For any product or equipment-based company, inventory management is of integral importance. Adequate stock availability prevents delays in customer service, leading to greater customer satisfaction and improved brand reputation. However, overstocking risks higher costs overall, particularly for storage and management of extra products. Overstocking items that are not frequently used also risks the potential obsolescence of products and lowers operational efficiency.
Although there are dedicated software options for data-driven inventory management, warranty management solutions can effectively aid in inventory forecasting. As warranty management software provides prediction and analytics data based on the warranty claims received, it can help OEMs and other businesses in accurate stocking of inventory. Depending upon the inventory prediction, the stocking of products can be optimized for current and future demands.
What is Warranty Prediction?
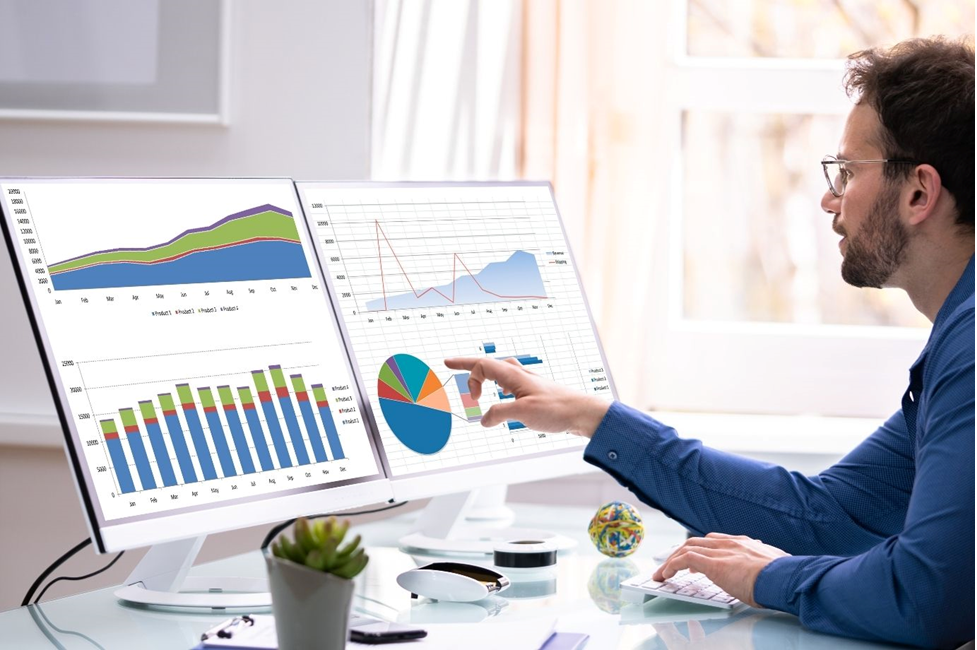
Warranty prediction is a process where past warranty data is used for warranty forecasting to identify and predict trends in future warranty claims. Product performance-related data is utilized to identify parts that frequently face warranty issues and breakdowns, requiring replacement. The warranty data analysis can then be used to optimize inventory management so that adequate preparations can be made for swift resolutions of warranty claims.
Apart from the management of inventory, warranty prediction can also help improve supply chain optimization as forecasting demands and identifying trends can enable proactive purchases through the supply chain. With advanced indication and predictive analytics, demands for specific products can be anticipated and prepared for, thereby improving demand planning. The data garnered from warranty forecasting can also be useful for product improvements, thereby reducing the need for warranties and part replacements overall.
Warranty prediction further boosts warranty management by reducing costs and streamlining the warranty processes. With a seamless and efficient process for warranty claims fulfilment, the process becomes faster resulting in reduced downtime for customers and improved customer satisfaction. Based on industry, niche, and types of warranties supported, warranty management software can be fully customized to meet the needs of an OEM or business.
What is Inventory Management?
