Plastic pipe extrusion lines are essential to modern manufacturing processes. With precision and efficiency, these systems produce pipes of various specifications, ranging from PVC pipes for irrigation systems to HDPE pipes for the telecommunications industry.
Understanding these pipe production lines will be helpful for you to choose the right equipment and solution for your production needs. In this article, we will walk you through the plastic pipe extrusion line and offer you valuable insights on the right machinery!
What Is a Pipe Extrusion Line?
A pipe extrusion line is a manufacturing setup designed to produce plastic pipes in a continuous process. These systems utilize a combination of machines to heat raw materials, form them into the desired shape, and then cool them to maintain structural integrity. The resulting pipes are used in various sectors, from water supply systems to gas pipelines and electrical conduits.
Advantages of Using Pipe Extrusion Lines
Pipe extrusion lines offer several benefits, making them an ideal choice for mass production:
- High Production Speed
An automatic pipe extrusion line can manufacture pipes at an incredibly fast rate, ensuring you meet high demand with ease.
- Consistent Manufacturing
They deliver uniformity in product dimensions, like length and diameter requirements, ensuring every pipe meets the required industry standards without defects.
- Versatility
These systems are adaptable to process different plastic materials, like PVC, PP, PE, and others, producing pipes for different applications, whether it’s for water supply, drainage, or industrial use.
- Cost-effectiveness
By automating the production process, pipe extrusion lines significantly lower labor costs and waste, making them a worthwhile investment for manufacturers.
With a basic understanding of what these systems are and why they’re advantageous, let’s look at the critical machinery needed to set up a plastic pipe extrusion line.
What Machines Are Used in a Pipe Extrusion Line?
A complete plastic pipe extrusion line incorporates several key machines working in harmony. Below, we’ll explore the purpose and function of each component:
1. Extruder
The plastic pipe extruder is the heart of the pipe extrusion line, and two primary extruder types are single-screw and twin-screw extruders. Generally, they work with the following key parts:
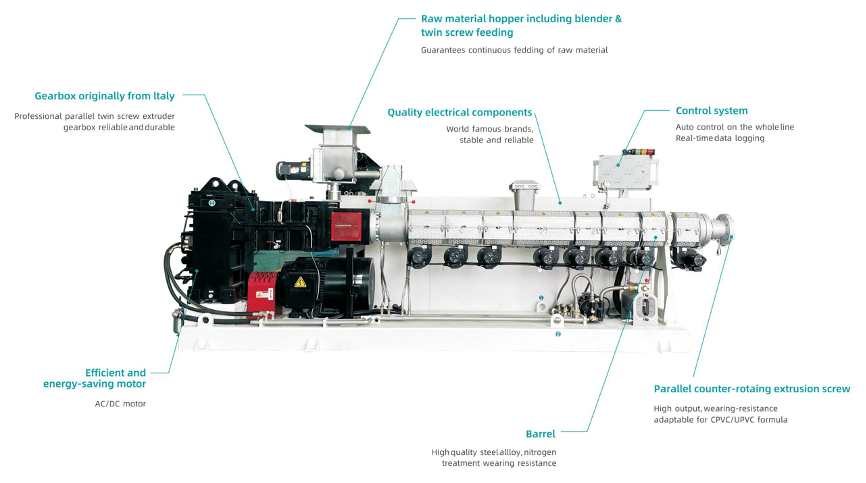
Twin-Screw Extruder Example
- The hopper, where the raw plastic material and additives are stored and then released into the barrel.
- The barrel, which has different temperature zones to ensure the proper melting of the raw material.
- The screw within the barrel, which pushes the material forward and facilitates proper mixing and melting.
- The screen pack, which filters out impurities and ensures a consistent and uniform flow of molten plastic, contributing to the quality of the final product.
2. Die Head
The die head determines the shape and size of the pipe. Two common types are screen basket dies and spiral mandrel dies. These dies usually need to be designed according to the pipe’s material, section size, and pressure class.
3. Vacuum Calibration Tank
The vacuum calibration tank will calibrate and cool the extruded plastic in a vacuum environment. The profile is pulled through a calibrated mold to ensure dimensional accuracy, and there is a water cooling system to quickly solidify the final shape.
4. Cooling Tank
After initial calibration, the cooling tank further reduces the temperature of the pipe. This step is critical for ensuring the pipe retains its specifications without warping or shrinking.
5. Haul-off Unit
The haul-off unit pulls the pipe steadily through the entire production line. It ensures uniform speed during extrusion and cooling, contributing to consistent product dimensions.
6. Cutting Unit
This unit accurately cuts the long continuous pipe into specific lengths according to requirements. It can be selected depending on factors such as pipe diameter, thickness, material, production speed, and more.
7. Control System
The control system manages the entire pipe extrusion operation. It monitors temperatures, speeds, pressures, and other essential parameters, allowing operators to maintain product quality and minimize errors.
How to Choose the Right Machines for a Pipe Extrusion Line
Selecting the right machinery requires a detailed understanding of your production needs. Below are some key points for you to make an informed decision.
1. Factors to Consider
- Production Capacity
Match your production needs to the capacity of the pipe extrusion line. High-capacity machines are better suited for large-scale projects, while smaller setups work well for niche markets or lower demands.
- Material Type
Different plastics, such as PVC, HDPE, and PPR, require specific processing conditions. Ensure the plastic pipe extruder and other equipment are compatible with the materials you’ll be using.
- Pipe Specifications
The size, wall thickness, and application of the pipes should guide your choice of machinery. For example, pipes used for gas transmission demand higher standards compared to standard water pipes.
2. Custom Pipe Extrusion Line Options
If off-the-shelf solutions don’t meet your needs, consider customized options. Custom setups can be tailored to your specific production goals, materials, and pipe dimensions.
In this case, it is paramount to partner with a reliable and experienced pipe extrusion line provider. Dekuma can be a trusted name within the industry with its 40+ years of experience. This brand features impressive advantages, including:
- High Production Efficiency: Dekuma develops advanced extrusion equipment for high output and consistent quality, suitable for large-scale production.
- Diverse Material Solutions: There are one-stop solutions for various materials (PE, PP, PVC, TPV, PA, PC, ABS, EVOH, Fluoroplastic), meeting diverse production needs.
- Wide Industry Applications: Dekuma’s extrusion lines serve multiple industries (construction, communications, automotive, and more), with a global client base across Europe, the Americas, the Middle East, and Asia.
Final Thoughts
A pipe extrusion line is a game-changing investment for industries looking to produce high-quality pipes efficiently and cost-effectively. By understanding the machinery involved and considering your specific needs, you can build an efficient pipe production system that meets your goals.
For those seeking top-tier equipment, manufacturers like Dekuma offer exceptional extrusion line solutions. Why not contact Dekuma to see if they have a standard offering that’s right for you? It’s also worth reaching out to them for their professional custom services!