The Fourdrinier paper machine is one of the modern marvels of engineering. Developed during the early 19th century, it is often credited for fueling the Industrial Revolution, owing to its ability to manufacture paper in substantial quantities. This guide will delve deeply into how the Fourdrinier machine functions, its components, and the benefits it offers the industry. No technical expertise or prior knowledge of the field is required to appreciate the innovation behind this machine.
For more in-depth information you should view from Fourdrinier Paper Machine – UDTECH
What is a Fourdrinier machine, and what does it do?
The primary working parts of a Fourdrinier paper machine.
A Fourdrinier paper machine is made up of several primary parts that work interdependently to produce a continuous web of paper from a suspension of pulp. The major parts are headbox, wire section, press section, dryer section, and reel. The headbox or “heart of the machine” ensures that the pulp is correctly and uniformly sheeted onto the forming wire within the machine so that the sheet formed is uniform to all the dimensions. The wire section includes a moving mesh screen on which the pulp is laid in the form of a web. On the wire section most of the water content is removed by gravity and by agitation of the vacuum suction boxes. After the wire section comes the press section, where the newly formed sheet is further consolidated into a dense felt and most of the water is expelled. In the dryer section of the process, cylinders heated to high temperatures are used to remove any residual moisture. Finally, the paper is wound onto large reels in order to carry out subsequent operations.View Fourdrinier Paper Machine – UDTECH for More Details
The continuous sheet formation process explained
With the wire sections, the Fourdrinier paper machine marks the start of fully automatic paper production by offering a steady strip of paper. In a headbox, a moving wire starts to pull in the highly diluted pulp mixture offered by a feeder. This headbox offers fibers to be uniformly dispersed. As the wire moves, some water is drained which leads to the formation of a wet web. The web is now passed through the press section to further consolidate the fibers and remove superfluous moisture. After the wetness is decreased, the paper is sent to the dryer section, where steam-heated cylinders are utilized to dry the paper at a minimum percentage of water content. This nicely thin paper can then be rolled for storage or further procedures, all the while achieving impressive efficiency and enduring consistency.
Crucial breakthroughs identified in Fourdrinier machine design innovations.
Overworking of Fourdrinier machines has come with remarkable improvements in their design, which now performs effective and efficient multifunctional tasks\n\n. Current pieces of machinery have headboxes controlled by computers, which aids in the even distribution of fibers to sheets of paper. Alternative drainage systems like suction boxes and better quality wires have increased the efficiency of removing water from the mix. Moreover, the introduction of new efficient production dryers decreases the energy consumed during the making of paper. With the advancement in automation, operators can monitor production in real-time, facilitating rapid problem solving, thereby reducing downtime and ensuring consistency in product quality.\n\nThese massive improvements have ensured the position of the Fourdrinier machine in the making of modern paper.
In what way has the Fourdrinier machine transformed the paper industry?
A Comparison Between Fourdrinier Machines and Cylinder Machines
Each type of papermaking machine – the Fourdrinier and Cylinder Machine – is exceptional in its own right, as they both represent different stages in the evolution of papermaking technology. The advancement of the Fourdrinier machine has made it possible to produce long, continuous rolls of very fine, light-weighted paper that come with a high level of smoothness. This machine uses moving wire mesh screens to manufacture a continuous web of paper. As a result, it can produce a wide variety of paper grades with high precision and efficiency.
In contrast, cylinder machines are mainly used for thicker and heavier grades of paper such as paperboard. This variety of machine uses a rotating cylinder to build up layers of fibers, which are then amalgamated to give the needed thickness and weight value. Although these machines are not very effective at producing fine paper, they are highly useful for other applications like making multi-ply industrial grade paperboard or package paper, where a rougher structure is desired. The difference between the two machines illustrates the complication and versatility which exists in modern papermaking technology.
Increases in the Speed and Quality of Paper Production
Improvements in technology of the Fourdrinier machine has markedly changed the industry with respect to speed of production and quality of the end product.
The increase in machine output from operational innovations in wire mesh design and dryer section configurations allow for faster paper manufacturing without loss in quality. Moreover, advanced control systems such as automated moisture and thickness measurement help maintain product specifications to uniform standards during mass production.
Increased quality outcomes, including enhancement in pulp refinement and integration of advanced coating technology, have also bolstered the production of papers with superior opacity, brightness, and surface characteristics. These advancements meet the need for high-end applications such as specialty papers and premium printing papers to be produced in the modern market with great efficiency.
The Effect on the Manufacturing of Different Grades of Paper and Paperboard
The Fourdrinier machine’s versatility has greatly contributed to the production of a range of paper grades and paperboard materials. The machine’s ability to control a variety of pulps and additives enables the production of lightweight tissue papers to robust linerboard, which permits manufacturers to meet specific requirements such as coated papers for high-quality magazines or kraft paper that is durable for industrial grade packaging.
