Servo controllers are instrumental in automation due to their ability to precisely manage the operation of mechanical systems. These devices regulate speed, position, and acceleration, making them essential in a wide range of automated equipment. This guide delves into the significance of servo controllers, illuminating their functionality, types, and applications.
What is a Servo Controller?
A servo controller is a sophisticated device used to control a servo mechanism. It sends signals to a servo motor about the desired position or speed, adjusting the motor’s output based on feedback from the system. Essentially, it acts as the intermediary between a machine’s digital commands and its physical actions.
How Do Servo Controllers Work in Automation?
Servo controllers operate by receiving input commands from a control system, which are then translated into precise motor output. Here’s how they interact within an automation setup:
- Feedback Integration: Servo controllers continually receive feedback from sensors on the motor’s actual position and speed.
- Signal Processing: They process this feedback to adjust the motor’s operation, ensuring actions meet the programmed specifications.
What Are the Key Components of a Servo Controller?
Key components of a servo controller include:
- Power Supply: Powers the controller and motor.
- Microcontroller: Processes input commands and feedback, issuing motor control outputs.
- Feedback System: Monitors and reports the motor’s actual state (position, speed).
- Amplifier: Boosts the control signals to levels suitable for driving the motor.
- Communication Interface: Facilitates command and feedback transmission between the controller and other automation system components.
What Are the Different Types of Servo Controllers?
Servo controllers vary mainly in their control signals and connectivity:
- Digital Servo Controllers: Use digital signals for enhanced precision and flexibility.
- Analog Servo Controllers: Operate with analog signals, simpler but less versatile.
- Networked Servo Controllers: Connect to industrial networks, allowing for integrated system management.
Why Are Servo Controllers Important in Automation?
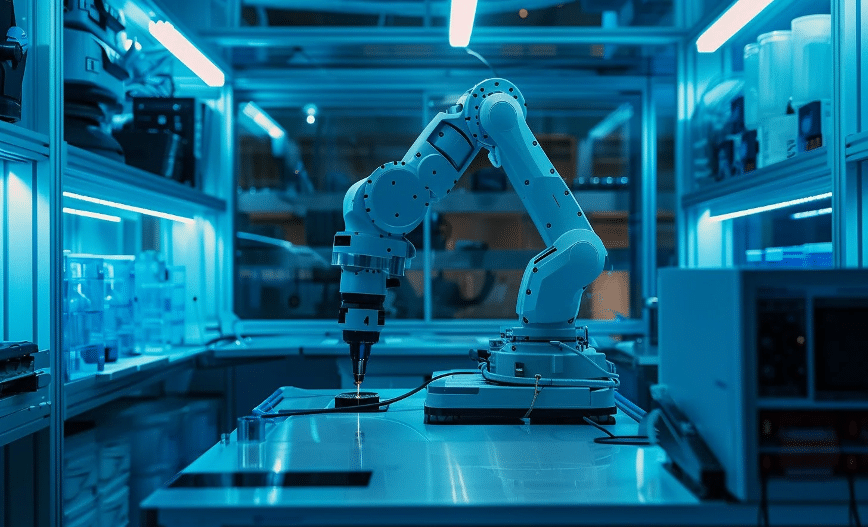
Their critical role in automation stems from their ability to enhance precision, speed, and efficiency. Servo controllers enable complex and delicate tasks to be performed with high repeatability and minimal error.
What Are the Advantages of Using Servo Controllers in Automation?
Benefits of using servo controllers include:
- Precision Control: Allows exact positioning.
- High-Speed Response: Quick adjustment to command changes.
- Improved Efficiency: Reduces energy consumption through precise control.
- Flexibility and Scalability: Adapts easily to different functions and scales.
What Are the Applications of Servo Controllers in Automation?
Applications across various industries demonstrate their versatility:
- Robotics: Used in robot arms for assembly, painting, and welding.
- CNC Machines: Enhances precision in cutting and milling operations.
- Packaging and Assembly Lines: Streamlines processes by controlling machine movements.
- Material Handling and Conveyor Systems: Optimizes the flow of materials across facilities.
How to Select the Right Servo Controller for Your Automation System?
