Tooling is a significant process in designing high-precision parts to meet the specific requirements of an application. The process usually starts with basic materials and turns them into the final-use product using technology, skilled workers, and the right tools. So, what is tooling in manufacturing? Tooling involves the development of tools used to form, shape, or mold raw materials into a specific part.
Read on to find out more about what is tooling. How tooling impacts your manufacturing processes and how you can achieve the best outcomes.
What Is Tooling in Manufacturing?
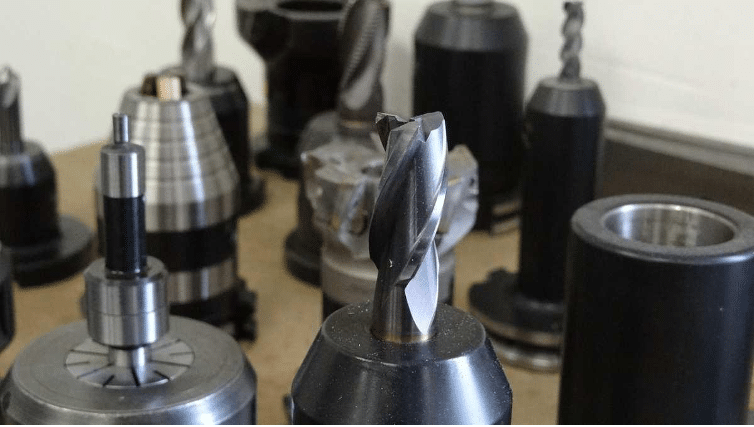
CNC Tooling
Tooling can be described as the forming of materials mainly to produce accurate and exclusive parts. These components are typically defined by specified tolerances. Tooling applies various apparatus including jigs, molds, patterns, fixtures, and cutting tools, to mold and develop these parts. The type of tooling equipment used depends on the general production requirements, the part type, and the tooling size.
Every business needs to have the right equipment for it to run as planned. To this extent, tooling is a critical component in the manufacturing process since the process cannot achieve the desired outcomes without it. Moreover, changes in tooling technology can significantly impact production speed, product quality, and cost.
Role of Tooling in Manufacturing
Tooling has a sizable influence on mass production. Because it increases the speed and decreases the operational expenses. The key to producing quality products efficiently lies in the tooling.
Part Precision
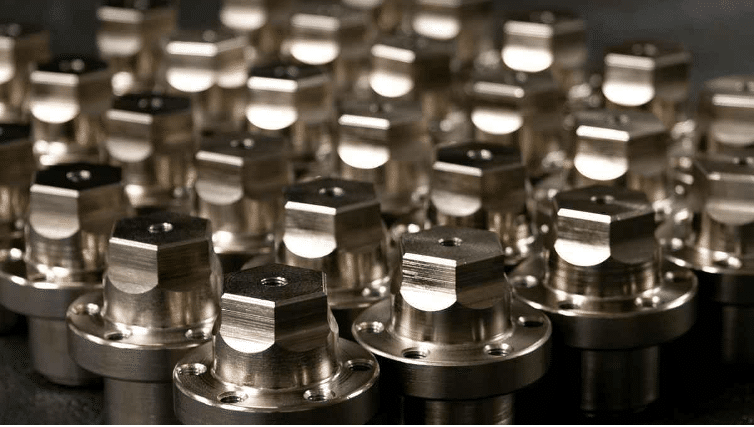
Precision Machined Parts
Tooling is an important area where precision engineering has a major influence. The quality of these tools defines the degree of the components’ precision and uniformity. No matter the product to be manufactured – an injection-molded part or an aircraft component – the quality of the tool is central to the outcome.
Production Efficiency and Operating Costs in Manufacturing
There are certain processes typically exist in manufacturing, which are aimed at the tooling procedures. Techniques such as inject molding, for instance, make it easy to produce numerous similar parts with little or no deviation. Although tooling has a high initial cost, the cost per unit is much lower in the long run compared to other methods.
