Have you noticed that your tensile testing machine started delivering inconsistent outcomes or unexpected failures over time? Perhaps the testing process has become slower, or the system seems less reliable even without clear warnings. Even if none of these problems seem obvious at first glance, it does not necessarily mean everything is operating optimally. Subtle declines in efficiency often accumulate over the years, and while your equipment slows down, competitors who invest in newer technologies move ahead.
Modern material testing demands precision, speed, and compliance with constantly evolving standards. Relying on outdated tensile testing machines can negatively impact product quality, delay research and development, and ultimately affect a company’s reputation and bottom line. Understanding when to upgrade your equipment is key to maintaining high performance and maximizing future competitiveness.
Throughout this article, you will discover the key signs that reveal when it is time to replace your tensile testing machine, understand why timely upgrades are a necessity for maintaining quality and competitiveness, and learn how to select the best new system for your testing needs. If you want to stay ahead of industry demands and make the right investment at the right time, continue reading — the insights you will find here could define your operations’ future performance.
Key Signs That Indicate It’s Time to Upgrade Your Tensile Testing Machine
There are many signs that your tensile testing tools may no longer meet modern material testing requirements. Some of these signs are clear and difficult to ignore, such as frequent failures or visible malfunctions. However, many important indicators are far less obvious and can quietly affect your testing processes’ accuracy, efficiency, and reliability without immediate detection. Even if your machine still operates, it does not always mean that it is delivering the performance you require.
Here are some key signs that indicate it may be time to consider upgrading or replacing your tensile testing machine:
1. Frequent Calibration Issues
Frequent calibration problems signal that a tensile testing machine is losing mechanical or sensor precision. If your equipment often requires calibration between scheduled intervals or shows deviations beyond acceptable tolerances, this will negatively affect testing accuracy. Issues such as worn load cells, extensometers, or control systems delay operations and raise uncertainty about data reliability. When recalibration becomes a routine necessity rather than a periodic task, upgrading equipment is the best solution.
2. Inconsistent and Unreliable Test Results
When a machine produces variable results under the same conditions, it indicates internal mechanical wear, sensor degradation, or outdated control systems. Inconsistent outcomes compromise quality assurance, risk non-compliance, and lead to costly retesting or product rejection. If repeatability cannot be restored through maintenance, the machine can no longer support dependable operations and should be replaced.
3. Inability to Meet Updated Testing Standards
Testing standards such as ASTM E8 and ISO 6892 evolve regularly. Older machines may lack the speed control, precision, or reporting capabilities required by new revisions. Operating non-compliant equipment risks losing certifications, failing audits, and reducing market access. Modern equipment upgrades allow laboratories to stay compliant and competitive as standards tighten.
4. Increasing Maintenance and Downtime Costs
Aging tensile testers often require more frequent repairs, causing operational disruptions and rising maintenance costs. Spare parts for legacy models become harder to source, and cumulative expenses for service and downtime can eventually exceed new equipment costs. Prolonging machines past their reliable service life often leads to higher long-term costs and productivity losses.
5. Limited Data Management and Integration Capabilities
Today’s laboratories demand real-time data handling, traceability, and digital integration with LIMS and ERP systems. Older machines with limited memory, outdated interfaces, or incompatible software make data management inefficient and prone to errors. Upgraded systems enable automated reporting, remote access, and easy data exchange, significantly enhancing productivity and compliance.
6. Lack of Flexibility for New Materials or Tests
Advanced materials like composites, ultra-thin films, and high-strength alloys require machines with broader load capacities and flexible testing modes. Legacy machines are often restricted to standard metals or traditional specimen geometries, limiting a laboratory’s ability to expand services or support innovation. Upgrading enables adaptation to emerging material testing needs without major system overhauls.
7. Outdated Software and User Interface
Outdated software can hinder testing workflows, slow down analysis, and expose systems to cybersecurity risks. Older interfaces are less intuitive, increasing operator errors and training times. Modern software provides simplified operation, automated analysis, and compatibility with current IT systems, making testing faster, more accurate, and easier to manage.
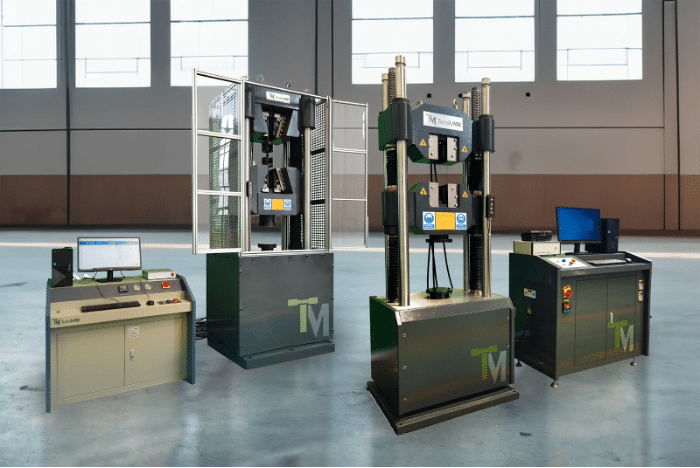
Why It Is Necessary to Upgrade Testing Equipment at the Time
As many signs as there are that suggest upgrading your equipment for tensile testing, there are just as many advantages to making the right decision at the right time. Upgrading is not only about replacing old systems — it is about unlocking new capabilities, improving performance, and protecting your testing operations’ future. Let us show you the key benefits of timely upgrades:
Maintaining Accuracy and Reliability
Aging equipment often suffers from mechanical wear and outdated components, leading to inconsistent and unreliable test results. Such inaccuracies can compromise product quality and safety, especially in industries where material performance is critical. Modern tensile testing machines offer enhanced precision and repeatability, making certain that materials meet specified performance criteria.