The Fourdrinier machine has also enhanced the capabilities of the cylinder machines for paperboard manufacturing by offering the production of single-ply boards that possess uniformity and high strength.
This innovation has broadened the use of paperboard to include advanced packaging, folding cartons, and even eco-friendly substitutes for plastic materials. Therefore, the Fourdrinier machine significantly contributes to modernizing and enhancing environmental protection in the global paper industry.
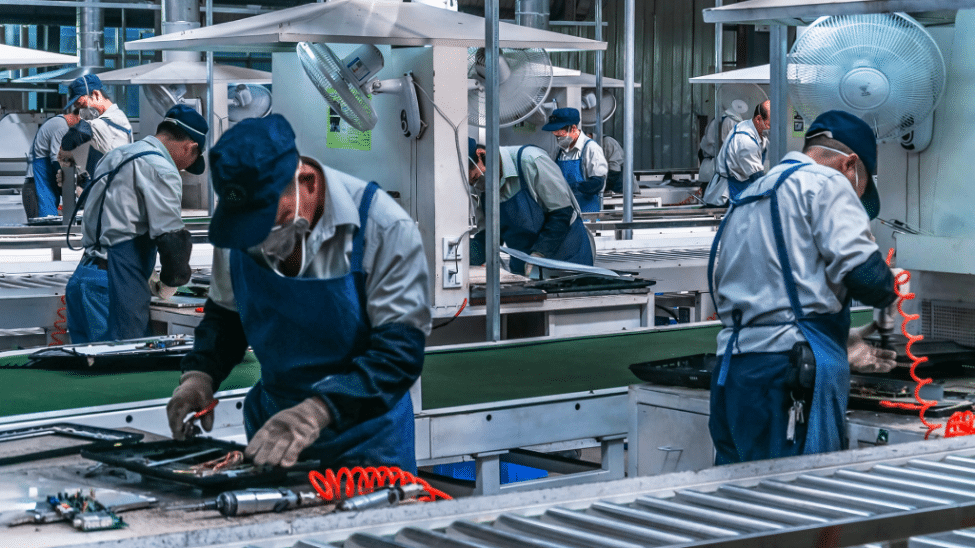
What are the components of a Fourdrinier paper machine?
The wire section: Where the paper formation starts.
The wire section marks the first phase in a Fourdrinier machine and it is where the combination of fibers, water, and other relevant materials is poured into an endless moving mesh or wire. This section is very important in the formation of the paper in that the water that is in excess must pass through the mesh and at the same time, the fibers must have started to interlock and form a sheet. Stringent control over interlocking variables of fiber distribution, drainage, and machine speed provides paper structure uniformity which is vitally important and gives an initial foundation for the later stages of the entire production process.
The press section: Smoothing and removing excess water from the paper
The paper that has been only partially formed makes its way to the press section after the wire section. This segment aims to decrease the water amount and enhance the strength of the partially made paper. Moreover, additional water is removed by passing the sheet through multiple press rolls that use mechanical pressure. Additionally, pressing smoothens the paper and better’s the surface texture. While high-pressure and temperature settings can lead to sheet breakage, damage control is cleared in this section as well. The optimization of efficiency and production on contrary maximizing finished outputs remains possible.
The drying section: Adjusting moisture levels to preferred state
The current stage in the workflow is ideally set between pressing and additional drying. Even though the sheet still has significantly retained moisture, additional drying is required to achieve target levels. The drying section of the sequence is then composed of a system of dryers or heated cylinders that evaporated water while the moisture content is carefully monitored. Remaining water is extracted while the paper goes through the conveyor system. To bring the paper’s moisture levels to desired outcomes while fixing its dimensions and features, stretching and drying temperature controls need to be effortlessly maintained throughout this stage. The ideal standard within this section is defined through no warping or defects within the paper.
Who invented the Fourdrinier machine and when?
Henry And Sealy Fourdrinier Story
Henry and Sealy Fourdrinier made essential contributions to the modern process of paper making. Previously, both were successful stationers but they spotted a gap when it came to efficient, high quality production of paper. They backed the design financially, which led to the invention of the machine that now bears their name. They did their fair share towards the industrial and technological progress in papermaking; however, there were financial problems for the Fourdriniers since so much money was needed in the development and constant refinement of the machine.
Donkin and Gamble were also key figures in the Fourdrinier ne constructors, along with the brothers: John Gamble worked in France and got the idea of continuous papermaking while Bryan Donkin built the first operable machines. Gamble and Donkin boldly poured money into this project and hired some of the best engineers to make their ideas a reality – thanks to their superb money investments and brilliant marketing ideas, machines that could produce paper were built, unlimited in volume and efficiency at the industrial level.