Custom Parts
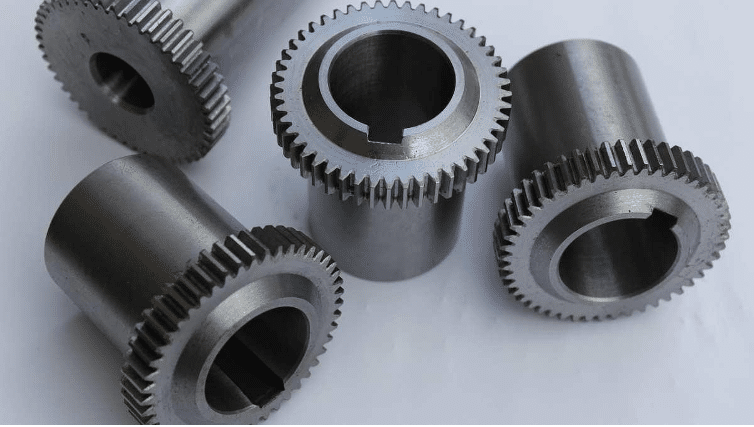
Custom CNC Machined Parts
Tooling allows to design of small and unique parts and components. Machining techniques such as Computer Numerical Control enable designers to come up with complicated shapes and structures because of the flexibility offered in manufacturing.
Compatible with a Wide Variety of Materials
Tooling accommodates many types of material, metals, such as steel and aluminum, and polymers of different types. It enables the material to improve the application and meet strength, durability, and aesthetic needs.
Fundamentals of Tooling Design?
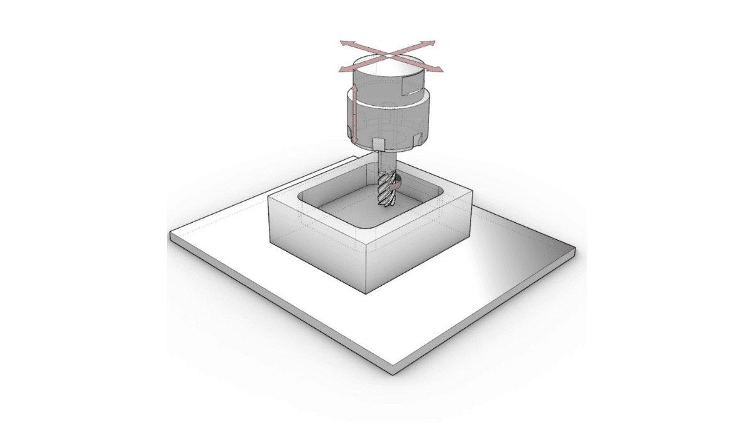
Tooling Design Model
Tooling design is complicated, so, product developers and manufacturers are involved in the decision-making process. Of course, the options available are diverse, but several considerations are relevant to all tools, whatever the aim. Here is the list of fundamentals of tooling design that you should know:
Cycle Times
How often will the tool be needed during the production process? For instance, in the pressure die casting molds, it may cycle every 2 minutes. However, each cycle exposes the tool to high temperature and pressure, thereby making it more susceptible to wear or outright failure if the cycle times are cranked up to reduce processing time.
Another way to increase tool life and processing speed is by applying a thin film. This raises tool costs but is offset by the expected increase in efficiency.
Production Volume and Tool Life
The company does not need to buy several tools for a single production cycle. However, the tools should be made of high-strength materials that don’t bend or break under repeated stress. A long-lasting tool should be able to sustain mechanical, chemical, and thermal stress and at the same time remain accurate.
Nevertheless, durable tools are more expensive in the initial setup and take a longer time to produce than the less durable ones.
Material Used for Tooling
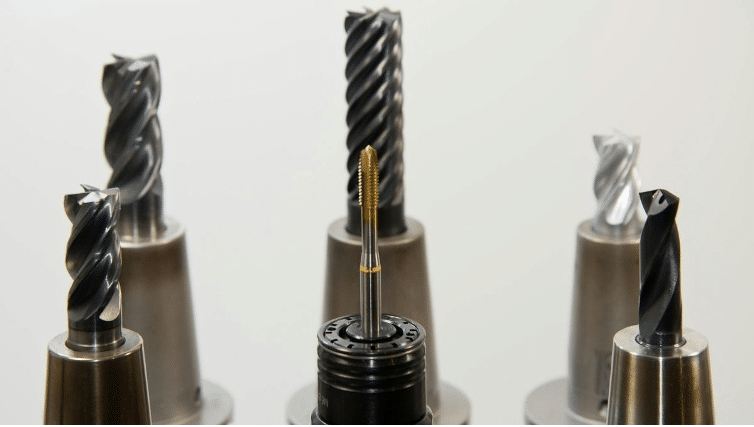
Tungsten carbide Tools
The choice of material for tooling has to be made appropriately. You must have to identify the right balance between performance and time and tool cost depending on the intended use. The typical conditions that determine the choice of material include how precise the part needs to be, how long it needs to last, and how many of the parts are likely to be produced.