Selecting the right servo controller involves:
- Assessing System Requirements: Understanding the load, speed, and precision needs.
- Compatibility with Existing Systems: Ensuring the controller works with current infrastructure.
- Budget and Cost Considerations: Balancing cost with functional requirements.
What Are the Main Parameters to Consider When Using Servo Controllers?
Key parameters include:
- Torque: The force the motor can exert.
- Speed: How fast the motor can operate.
- Positioning Accuracy: The precision of reaching desired positions.
- Feedback Resolution: The granularity of feedback for adjustments.
How Do Servo Controllers Differ from Other Motion Control Devices?
- Stepper Motors: Generally less expensive but offer less precision and control.
- Variable Frequency Drives (VFDs): Used for speed control in asynchronous motors, not positioning.
What Are the Challenges of Using Servo Controllers in Automation?
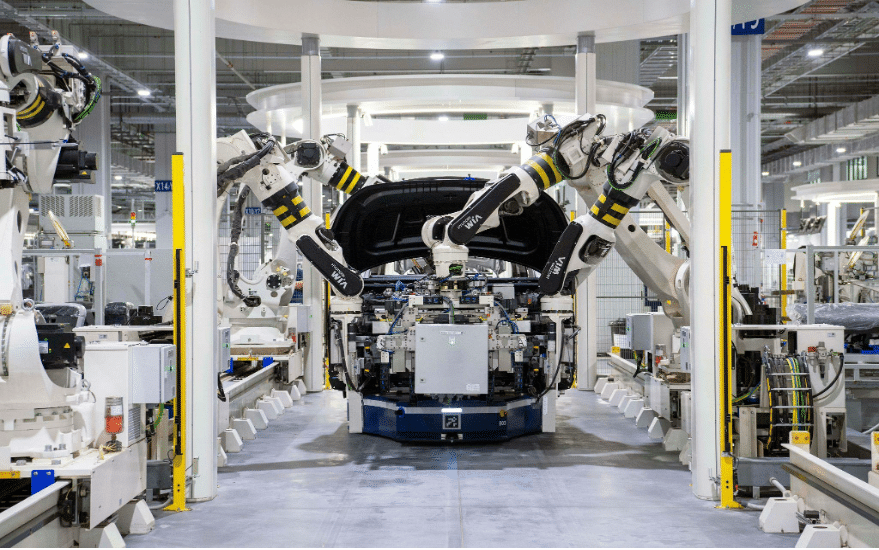
Challenges include:
- Tuning Difficulties: Ensuring optimal settings for each application.
- Complex Programming: Requires detailed programming for precise operations.
- High Costs: Advanced features and functionalities come at a higher price.
What Are the Important Safety Considerations When Using Servo Controllers?
Safety protocols to follow:
- Proper Installation: Ensures the system operates as intended.
- Emergency Stop Systems: Provides a means to quickly shut down in emergencies.
- Thermal Protection: Prevents overheating that could damage the controller or motor.
How to Install and Configure a Servo Controller?
Installation and configuration steps include:
- Pre-Installation Preparations: Checking component compatibility and preparing tools.
- Wiring and Connecting Components: Properly connecting all elements according to the manufacturer’s guidelines.
- Initial Configuration and Calibration: Setting up the controller to meet specific operational needs.
What Are the Common Mistakes to Avoid When Using Servo Controllers?
Avoidable errors include:
- Incorrect Wiring: Can lead to malfunction or damage.
- Improper Calibration: Impacts the accuracy and effectiveness of the controller.
- Neglecting Feedback Loops: Essential for adjusting actions based on real-time operations.
What Are the Maintenance Tips for Servo Controllers?