The first Fourdrinier machine at Frogmore Mill in 1803
In 1803, the first successful Fourdrinier machine was installed at Frogmore Mill, which greatly improved the efficiency of papermaking. Donkin Bryan created this machine based on previous models, and it was able to produce paper in continuous rolls, which was revolutionary during that period. At the same time, Frogmore Mill in Hertforshire, England became the headquarter of industrial papermaking, showcasing the Fourdrinier machine and paving the way for the widespread use of it in the industry.
In what manner does pulp preparation influence the performance of a Fourdrinier machine?
Pulp quality and consistency are key factors in output performance. A Fourdrinier machine is only as good as the quality and consistency of the pulp used during the papermaking stage. During this stage, pulp consistency defines the fiber content to its water ratio, expressed in percentage form. If an optimal consistency is not maintained, it would lead to improper distribution of the fibers, affecting the final output paper’s strength, texture, and appearance. High-quality pulp, clear of contaminants such as dirt, ink, and oversized particles, reduces the possibility of defects while increasing machine efficiency because of less downtime for cleaning the machine or performing other adjustments. Moreover, high-quality input also helps in controlling the production variability thus assisting in improving the overall control and predictability of the paper characteristics.
Fine tuning the ratio of pulp and water for different grades of paper
When it comes to producing newsprint, writing paper, or cardboard, specific grades require specific blends of pulp and water. The ratio of the fiber concentration shifts throughout the different grades, impacting thickness, porosity, and the smoothness of the paper’s surface. A mixture of specific pulp and water helps manufacturers achieve certain characteristics in paper while keeping the machinery operable. For example, high-quality printing papers require stringent control of fiber distribution to avoid a negative glare effect, whereas tissue papers that are more absorbent need a lower fiber concentration to enhance softness and flexibility. Fibers and waters ratio is very delicate in a way that improper ratio could lead to great results, but in combination with the Fourdrinier machine in particular, it would not be so efficient.
What are the benefits of twin wire Fourdrinier machines?
Enhanced Paper formation and two-side Printability
Twin wire Fourdrinier machines are ideal for improving the uniformity and overall quality of paper formation. More specifically, with the application of two wire meshes, these machines enable simultaneous drainage from both surfaces of the paper web. This minimizes the one-way typicality of the sheet. Furthermore, this dual drainage technique minimizes the discrepancies in fiber distribution and density, resulting in two-sidedness with improved quality. Consequently, the end product is a sheet with superior aesthetic and printing qualities, which is deemed vital for coated papers or specialty papers.
Increased Production Speed and Efficiency
The twin wire configuration, particularly the twin wires, enhances operational speed due to more efficient removal of water at the initial stages of paper formation. In addition, faster dewatering allows the machine to operate at increased production speeds without compromising sheet quality. Moreover, the dual drainage system reduces the need for drying, which lowers energy expenses as well as operational expenditures. These benefits render twin wire Fourdrinier machines the best option for producers seeking higher productivity with acceptable quality level.
In what ways have contemporary technologies improved upon the capabilities of a Fourdrinier machine?
Enhanced suction and dewatering techniques
Fourdrinier machines of today utilize sophisticated suction and dewatering techniques for more efficient removal of water during the papermaking process. High-capacity suction boxes and vacuum systems are built into the design to maximize water removal at these stages, which in turn facilitates more efficient and smoother sheet formation. These superior techniques diminishes the moisture content as much as possible for the sheet before it undergoes the drying phase which in turn saves energy for thermal drying that follows. Also, enhanced dewatering devices produces superior sheet quality and dimensional stability which meets the requirements for high-end paper products.
Computerized control for accurate paper production
Advanced computerized control systems have fundamentally changed the efficiency and accuracy at which paper products are manufactured using Fourdrinier machines. The installations are equipped with sensors, automated feedback systems, and live observation to track and control functions like headbox flow, wire tension, and machine velocity. It is imperative for manufacturers to always strive to achieve optimum limits for basis weight, moisture and sheet balance, with this level of control. In addition, these systems improve machine efficiency and reliability, lessening downtime due to problems with machine, which results in greater predictive maintenance and more efficient performance for changing production requirements.
Sustainability in Fourdrinier Papermaking
Implementing sustainability initiatives in Fourdrinier papermaking is in keeping with the industry trend towards embracing environmental accountability. The implementation of technologies like closed-loop water cycles, the utilization of energy-saving drying processes, and the incorporation of recycled paper fibers greatly enhances waste and resource efficiency. Additive components that are biodegradable and lower chemical constituent use enable manufacturers to protect the environment without compromising product standard. These practices, in addition to better meeting the regulatory requirements, are more appealing to the environmentally friendly markets which depicts the industry’s sustainable focus.