For instance, aluminum finds application in injection molding tools while in CNC milling cutters, the common tooling materials used are steel due to the low strength and hardness of aluminum.
Changing Frequency of Tooling
The time it takes to change tools is critical when it comes to increasing the manufacturing throughput. Tools like injection molds are usually big, and cannot be easily moved from one place to another especially when replacement is needed. They need to be replaced using cranes or hoists.
Tool change is an area that warrants improvement in terms of time and cost since the time taken to change tools leads to an accumulation of overhead costs.
Part Precision and Tolerance
If highly precise parts are expected to be produced, there is a need to consider special care when designing the tools to employ. In most cases, these tools lead to increased costs of construction and need more frequent servicing to adhere to tight tolerances.
However well-maintained instruments can last longer through processes such as reshaping or recalibration.
Typical Two Types of Tooling In Manufacturing
Depending on the material, durability, area of use, and manufacturing needs, tooling can be put into two general groups.
Soft Tooling
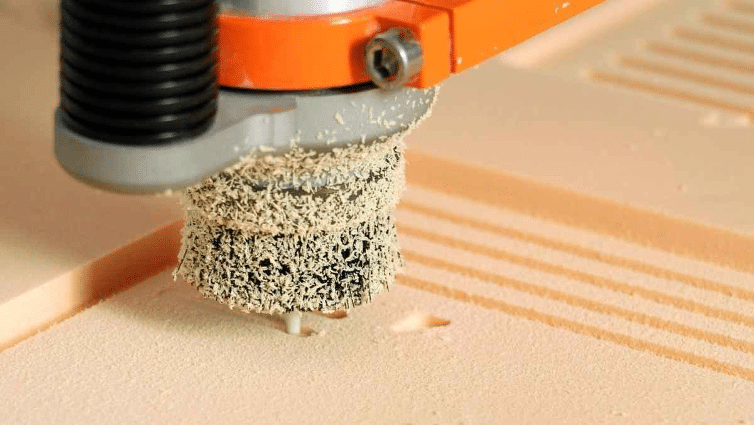
Soft Tooling
Soft tooling is flexible, and less expensive technologies applied to cast urethane molding and is often used when the production volume is medium or low. Among the materials under the class of plastics, silicone is the most frequently used material for soft tooling in industries that deal with prototyping and low-volume production.
Soft tooling enables manufacturers to deal with several materials and is convenient for projects that require limited amounts of material with accurate finishes, for example, prototypes.
Nonetheless, there are a few limitations to using soft tooling as a rig for forming microstructures. It is not as hard nor as wear-resistant as hard tooling. For instance, tools made of silicone must be replaced after making no more than 25 parts. In addition, soft tools are rigid to change and adjust once tooling is done. Hence, you need to select carefully.
Hard Tooling
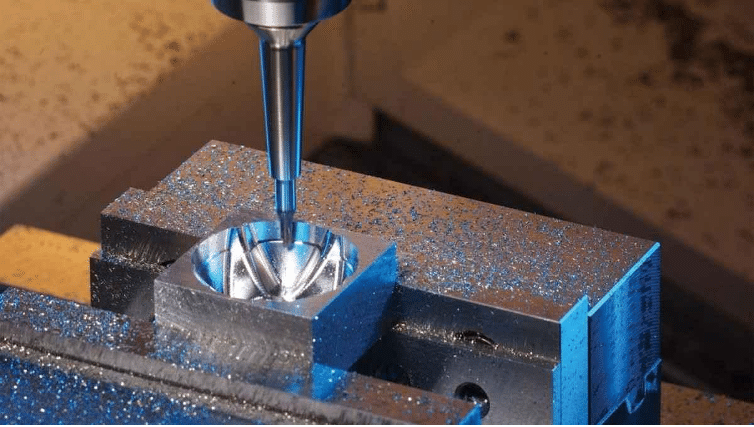
Hard Tooling
Multi-functional hard tooling applied in injection molding is mainly composed of steel or nickel alloy. This type of tooling is reusable for the production processes more than once to make numerous accurate components. Moreover, it’s desirable when it is necessary to maintain close tolerance, test, and functional requirements.
