Steel fabrication is critical to the success of offshore and marine projects, providing the structural backbone for oil platforms, wind farms, and subsea systems. However, steel production itself poses significant environmental challenges, including high carbon emissions, intensive energy consumption, and resource depletion.
Efforts to transition to greener production methods are underway, with innovations like hydrogen-based steelmaking and increased recycling making strides. Yet, these technologies remain in the early stages of widespread adoption.
Reliable industrial steel supply, such as that provided by companies like Sun Steel, plays a crucial role in bridging this gap. In this context, addressing the environmental impact while maintaining performance standards for harsh marine conditions is a pressing concern for engineers and fabricators.
Steel’s Role in Offshore and Marine Applications
Steel dominates in offshore and marine industries because it balances strength, durability, and customizability. From massive oil platforms to subsea pipelines, it forms the foundation of critical infrastructure. Other materials might offer specific advantages, but steel’s ability to be fabricated into complex shapes and its predictable performance under stress make it essential.
Core Applications
- Platforms: Steel is used for jackets, topsides, and structural supports in offshore installations. These components need to resist constant wave action and extreme weather.
- Marine vessels: Hulls, bulkheads, and decks of ships rely on fabricated steel for integrity under operational stresses.
- Subsea systems: Pipelines and risers require steel capable of withstanding high pressures and corrosive conditions at depth.
Environmental Challenges in Offshore and Marine Fabrication
Corrosion Risks
Steel faces relentless exposure to saltwater and humidity in marine environments. These elements accelerate corrosion, reducing the lifespan of equipment and structures if not mitigated effectively. Solutions in practice include:
- Alloy selection: High-performance alloys like duplex or stainless steel resist corrosion in ways standard carbon steel cannot.
- Surface treatments: Protective coatings such as epoxy-based paint or galvanization are applied during fabrication to prevent oxidation.
- Cathodic protection: Sacrificial anodes or impressed current systems are often integrated into the design to protect steel components from electrochemical degradation.
Forces of Nature
Offshore projects encounter severe weather, including high winds, waves, and storms. Steel structures must remain intact under these dynamic forces, maintaining stability and safety.
Fabricators incorporate stress-relief points to allow for controlled movement under load. Joints are designed to withstand repetitive stress without cracking or failing.
Balancing Weight and Strength
Marine applications, particularly vessels, require steel to be strong yet lightweight. Excess weight can impair stability and increase fuel consumption, while insufficient strength compromises safety.
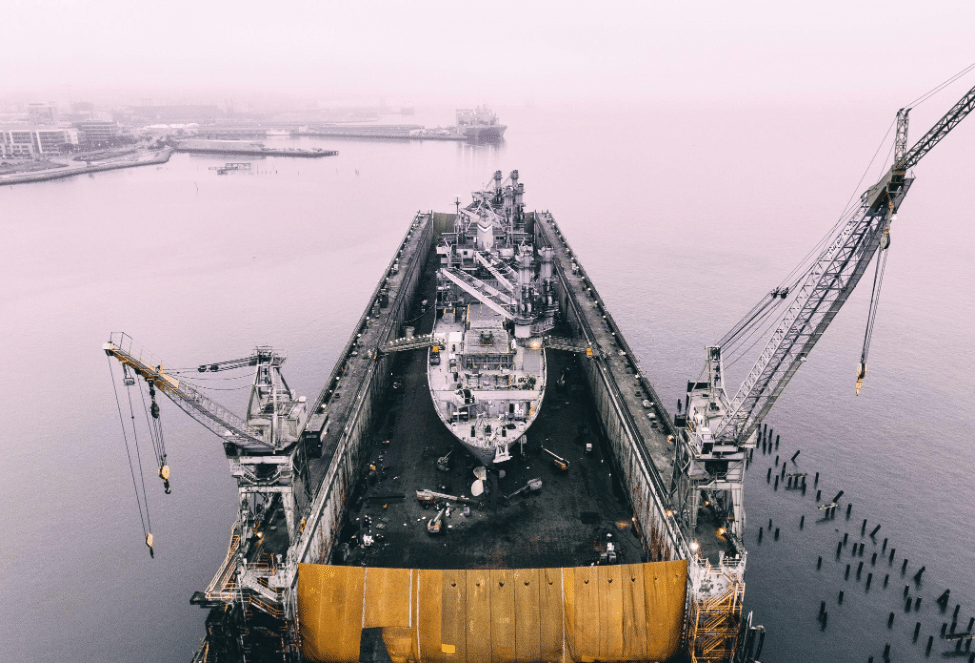
Modern cutting and shaping techniques, like laser or plasma cutting, reduce excess material without compromising strength. Materials that offer a better strength-to-weight ratio are often selected for key areas.