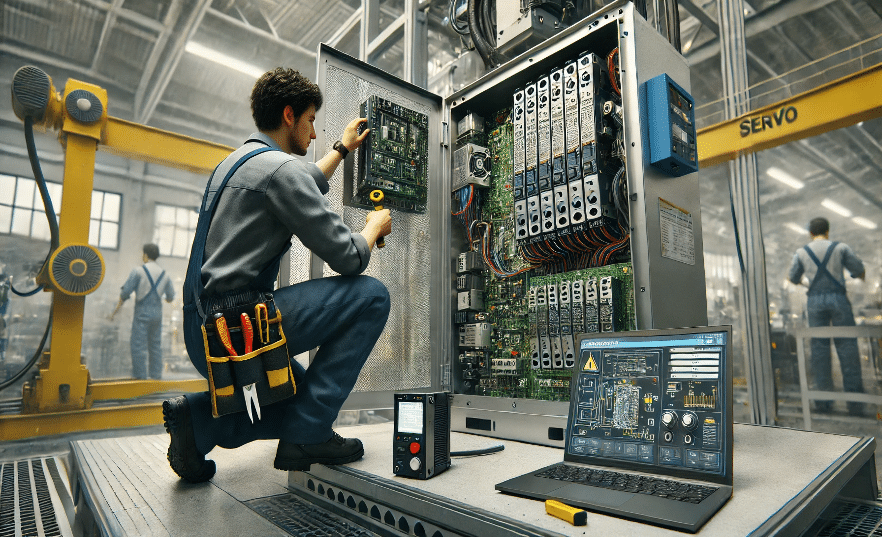
Maintaining servo controllers involves:
- Regular Inspection: Checking for signs of wear or damage.
- Cleaning and Lubrication: Ensuring components remain in good working condition.
- Software Updates: Installing updates to improve functionality and security.
Can Servo Controllers Be Integrated with IoT and Industry 4.0?
Modern servo controllers can connect to IoT, facilitating:
- Real-Time Monitoring: Provides up-to-date information on system performance.
- Predictive Maintenance: Anticipates failures before they occur, reducing downtime.
What Are the Future Trends in Servo Controllers and Automation?
Emerging trends include:
- AI Integration: Enhances decision-making capabilities.
- Enhanced Feedback Systems: Improves the accuracy and responsiveness of controllers.
- Energy-Efficient Designs: Reduces operational costs and environmental impact.
What Are the Best Practices for Optimizing Performance with Servo Controllers?
Best practices include:
- Proper Tuning: Adjusts the controller to perform optimally for specific tasks.
- Optimizing Feedback Systems: Ensures accurate feedback is used for adjustments.
- Using Appropriate Communication Protocols: Facilitates better integration and data transfer.
What Are Alternative Motion Control Devices to Servo Controllers?
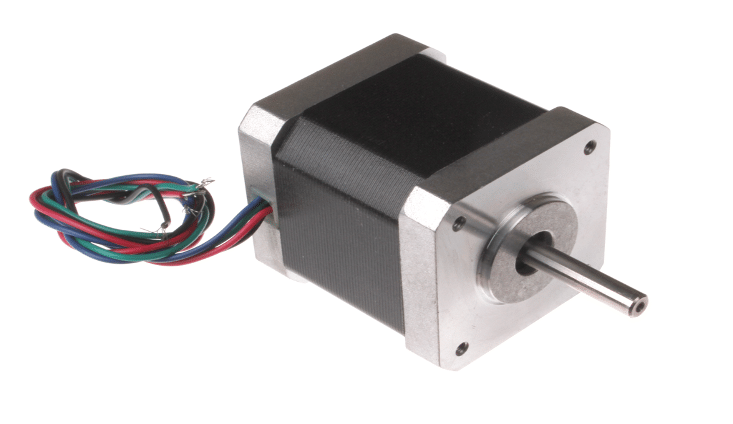
Alternatives include:
- Stepper Motors: Suitable for applications requiring less precision.
- Pneumatic Systems: Offers simplicity and cost-effectiveness for straightforward tasks.
- Hydraulics: Ideal for applications requiring substantial force.
- Rotary Actuators: Effective for continuous rotary motion, providing controlled torque and speed in various automation setups.
Conclusion
Servo controllers are a cornerstone of modern automation, offering unmatched precision, flexibility, and efficiency. Understanding how to select, use, and maintain these devices is crucial for optimizing automation processes and achieving superior operational outcomes. Integrating advanced servo controllers into your systems can significantly enhance performance and extend the lifespan of machinery, making it a strategic investment for any technology-driven enterprise.