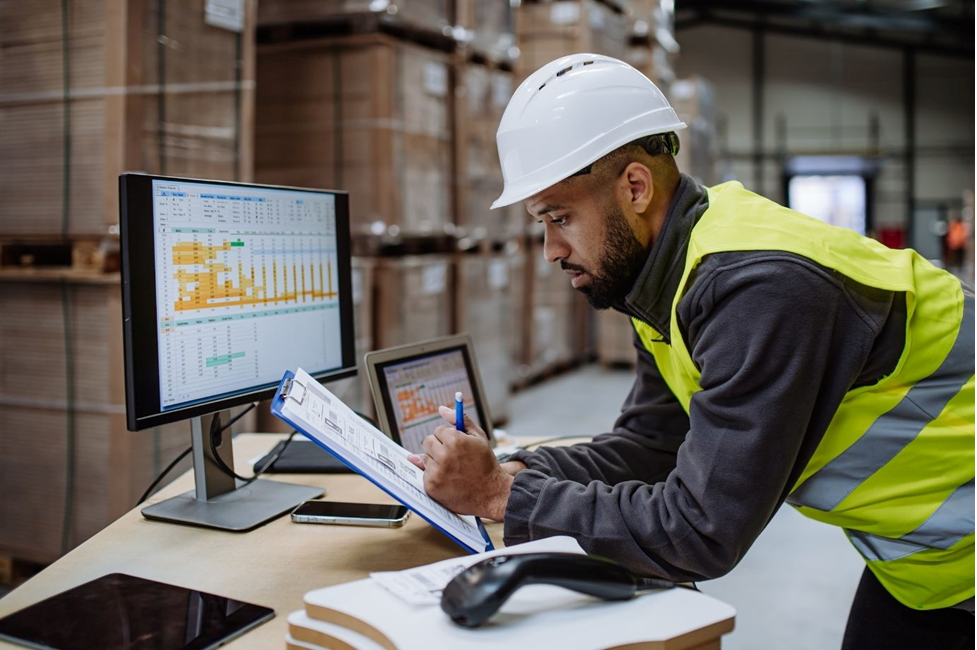
Inventory management refers to the overall management of the products and stock kept by a business. It includes the ordering of new items from suppliers, storing the stock before sales, and finally, selling the stock to customers. Accurate tracking, monitoring, and management is a necessity so that accurate stock availability can be maintained.
Depending upon the business, there can be nuances and challenges in maintaining stock optimization, for example, the size and expiry of products, and fluctuations in demand. Agile and flexible inventory management that can adapt to changing market demands can help provide a business with a competitive edge by quickly responding to customer demand trends.
Impact of Warranty Prediction on Inventory Management
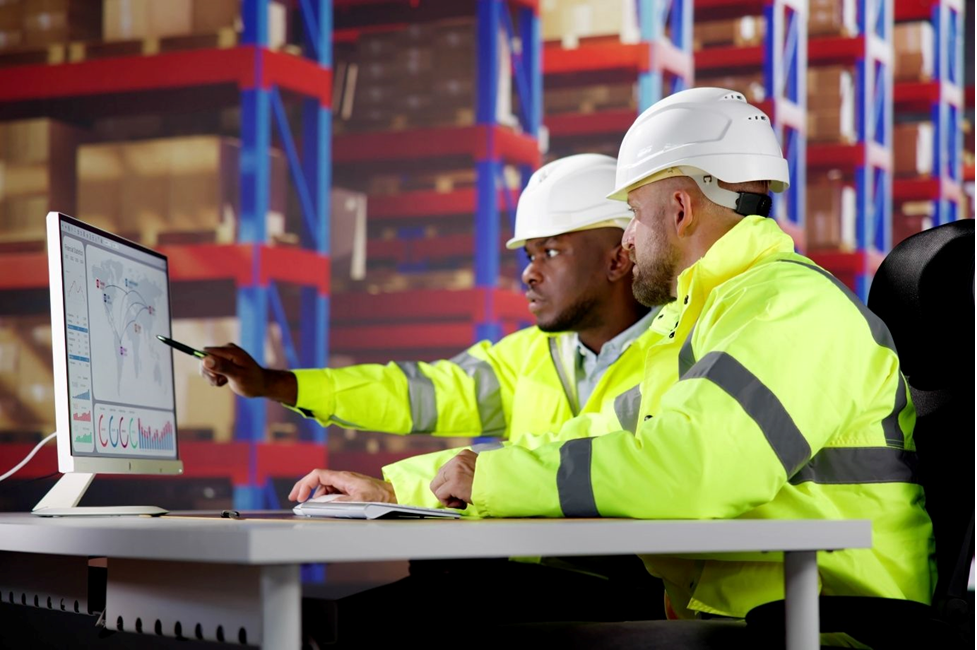
The capabilities of warranty management software continue to evolve, resulting in a wide range of additional benefits for businesses. Warranty prediction is a key feature of warranty management solutions with a significant impact on inventory management as well as cost management overall.