However, hard tooling means higher costs and longer times to produce than soft tooling. Therefore, manufacturing hard tools is a little bit more complex than manufacturing soft tools because, besides the injection process, extra processes like heat treatment, post-processing, and machining are also used to provide the required surface finish, all of which are time-consuming and costly.
Choose the Right One: Soft Tooling or Hard Tooling
Which tooling method should you choose: soft or hard? Soft tooling is mostly accomplished with silicone materials and is most suitable for prototype and small-scale production. It permits easy configuration and adaptation in instances where the project is temporary, or there is limited time required.
In comparison, hard tooling is more long-wearing and can be made of sterner materials, such as steel. It guarantees longer mold life and equal production of quality parts, which makes it ideal for large-scale applications.
Whereas the use of hard tooling, incurs high initial costs, it is cheaper in the long run since the cost of each part produced is relatively low. Soft tooling, on the other hand, requires low initial investment and is appropriate for the early stages of the design.
Different Stages of Tooling in Manufacturing
Tooling manufacturing typically follows three stages: preliminary tooling such as prototype tooling, and bridge tooling, and final tooling known as production tooling.
Prototype Tooling
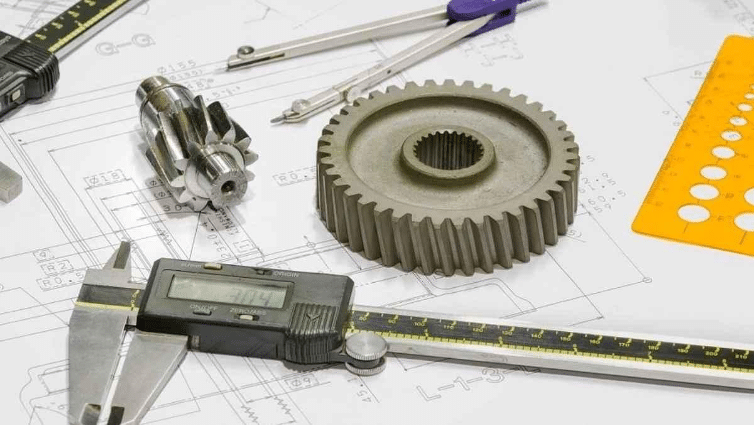
Prototype Tooling
Prototype tooling is the first stage where mold and tool making occur to evaluate a design or to manufacture a small quantity of a particular design. These are single-use tools and are ideal for confirming the correctness of a product design before going to the actual construction.
Bridge Tooling
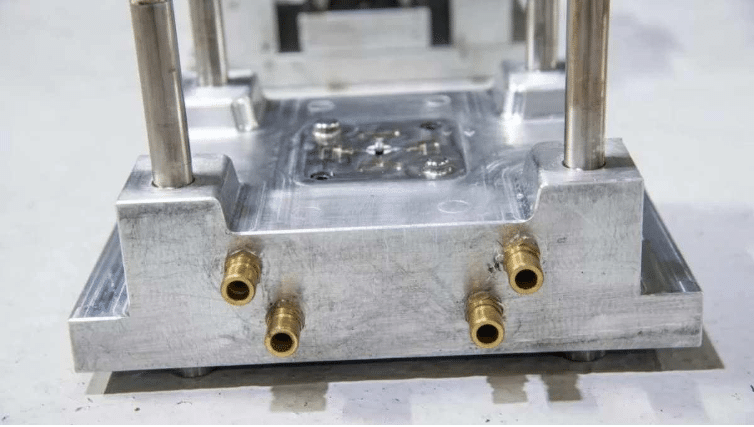
Bridge Tooling
Bridge tooling then is an intermediate stage between a prototype and the final tooling. It is not as sturdy as production tooling, but it can be made rapidly and for a comparatively small price. Moreover, it can facilitate manufacturers to optimize the production flow and complete the product design before the large-scale production.
