Mechanical testing has become increasingly important for assessing material performance in research and industrial settings. Tensile and impact tests, in particular, provide insight into how a material responds to different types of stress. Yet, preparing specimens for these tests can be labor-intensive, especially when each sample must meet tight dimensional and surface finish requirements. Often, multiple machines or manual methods are required, increasing errors risk and prolonging turnaround times. As material innovation accelerates, finding a more simplified approach to specimen preparation becomes a necessity for obtaining accurate, repeatable results while managing costs. It has become possible for modern CNC systems to address this gap by combining tensile and impact sample preparation capabilities into a single platform, providing greater efficiency, consistency, and ease of use.
The Challenge: Two Types of Samples, One Common Goal
Traditional methods for producing tensile and impact specimens typically involve separate cutting, grinding, and milling steps on different machines. This process can cause scheduling conflicts and create additional expenses for maintenance and training. An integrated CNC system seeks to minimize these issues by allowing operators to prepare both flat tensile and impact test samples in one setup. These solutions often include preprogrammed profiles for a range of standards, such as ASTM and ISO, which minimize complex manual programming and reduce dimensional discrepancies.
Such a system can be especially valuable in laboratories with high sample throughput or limited space. Instead of dedicating resources to multiple machines, a single hybrid unit guarantees consistent tolerances, repeatability, and surface finishes. The result is a shorter learning curve for new operators and less room for error due to misaligned fixtures or manual measurements.
A real-world example is the TensileMill CNC – Classic Upgrade, which provides automated features designed for both flat tensile and impact specimens. It integrates robust fixture solutions, a user-friendly interface, and powerful servo-driven precision to meet strict testing requirements. By offering a compact, all-in-one system, it enables consistent, high-quality sample preparation without relying on multiple independent processes. This simplified approach helps labs maintain tighter controls on specimen quality, speed up their testing cycles, and channel more resources into analyzing results rather than struggling with preparation challenges.
Achieving Standard Compliance in Tensile and Impact Specimen Preparation
Compliance with international test standards is central to any comprehensive tensile and impact specimen preparation solution. Laboratories and manufacturers rely on standards such as ASTM, ISO, DIN, and JIS to guarantee uniformity, reliability, and global acceptance of their test results. Each standard specifies rigorous dimensional tolerances and surface finish requirements, assuring data comparability across different organizations and geographical regions.
Meeting these strict protocols demands precision machining capabilities and robust quality control measures. A well-designed system typically includes built-in profiles for each applicable standard, allowing operators to select preprogrammed parameters without extensive manual input. This reduces human error risk and speeds up specimen preparation.
Importantly, compliance with multiple standards reflects system adaptability. Industries ranging from aerospace to consumer goods often evaluate materials using different test methods, and a single integrated platform that satisfies these varied benchmarks can have a significant impact on the efficiency of operations.
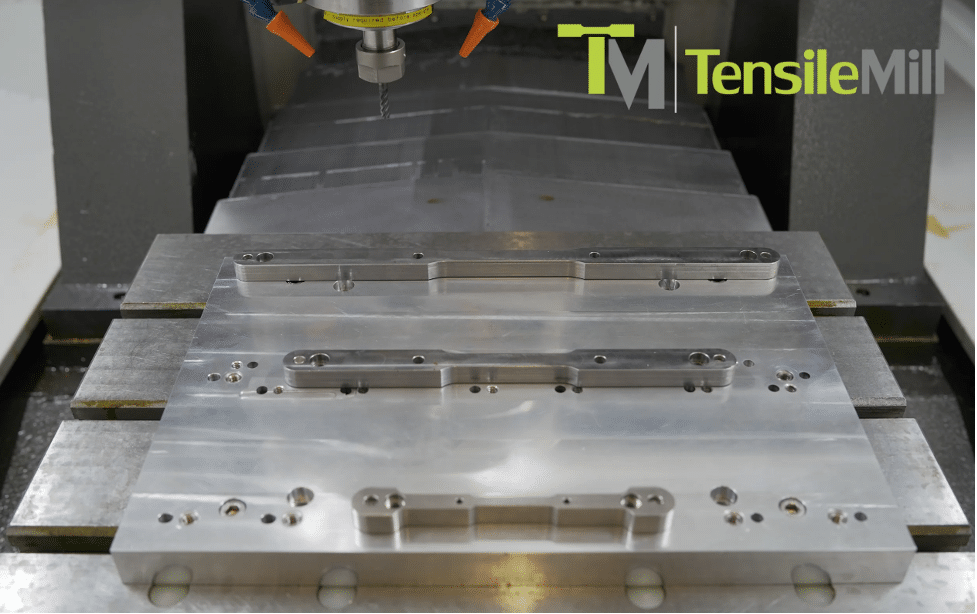
A Comprehensive Solution: A Hybrid CNC Approach and a Practical Example
Combining tensile and impact specimen preparation into a single system can greatly reduce material testing complexity and cost. Traditional methods often require multiple machines, specialized tooling, and significant operator oversight. In contrast, a hybrid CNC approach enables laboratories to prepare both flat tensile and impact specimens using one comprehensive platform. This simplifies workflows and minimizes errors caused by switching between separate processes.