Some of the significant impacts of warranty prediction on inventory management include:
1. Stockouts Prevention and Reduced Overstocking Risks
Both scenarios, stockouts, and overstocking, are undesirable for businesses and can be improved with stock optimization through warranty prediction. Stockouts are situations where there is inadequate stock to meet the demands of consumers, resulting in added delays that reflect negatively on a business. Meanwhile, overstocking is when excess stock is maintained for extended periods of time without demand, resulting in overhead charges for storage and maintenance of the parts. Poor demand planning may even result in overstocking to such a degree that stocked parts become obsolete without demand.
Warranty prediction streamlines the overall inventory forecasting, providing usable insights into which parts and products are likely to face a demand. Predictive analytics have relatively high levels of accuracy and can aid in spare parts management by identifying which products are likely to be in demand and approximately when that demand will arise. Based on upcoming demands, businesses can plan their inventory replenishment, thereby preventing stockouts and reducing the risks of overstocking.
2. Supply Chain Optimization
As companies become more global and supply chains increasingly complex, the risk of delays is inevitably higher. Depending upon the particular niche and industry, the supply chain of a company can spans across multiple locations and several days. While convenience and speed of delivery may be a factor for businesses, the cost-benefit analysis is a more important criterion. In situations where the supply chain is extensive, there is an added risk of delays when supplying customers.
Adequate supply chain optimization aids in improving the overall efficiency of the supply chain network so that required products arrive on time and as needed. Warranty prediction aids in improving the supply chain by providing greater insights for inventory forecasting. By knowing in advance which products are likely to face a demand, businesses have more time to move products through the supply chain in a cost-efficient manner, resulting in greater operational efficiency.
3. Improved Spare Parts Management
Spare parts management may be similar to inventory management to some extent, however, for OEMs and businesses supporting spare parts replacements, there is even greater importance of speed and adequate stock availability. For larger equipment and machinery, the breakdown of individual parts can lead to a complete halt of operations, requiring speedy resolutions. Smaller spare parts can also pose a challenge in management since tracking and monitoring large volumes of spare parts can be difficult.
Although OEMs and businesses dealing extensively with spare parts can benefit from a dedicated spare parts management software solution, even warranty management software can offer substantial benefits. Warranty data analysis can aid in forecasting the demand for specific parts so that inventory replenishment can take place in time. Moreover, with predictive analytics, specific parts can be serviced and maintained proactively, thereby predicting breakdowns overall. Spare parts that are frequently facing challenges can also be flagged for other users and inventory prepared accordingly.
4. Efficient Cost Management
In inventory management, costs can easily add up through holding costs, ordering costs, maintenance costs, overhead costs, and more. While some costs are unavoidable, there are measures that businesses can take to improve their risk management in inventory. Conducting a cost-benefit analysis can aid in identifying some areas of improvement for saving costs, however, for ongoing savings, an ongoing solution is needed.
Warranty prediction aids in inventory cost savings in multiple ways, providing sustainable improvements in cost management. By improving the accuracy of inventory forecasting, overhead stocking, and holding costs can be reduced. With enhanced demand planning, ordering costs can be significantly reduced, including last-minute ordering costs. Data-driven inventory management helps reduce overhead stock which also lowers administrative, and labor expenses otherwise involved in maintaining larger stocks.
