With the growing demand for high-precision custom parts, CNC machining has become a widely used technique for producing complex components with tightly controlled dimensions through automated toolpaths. However, achieving the desired level of precision depends on defining optimal tolerances, which refer to the acceptable limit of variations in a part’s dimensions and geometries. Establishing CNC machining tolerances that satisfy both design and cost needs is crucial, as tighter tolerances increase precision but also production costs and challenges, while looser tolerances could compromise functionality. The importance of precision in manufacturing continues to increase with miniaturization and integration of components.
Understanding CNC Machining Tolerances
CNC machining involves using computer-controlled machine tools like mills and lathes to cut raw materials like metals and plastics into net shapes according to programmed toolpaths. With its ability to precisely manipulate tools and position parts inside the machining envelope, CNC machining plays a pivotal role in consistently achieving close tolerances throughout production.
How CNC machining tolerances are defined and inspected varies depending on the material and complexity of the part. For metal parts, the standard tolerance is typically +/-0.005 inches. On the other hand, it is usually +/-0.010 inches for plastic parts. Tighter CNC machining tolerances can be achieved for critical applications, e.g., medical implants, etc., through extended machining cycles. The inspection of these tolerances is done using instruments like micrometers, calipers, and height gauges.
CNC Machining vs Injection Molding: Tolerance Comparison
Being two of the most prevalent industrial manufacturing processes, CNC machining and injection molding differ vastly in their capabilities to achieve tolerances. While injection molding is ideal for high-volume production, CNC machining provides greater precision and flexibility for low to mid-volume runs. The following aspects highlight their differences:
1. Process Precision
CNC machining can hold tighter CNC machining tolerances (0.001 inches achievable) compared to injection molding (0.005 inches), depending on part geometry and material. This level of precision is achieved through high-accuracy computerized toolpaths and position control.
2. Material Considerations
CNC machining supports a much wider range of materials compared to injection molding’s limitations to thermoplastics. CNC can machine metals, plastics, composites, ceramics, and other exotic materials. This versatility allows for broader engineering possibilities compared to injection molding’s thermoplastic constraints.
3. Complexity and Design Flexibility
CNC machining can accommodate far more complex geometries with internal and moving features than injection molding. It can machine parts with intricate internal cooling channels and multi-axis complexities and design adaptabilities that injection molds struggle with. CNC is also more flexible for design changes due to its subtractive process versus molded cavities.
4. Surface Finish and Secondary Operations
Injection molded parts typically require secondary surface finishing operations like polishing, painting, or etching to achieve desirable surface textures and appearances. CNC parts often result in near-net shapes requiring little or no post-processing directly from the machine tool.
5. Tooling and Setup Time
While injection molds have much lower per-unit costs for long production runs, their tooling setup and lead times are considerably longer than rapid CNC tooling. However, CNC tool changes and part modifications can be made much quicker to support flexible, low-volume production.
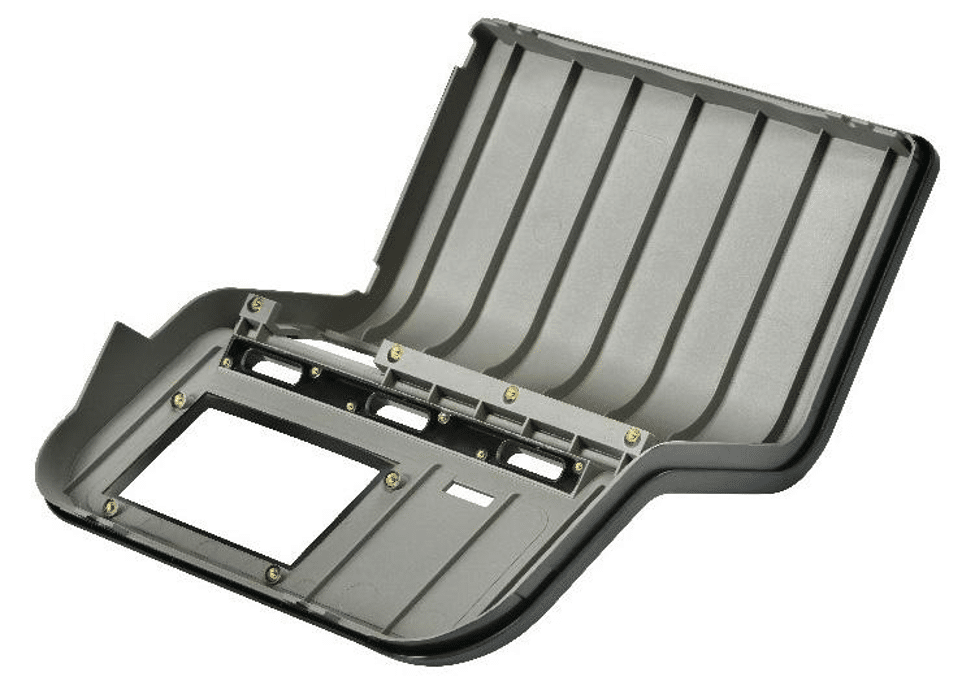
HordRT Offers Reliable CNC Machining and Injection Molding Services
For high-quality prototyping and low-volume production with ensured reliability, choosing an experienced provider of both CNC machining and injection molding services is ideal. HordRT has been serving global customers excellently for over 20 years with its diversified in-house manufacturing capabilities, services, and a team of industry experts.
1. CNC Machining/Rapid Prototyping Ser custom aluminum machining vice
HordRT’s technical team has extensively researched rapid tooling standards and CNC machining tolerances to balance quality, speed, and cost when it comes to CNC machining/rapid prototyping. Using advanced CNC machines and streamlined processes, the company can deliver prototypes in as fast as 1 day. Its machining expertise supports complex geometries with tight tolerances for medical, automotive, aerospace, and other precision applications. Other advantages/services include DFM analysis, NO MOQ, up to 30% cost-efficiency, and more.
2. Rapid Plastic Injection Molding Service
For plastic injection molding, HordRT has a massive production capacity. The brand’s injection molding machines can produce plastic parts of any size or complexity rapidly and efficiently. The company offers a wide choice of engineering-grade plastic injection molding materials along with optional surface finishes. Its strict quality controls ensure dimensional accuracy and consistency across high volumes.
Conclusion
Overall, HordRT’s wide range of advanced manufacturing solutions, expertise in precision machining capabilities to meet tight CNC machining tolerances, and dedication to quality make it a reliable partner for complex tolerance-critical applications. Visit the company’s website to explore its full range of rapid prototyping and manufacturing solutions.