth:
Carefully insert the new milling tooth into the machine spindle or arbor, ensuring proper alignment and engagement with the tool holder. Tighten the retaining screws or clamping mechanisms according to the manufacturer’s specifications.
Check for Alignment and Runout:
Before resuming machining operations, perform a visual inspection to ensure that the new milling tooth’s secure installation and alignment with the workpiece. Use precision measuring tools such as dial indicators to check for any runout or misalignment. Finish with a test run.
Maintenance of Milling Teeth
Proper maintenance is essential for prolonging the lifespan and performance of milling teeth. Here are some maintenance tips to follow:
Regular Inspection:
Periodically inspect milling teeth for signs of wear, damage, or dullness. Replace worn or damaged teeth promptly to prevent quality issues and machine downtime.
Coolant and Lubrication:
Use appropriate cutting fluids or lubricants during milling operations to dissipate heat and reduce friction, prolonging tool life and improving surface finish.
Cleaning and Chip Removal:
Clean milling teeth and cutting surfaces regularly to remove built-up chips, debris, and coolant residue. Use compressed air or chip brushes to clear chip pockets and flutes effectively.
Sharpening and Reconditioning:
Consider sharpening or reconditioning dull milling teeth using specialized grinding equipment or services. Properly sharpened teeth can restore cutting performance and extend tool life.
Storage and Handling:
Store milling teeth in a clean, dry environment away from moisture, corrosive agents, and extreme temperatures. Use protective containers or trays to organize and protect cutting tools from damage during storage and handling.
Training and Education:
Provide training and education to machine operators and maintenance personnel on proper tooling selection, setup, and maintenance procedures. Empower employees with the knowledge and skills to optimize milling operations and maximize productivity.
Conclusion:
Milling teeth play a vital role in the success of milling operations across various industries. Understanding the different types of milling teeth, their applications, replacement procedures, and maintenance practices is essential for achieving optimal machining results. By investing in high-quality milling teeth and implementing effective maintenance strategies, users can enhance productivity, reduce costs, and stay competitive in today’s.