Assuring Compliance with Evolving Standards
Industry standards, such as ASTM E8/E8M and ISO 6892-1, are periodically updated to reflect new research and technological advancements. Old equipment may not support these updated testing protocols, risking non-compliance and legal ramifications. Upgraded machines are engineered to meet current standards, facilitating certification processes and providing easy market access.
Improving Operational Efficiency
Outdated testing equipment often requires manual operation, leading to longer testing times and increased labor costs. Modern machines incorporate automation and advanced software, automating the testing process and reducing human error. This efficiency accelerates product development cycles and allows for higher testing throughput.
Reducing Maintenance Costs and Downtime
Maintenance requirements typically increase as equipment ages, leading to higher operational costs and downtime. Sourcing replacement parts for obsolete machines can be challenging and expensive. Investing in new equipment reduces maintenance needs and minimizes unexpected breakdowns.
Supporting Research and Development
In research and development settings, precise and a variety of tests have a fundamental role to play. Modern tensile testing machines offer advanced capabilities, such as high-resolution data acquisition and the ability to test an array of materials under different conditions. These features support the development of innovative materials and products, keeping companies at the forefront of technological advancement.
To conclude, upgrading tensile testing equipment in a timely manner is not merely a matter of replacing old machinery; it is a strategic decision that impacts product quality, compliance, operational efficiency, and innovation. Investing in modern testing solutions allows organizations to achieve accurate results, meet industry standards, and maintain a competitive edge.
Choosing the Right Solution for Upgrading or Replacing Your Tensile Testing Machine
Selecting the right tensile testing equipment is a decision that must be based on a clear understanding of your current needs, future growth, and industry requirements. A well-chosen upgrade or complete replacement can greatly improve testing accuracy, operational speed, and compliance levels, strengthening your laboratory’s capabilities for years to come.
One of the first considerations is defining the expected load capacities and material types you intend to test. Machines designed for small polymer samples, for instance, differ greatly from those intended for heavy-duty metal testing. Selecting a system with the appropriate force range, extensometers, and gripping solutions is key to achieving reliable and consistent results in all applications.
Modern testing also demands advanced data management and connectivity features. The ideal tensile tester should offer automated result logging, smooth integration with laboratory information management systems (LIMS), and compatibility with international testing standards. Software updates, real-time data visualization, and automated reporting functions can significantly reduce operator workloads and minimize human error risk during testing cycles.
It is equally important to consider compliance with recognized industry standards. Machines aligned with standards such as ISO/IEC 17025:2017 and ISO 7500-1 not only help achieve internal quality assurance but also support certification processes required by customers, regulatory bodies, and industry partners. The ability to maintain competitiveness in sensitive industries such as aerospace, automotive, and medical manufacturing becomes increasingly difficult without this level of compliance.
Beyond technical specifications, evaluating service, support, and future expandability is also crucial. Reliable suppliers offer not just equipment but long-term partnerships, assisting with calibration services, machine training, preventative maintenance, and future system upgrades as your laboratory’s needs evolve.
Many companies on the market offer tensile testing equipment and upgrade services, but not all of them are capable of fully meeting the specific requirements of modern testing environments. Choosing a provider that understands technical challenges, compliance standards, and operational needs is a critical step in a successful upgrade. There are established companies, such as TensileMill CNC, that specialize in providing solutions that support the modernization of existing systems as well as selecting new equipment. With the right partner, organizations can achieve faster setup, improved testing accuracy, and compliance with recognized standards like ISO/IEC 17025:2017 and ISO 7500-1, helping maintain long-term testing reliability and laboratory efficiency.
Moving Forward with Confidence in Material Testing
Upgrading your tensile testing machine is not simply about keeping pace with new technologies — it is a necessary step toward protecting the integrity, precision, and reliability of your material testing operations. Outdated equipment can lead to inconsistent results, missed compliance targets, and increased maintenance costs, putting both daily work and long-term competitiveness at risk.
Recognizing when to act and choosing the right solution makes sure that your laboratory meets modern testing demands. New equipment offers better data management, faster testing processes, and alignment with the latest industry standards, helping you stay prepared for future challenges.
Whether you are expanding your laboratory’s capabilities, improving operational efficiency, or responding to updated regulatory requirements, investing in the right tensile testing system is a decision that strengthens your entire testing process. The results of your work will be more reliable, your certifications will be stronger, and you will have a distinct advantage in your field by taking proactive steps today.