Natural gas meters are important in accurately measuring the amount of gas consumed by commercial and residential customers. By monitoring utilization, meters enable utility companies to appropriately bill customers for the gas supplied. They also help customers monitor and potentially reduce their consumption over time. There are three main gas meter types: diaphragm meters, flow meters, and ultrasonic meters.
Diaphragm Meters
Diaphragm meters measure natural gas flow via a flexible diaphragm located inside the measuring chamber. The diaphragm moves back and forth as the gas passes through the chamber, allowing the meter to indirectly detect changes in the flow rate. Repeated movements accumulate a tally of total gas consumption over time.
Operational Principle and Application Areas
Diaphragm gas meter types operate based on positive displacement. The diaphragm gas meter working principle divides the chamber into separate volumes. Gas pressure makes the diaphragm flex, trapping small measured amounts on each side. An electromagnetic pickup associates the movement with gas volumes. Individual measurements add up to generate accurate usage data. They handle low to moderate pressures well-suited for residential and light commercial use.
Installation and Maintenance Considerations
Due to their compact design, diaphragm meters can be installed indoors or outdoors. Outdoor units have weatherproof housing. Regular maintenance, such as periodic checks of indexes and registers, helps ensure long-term accuracy, depending on conditions.
Limitations and Constraints
As mechanical devices, diaphragm meters can develop errors over repeated movements versus static electronic meters. Harsh operating conditions cause faster degradation. The maximum recommended pressure is also lower compared to some other gas meter types. They are best for simple residential applications rather than large industrial flows.
Flow Meters
Flow meters, such as turbine meters and rotary meters, utilize distinct technologies compared to displacement meters.
Operational Principle and Application Areas
In these meters, a rotor or turbine is set within the gas flow path. As the gas passes through, the rotation of the turbine or rotor is measured to determine the flow rate. This rotational movement is converted into electrical signals, providing real-time data on flow rates.
These meters find widespread application across diverse industries, including oil and gas, chemical processing, and utilities, where precise measurement of high-pressure and high-flow gas streams is essential for operational efficiency and process control.
Installation and Maintenance Considerations
Installing turbine or rotary meters requires meticulous attention to detail to ensure accurate measurements and optimal performance. Proper alignment and calibration during installation are critical to achieving reliable results. Ongoing maintenance is necessary to uphold sensor integrity and prevent fouling, which can compromise accuracy over time. Regular inspections for wear and tear on internal components and scheduled cleaning procedures are essential to sustain long-term reliability and performance.
Ultrasonic Meters
Ultrasonic gas meters employ an innovative, nonintrusive design capable of highly accurate flow measurement. At the heart of these meters are ultrasonic transducers. The transducers generate and receive high-frequency sound pulses that pass through the transported gas medium.
Working Principle and Accuracy
By transmitting ultrasound in both the direction of gas flow and the opposite, the time differential for sound waves to cross the measured stretch can be determined with extreme precision. Since gas flow speed is the only variable affecting transit time, ultrasonic meters can calculate real flow velocity based on established physical formulas. With no moving parts to accumulate errors, the accuracy of these calculations is very high, and the maximum relative error is low.
Non-invasiveness and Application Range
Ultrasonic flow measurement leaves the inside of pipelines completely unobstructed, avoiding issues like deposits that plague intrusive sensors. This nonintrusive design allows them to be used in applications ranging from small residential systems to high-capacity industrial and transmission pipelines across all gas types. Operating pressures can reach over 100 bar.
Installation and Maintenance Considerations
Checking state of the meter is the only thing concerned during the installation, which ensures the accuracy of the meter readings. Minimal long-term maintenance is needed beyond regular verification, as there are no internal components subject to wear or fouling.