A key example is the previously mentioned TensileMill CNC – Classic Upgrade, which consolidates both machining tasks into one robust unit. It is equipped with servo-driven accuracy, guaranteeing close tolerances for diverse specimen types. Operators can access preprogrammed standards (ASTM, ISO, DIN, JIS) through a user-friendly interface, reducing manual input and dimensional inconsistencies. The machine’s cast-iron frame and specialized fixturing help maintain stability, delivering repeatable results even when handling hard or thick materials.
Because it offers a single point of operation, this hybrid system simplifies maintenance schedules and lowers service costs. Operators only need to learn one machine’s controls, making training faster and easier. This system further reduces downtime between tests by automating tasks such as tooling changes and fixture adjustments.
More About TensileMill CNC – Classic Upgrade
In addition to its dual-purpose machining for tensile and impact specimens, the TensileMill CNC – Classic Upgrade incorporates several advanced features that improve day-to-day operations. For instance, an enclosed cooling system continually regulates tool temperature and evacuates chips, resulting in smoother finishes and extended tool life. The heavy-duty cast-iron body further minimizes vibration and chatter, resulting in highly consistent specimen geometries, even during high-speed machining.
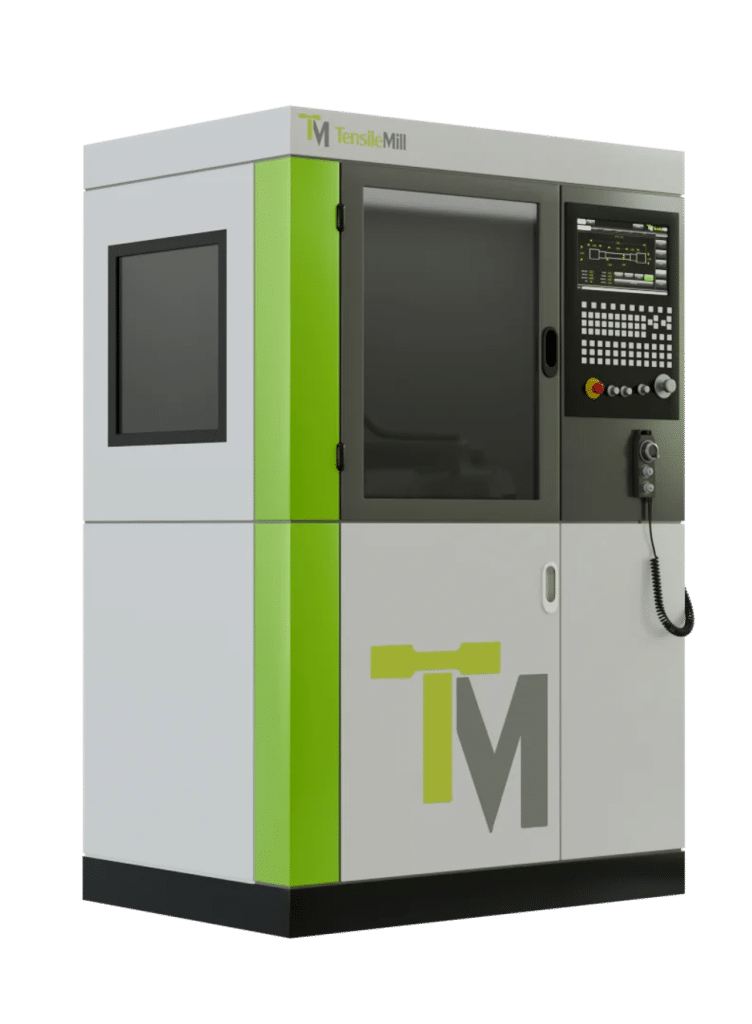
To support more specialized testing situations, operators can customize cutting parameters or create macros for non-standard sizes, enabling swift adaptation to evolving research or production needs. Advanced diagnostic features also monitor spindle loads and vibration in real time, automatically pausing operation if irregularities arise. This reduces material waste and protects both the machine and specimens from damage.
An optional remote interface allows supervisors to track performance and schedule preventive maintenance more effectively, particularly in facilities running multiple shifts or high-volume test cycles. By uniting these capabilities within a single CNC platform, TensileMill CNC – Classic Upgrade is a flexible and robust solution for modern labs that require efficient, accurate, and future-proof specimen preparation.
Who Can Benefit from a Hybrid CNC Solution
A hybrid tensile and impact specimen preparation system is valuable for a broad spectrum of material testing organizations. Quality control laboratories, which frequently process multiple batches of samples, can optimize operations by using one machine for both tensile and impact tests, thus providing uniformity of results and reducing equipment-related overhead. Manufacturers seeking rapid turnaround times for product development also benefit, as they can quickly produce test samples and identify any material inconsistencies before proceeding to full-scale production.
In research and development (R&D) environments, engineers often experiment with new alloys or composites that demand repeated testing for yield strength, ductility, and toughness. With a single CNC system handling various specimen sizes and geometries, R&D teams can move efficiently from one testing protocol to another, ultimately speeding up innovation cycles.
Academic institutions and training facilities, where budgets and available space are limited, find that housing a single hybrid machine simplifies setup and reduces capital costs. By facilitating hands-on learning on one centralized platform, students can gain practical experience in preparing both tensile and impact specimens without juggling multiple processes. In general, organizations of all sizes and specialties benefit from the accuracy, consistency, and reduced complexity of a hybrid CNC specimen preparation solution.