Production Tooling
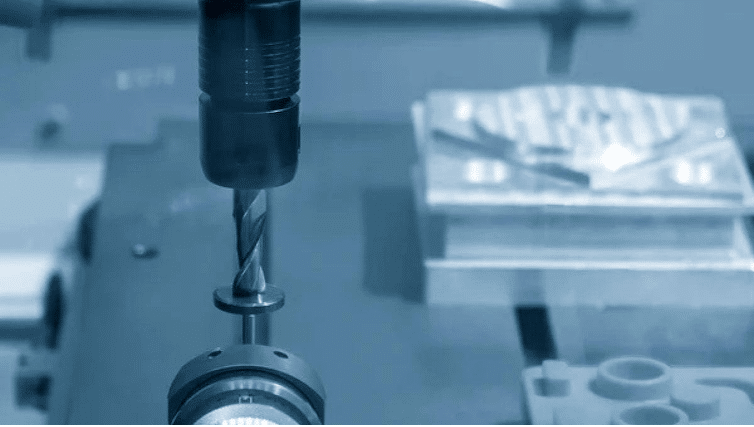
Production Tooling
What is production tooling? Here, the tools used in manufacturing processes require certain tools to be used for many production cycles. Quality is maintained up to the acceptable limit depending on a set quality measurement for the final product. Production tooling is expensive to acquire, but once acquired the cost of using it is significantly low for mass-scale production.
Which Process Are Applied to Create Tooling?
Tooling can be produced through two primary methods: hard and soft tooling. In a competitive environment, soft tooling is cheaper and quicker to manufacture than hard tooling. Generally, soft tooling techniques involve such processes as silicone casting milling, or 3D printing based on the project requirements.
Furthermore, It can be made through Milling or Machining. Hard tooling is sometimes called Progressive tooling. However, it has other production methods, for example, EDM (Electrical Discharge Machining), or precision turning, which are not equivalent to soft tooling.
Metal Materials for Production Tooling
The selection of materials for production tooling is considered to be very important in determining the lasting nature of the tools. They are generally categorized into;
- Tool steel
- Aluminum
- Composites
Consideration and Suggestion when Machining Tooling
In machining tooling, several things are supposed to be put into consideration to satisfy the given project. These include part geometry, tooling lifespan, and materials choices.
Part Geometry
In simpler shapes, soft tooling is cheaper because it takes a shorter time to produce the tools. Such methods as 3D printing or CNC machining are flexible towards change in design and allow for making complex tools in a short time leads.
Tooling Lifespan
Tooling life is a central factor that must be taken into consideration. It’s advisable to go for hard tooling if durability is an important factor. Soft tooling usually can only go through 25–50 shots of injection molding whereas strong tooling based on metals can handle 1000s of shots before becoming a victim of heat or wear.
Material Selection
Selecting the right material for tooling is based on production runs, tool life cycles, and material characteristics.
Conclusion
Tooling is a precise technique of manufacturing involving tools and utensils to shape raw materials into end-use parts. The effectiveness and efficiency of these tools are determinants of the quality of production.
FAQs
Q1. What are the simple parameters for manufacturing tools?
Key features of a manufacturing tool include:
- Core half
- Cavity half
- Runner
- Ejector system
- Cooling lines
- Side actions
Q2. What is rapid tooling?
Rapid tooling makes it possible to make tools just in time; that is before the final tool manufacturing is done during the production of parts in large quantities. The factors of consideration for rapid tooling are the mold material, hand load inserts, and a supplied mold base.
Q3. How much does tooling cost in manufacturing?
Tooling costs vary depending on the product type needed to be manufactured. An average estimate of cost falls between 3% and 6% of the total production cost. As tools are consumables, they are likely to degrade over time. Therefore, will require to be either repaired or replaced.