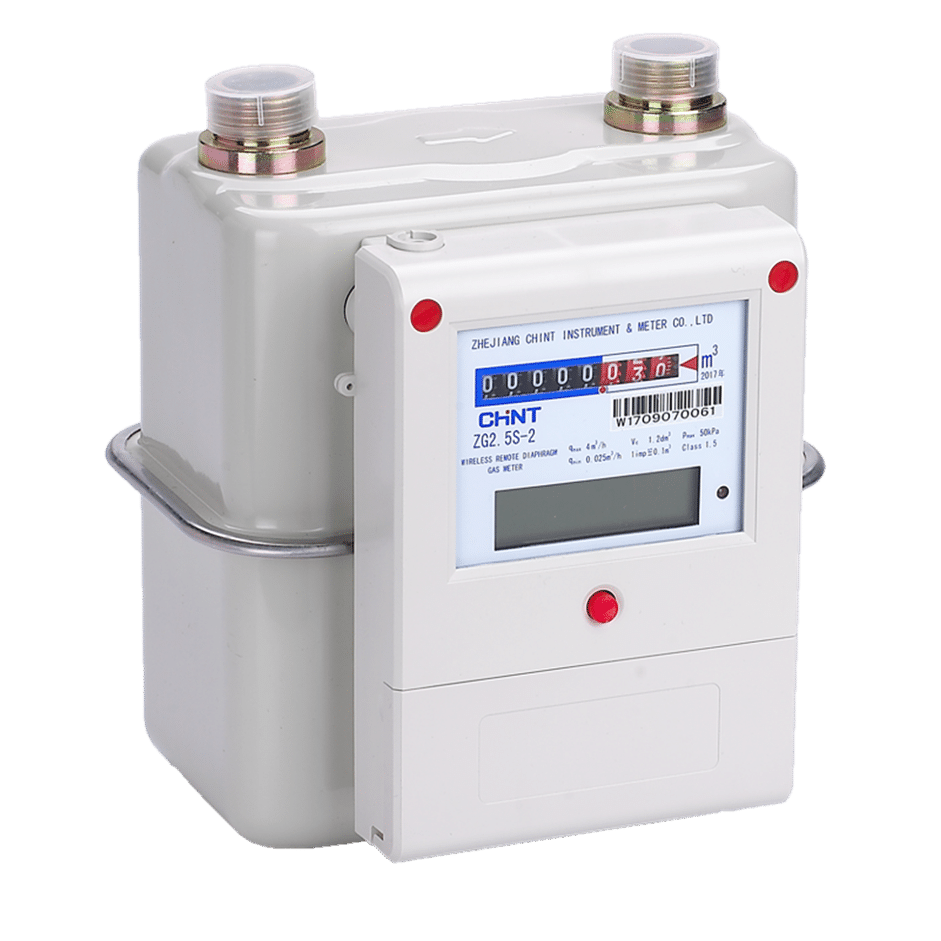
Factors to Consider When Choosing a Gas Meter
Selecting the appropriate natural gas meter for an application requires evaluating key characteristics of the metering point and intended usage.
Accuracy Requirements
For applications involving contractual utility billing of gas supply or resale, long-term accuracy assumes greater importance. National measurement standards may require a proven capability of maintaining errors well below 3% over 10-15 years of continuous operation under all flow and environmental conditions. Simple non-commercial metering of private residences demands less stringent accuracies, often in the 3-6% range is acceptable.
Flow Rate and Pressure Considerations
Most gas meter types are engineered to function optimally only within defined operating parameters. Understanding the maximum anticipated flow rate in cubic meters or cubic feet per hour aids in assessing if a meter’s rated flow capacity will not be exceeded.
It is also important to choose a reliable meter supplier. With years of experience in the industry, CHINT is a leading provider of advanced, smart energy solutions. The company has significant R&D and manufacturing capabilities, supported by thousands of employees in its global operations.
As a leading manufacturer of gas metering equipment, CHINT has a full products line, including diaphragm gas meters, NFC gas meters, IoT smart gas meters and LoRaWAN smart gas meters. They are well-suited for measuring the flux of flammable materials such as natural gas, liquefied petroleum gas, marsh gas, and city pipeline gas. Key advantages include:
- Pressure Range: Operating pressure ranges from 0.5 to 50 kPa, making them suitable for various gas flow conditions.
- Meter Management: With the smart parts, gas company can easily monitor the meter state, gas consumption and valve controlling remotely.
- Intelligent Measuring Control Device: The meters feature an intelligent measuring control device, offering low power consumption, resistance to magnet interference, a user-friendly interface with inquiry and valve-open buttons, high reliability, and anti-corrosion capabilities.
Conclusion
In summary, selecting the right natural gas meter involves assessing accuracy, flow rate, pressure, and maintenance requirements. Diaphragm meters are suitable for residential and light commercial use, while flow meters like turbine and rotary meters excel in industrial settings. Ultrasonic meters offer non-invasive, high-accuracy measurements for diverse gas types. Choosing a meter aligns with accuracy standards and operational needs, with suppliers like CHINT providing advanced solutions for reliable gas measurement.