The Fabrication Process for Marine and Offshore Steel
Steel fabrication for offshore projects follows a structured process to ensure every piece is built to endure harsh conditions.
Selecting the Right Material
Steel grades vary widely, each offering different properties. For marine and offshore projects, considerations include corrosion resistance, weldability, and tensile strength. Fabricators often work closely with engineers to select materials that meet the exact demands of the project.
- HSLA: High-strength, low-alloy steel is a common choice for structural components due to its durability and affordability.
- Duplex: This material combines strength and corrosion resistance, making it ideal for subsea applications.
Cutting and Forming
Cutting and forming shapes the raw material into usable components. The choice of method depends on the thickness and complexity of the piece being fabricated.
- Laser cutting: Ideal for precision and clean edges, often used in detailed structural components.
- Plasma cutting: Suited for thicker sections that require speed and power.
- Forming techniques: Processes like bending and rolling create curved or angled sections needed for hulls or risers.
Joining and Assembly
Joining steel components is a critical stage. In offshore and marine contexts, welds must be flawless, as weak points can lead to catastrophic failures.
Techniques like submerged arc welding (SAW) or flux-cored arc welding (FCAW) are commonly used for their strength and reliability. Post-weld heat treatment (PWHT) can reduce residual stress in welded parts, increasing the material’s toughness and preventing brittle fractures.
Surface Protection
Without proper treatment, even the best steel is vulnerable to corrosion. Surface protection extends the life of the structure and reduces maintenance costs.
- Blasting and cleaning: Preparing the steel surface ensures coatings adhere properly.
- Protective coatings: Layers of paint or galvanization shield the steel from saltwater and moisture.
Rigorous Testing and Quality Assurance
Every component undergoes thorough testing to ensure compliance with safety standards. Fabricators use a combination of non-destructive testing (NDT) methods like ultrasonic testing and radiography to identify flaws without damaging the material. Load tests simulate real-world conditions to verify the steel’s performance.
Modern Innovations in Steel Fabrication
Automation and Digital Tools
Automation plays a key role in improving precision and efficiency. Robotic welders and automated cutting machines deliver consistent results while reducing human error. Meanwhile, advanced software allows engineers to simulate designs and test their viability before fabrication begins.
Hybrid Fabrication Techniques
Combining traditional steelworking methods with newer technologies, such as additive manufacturing, enables the production of complex shapes and components with minimal waste.
Modular Fabrication
For offshore projects, modular fabrication is increasingly common. Instead of constructing structures on-site, large steel modules are built in controlled environments and then transported to their final location. This approach reduces risks and speeds up project timelines.
Meeting Sustainability Goals
Steel fabrication, traditionally energy-intensive, is evolving to address environmental concerns. Recycling steel reduces the need for raw materials and minimizes carbon emissions. Fabricators are also adopting energy-efficient technologies, such as laser cutting systems, to lower their operational footprint. These changes reflect a broader shift toward sustainability within the offshore and marine industries.
To Sum Up
The steel fabrication industry faces a dual challenge: meeting the increasing demands of offshore and marine projects while minimizing its environmental footprint. This requires continuous innovation in materials, fabrication techniques, and sustainable practices.
The next decade will likely see a convergence of advanced fabrication methods, sustainability goals, and digital tools, creating opportunities for safer, more efficient, and environmentally responsible offshore and marine infrastructure.