Bonus Advantages of Warranty Management Software
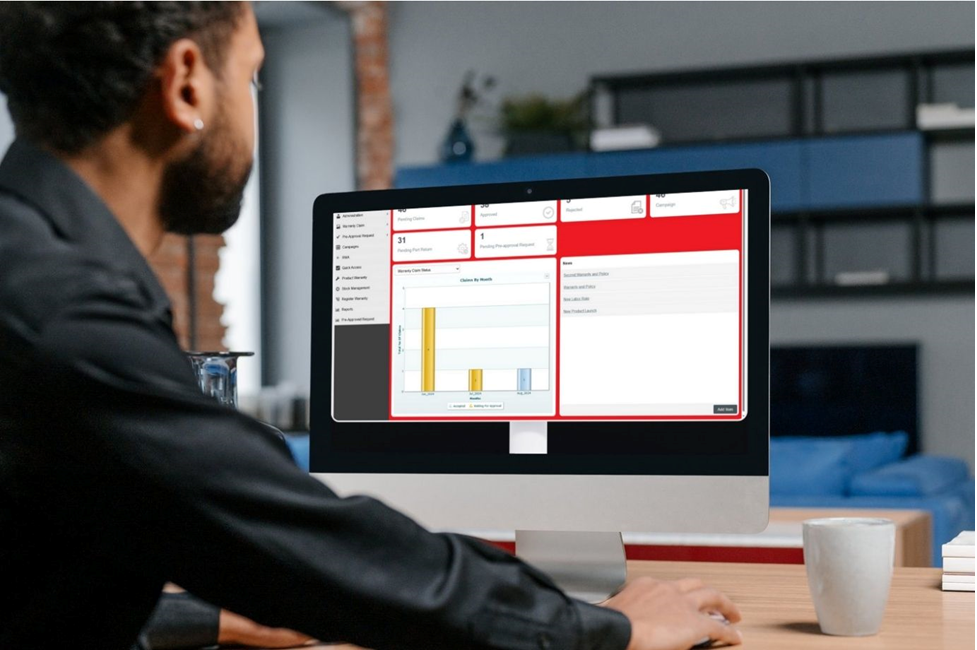
Warranty prediction is a key advantage of warranty management software for robust and accurate inventory management, however, there are several more benefits of such software solutions as well. The primary advantage of warranty management systems is that they streamline the entire process for warranty claims, including warranty forecasting. With an automated system, OEMs of any size can support any number of warranties for their customers, resulting in fast and efficient resolutions of customer claims.
Some of the bonus advantages of warranty management software include:
1. Support for Versatile Warranties
Warranty management systems are inherently scalable and can support a wide range of warranty types as well as claim types. Depending upon the specific industry and niche, chosen warranties can be supported, and accepted warranty claim types be programmed. This provides added flexibility for OEMs as they can offer the warranty and claim types that suit their products the most.
2. Full Transparency
With multiple teams and divisions involved, as well as stakeholders such as dealers and suppliers, warranty management can become complicated and at risk of miscommunication. Warranty management software provides audit trails and dedicated dashboards for users so that there is complete transparency and accountability throughout the process.
3. Automated Processes
An automated process for handling warranty claims can have a massive impact on speeding up the fulfilment of claims filed. Depending upon OEM preferences, programmable rules can be set up to automatically filter and deal with incoming warranty claims. The automated process enables speedy resolutions while also minimizing the risk of human error.
4. Warranty Fraud Prevention
Warranty fraud can be a significant contributor to warranty costs and can result in increasing losses over time. Moreover, once warranty fraud has taken place, chances of further fraudulent activities are likely to increase. Warranty management software incorporates the usage of multiple verification and validation checks in the process of filing warranty claims, leading to better protection against fraudulent activities.
5. Product Improvement
The insights and warranty data analysis provided by warranty management systems can be immensely valuable for an OEM or business. The data, apart from applications in inventory forecasting, can also be used for overall product improvements. If there are particular parts or components that are frequently facing complaints and challenges, those parts can be considered for overall improvements. By improving the quality of the original products, the need for warranty claims can be reduced and operational efficiency and customer satisfaction increased.
6. Easy Integrations
With modern technologies available to optimize multiple business processes, the use of dedicated systems such as ERP and DMS is on the rise. Warranty management software can be directly integrated with the existing systems an OEM or business is using, resulting in minimal interruptions to currently ongoing business processes. This simplifies the adoption of new software and seamlessly adds new capabilities.
Conclusion
Optimal inventory management is a crucial priority for business because it allows stock optimization and customers to be provided with timely service without expensive overstocking. Reliable management of inventory helps with stockout prevention and enables timely inventory replenishment. While multiple strategies may be utilized to improve risk management in inventory, there is a growing usage of warranty prediction for inventory management.
Warranty prediction is a component of leading warranty management software solutions that utilizes warranty data analysis to aid businesses in identifying trends and forecasts. These predictions can be immensely useful in planning stock availability, depending on warranty claims filed in the past. The warranty claims forecast aids businesses in preparing for both future claims as well as inventory to meet upcoming demands.